As manufacturers continuously look for ways to enhance profits, they are focusing on asset management initiatives to maximize business efficiency and boost the bottom line. Return on net assets (RONA) and overall equipment effectiveness (OEE) are two important indicators companies can use to measure how effectively they utilize their assets in relation to production output, income and expenses – all of which impact profitability.
RONA simply calculates how well a company converts assets to sales, and therefore income. (The simple calculation is sales minus expenses divided by net assets).
By definition, an asset is nothing more than an investment. However, large amounts of assets tie up cash, increase the expense of carrying inventory and reduce profitability.
While all levels of an organization impact RONA, the metric has largely been a concern reserved for upper management. Plant-floor personnel, particularly the maintenance and reliability organization, typically have had little exposure to RONA and don’t understand how their activities can influence this performance equation.
Ironically, it’s this organization that is responsible for driving a large percentage of these profit-influencing activities.
There are three primary ways in which a company can increase its RONA:
-
Reduce costs
-
Decrease expenses
-
Increase sales
Reducing Assets
Inventory, as it relates to spare parts for the automation system, is usually considered a capitalized asset. It’s purchased for its potential to create income. Keeping a well-stocked inventory of spare parts is an important part of the automation system, and while inventory itself is usually considered an asset, money spent maintaining that inventory is expensive.
By properly managing assets, companies can increase RONA by simultaneously reducing expenses and assets. You achieve this by downsizing or eliminating the spare parts inventory (by shifting this responsibility to the supplier); reducing carrying costs associated with maintaining an inventory (such as space, utilities and insurance expenses); and increasing the availability of critical parts to maximize uptime. By having the correct inventory on-site, or readily available, companies can reduce downtime and boost productivity.
Reducing Costs
With manufacturers often allocating as much as 40 percent of their revenues for maintenance department activities, a single process, such as tracking equipment warranties, has the potential to yield significant cost savings.
New electronic manufacturing technologies also are driving cost-saving initiatives. For example, asset utilization software is capable of calculating the production schedule for a particular machine, selecting the optimum time to shut it down for maintenance and issuing the work order. Therefore, these solutions not only improve the flow of information throughout the company, but also address scheduling and procurement functions.
Increasing Sales
To remain profitable, manufacturers need to keep processes running as efficiently as possible. As plant reliability improves, there is a measurable increase in production. When production increases, sales can also increase (assuming the market can sufficiently handle the additional goods). Therefore, equipment reliability can have a significant impact on revenue.
Today, focused process methodologies, combined with sophisticated condition monitoring equipment, are helping boost reliability by providing the tools to collect, analyze and distribute data throughout the enterprise.
Without adequate insight into the health of plant floor equipment, manufacturers lose time and money. When a machine fails, the loss exceeds the simple cost of replacing or repairing the machine. Companies must also consider lost revenue resulting from downtime and the personnel time required to remedy the problem.
Factoring in OEE
OEE is an innovative method to measure productivity performance. More specifically, it is a statistical metric to determine how efficient a machine is running. You calculate it by multiplying a machine’s efficiency, quality and availability. The combination is the value a machine contributes to the production process.
Many companies are developing OEE programs to improve the performance of their maintenance operations. For example, the automatic collection of machine fault data allows the maintenance and engineering staff to analyze the data and determine the root cause of the problem. The maintenance activity is then focused on actual problems and time to repair is reduced. You can use the additional time saved for preventive maintenance.
Every day, thousands of activities are performed on the plant floor that directly impact a company’s bottom line. The ability to harness and measure these activities through powerful asset management tools helps companies improve their RONA and OEE, while providing a distinct competitive advantage.
It also widens the accountability for financial performance from the top floor to the plant floor – a trend that is certain to pay dividends in today’s highly competitive manufacturing market.
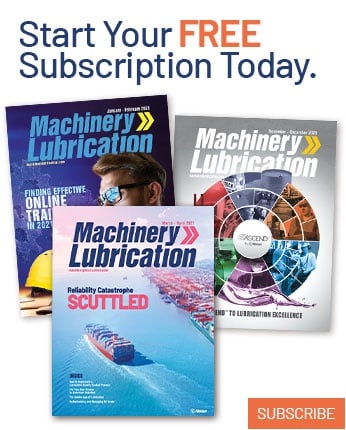