Overall equipment effectiveness (OEE) is the premier standard for measuring manufacturing productivity. Read about how to calculate OEE, the six big losses, OEE benefits and more.
What is Overall Equipment Effectiveness (OEE)?
Overall equipment effectiveness (OEE) is a term used to evaluate how efficiently a manufacturer's operation is being used. In other words, overall equipment effectiveness helps you notice a problem in your operations, identify which percentage of manufacturing time is actually productive and fix it while giving you a standardized gauge for tracking progress. The goal for measuring your OEE is continuous improvement.

How to Use Overall Equipment Effectiveness (OEE) to Measure Manufacturing Productivity
Overall equipment effectiveness is a powerful figure. It provides a lot of information in one number, so there are multiple ways OEE is used to measure manufacturing productivity. When calculated and interpreted correctly, it can significantly maximize your production. Overall equipment effectiveness is used as a benchmark to compare any given production to industry standards, in-house equipment or other shifts working on the same piece of equipment. Standard OEE benchmarks are as follows:
- An OEE score of 100 percent is considered perfect production, meaning you're only manufacturing quality parts as quickly as possible with no downtime.
- An OEE score of 85 percent is considered world class for discrete manufacturers and is a sought-after long-term goal.
- An OEE score of 60 percent is typical for discrete manufacturers and shows there is considerable room for improvement.
- An OEE score of 40 percent is considered low but not uncommon for manufacturers just starting to track and improve performance. In most cases, a low score can easily be improved through easy-to-apply measures.

Overall Equipment Effectiveness is not only a great tool for managers but can have a significant impact on employees working the plant floor. Plant floor metrics can include:
- Target - A real-time production target
- Actual - The actual production count
- Efficiency - The ratio of target to actual; the percentage of how far ahead or behind production is
- Downtime - This includes all unplanned stoppage time for each shift and is updated in real-time.
Overall Equipment Effectiveness: Terms to Know
Before we discuss overall equipment effectiveness further, there are some important terms to be aware of.
- Fully Productive Time - Production time after all losses are subtracted
- Planned Production Time - The total time your equipment or system is expected to produce
- Ideal Cycle Time - The time it takes to manufacture one part
- Run Time - The time your system is scheduled for production and is running
- Total Count - The total of all parts produced including those with defects
- Good Count - Parts produced that meet quality-control standards
- Good Parts - Parts produced that meet standards and don't need to be redone
- Quality - This refers to manufactured parts that don't meet quality-control standards, including ones that need to be reworked. It is calculated as Quality = Good Count / Total Count.
- Performance - This takes into account the number of times there are slowdowns or brief stops in production. A perfect performance score in OEE terms means your operation is running as quickly as possible. It is calculated as Performance = (Ideal Cycle Time x Total Count) / Run Time.
- Availability - This takes into account planned and unplanned stoppage time. A perfect availability score means your operation is constantly running during planned production times. It is calculated as Availability = Run Time / Planned Production Time.
How to Calculate Overall Equipment Effectiveness (OEE)
Before calculating overall equipment effectiveness, it's important to denote the difference between the terms effectiveness and efficiency when discussing OEE.
Effectiveness is the relationship between what could technically be produced and what is actually produced at the end of a production period. For example, if your machinery is capable of making 100 products an hour and it only makes 80, then it is 80 percent effective.
However, this doesn't tell us how efficient the machinery is because we didn't consider things like the number of operators, energy and the materials needed to reach 80 percent effectiveness. For example, if your machinery runs 60 percent effective with one employee and becomes 75 percent effective with two employees, the effectiveness increases by 25 percent, but efficiency decreases to 50 percent based on labor.
There are two main ways to calculate OEE:
- Simple Calculation: The easiest way to calculate OEE is the ratio of fully productive time to planned production time. It looks like this: OEE = (Good Count x Ideal Cycle Time) / Planned Production Time.
- Preferred Calculation: This type of OEE calculation is based on the three OEE factors discussed earlier – availability, performance and quality (good count). It looks like this: Availability x Performance x Quality = OEE. This is the preferred calculation method because not only do you get your OEE score showing how well you're doing, but you get three numbers (availability, performance and quality) showing what caused your losses.

Preferred Calculation Example
Below we'll look at two examples of Preferred Calculation.
Item | Data |
---|---|
Downtime | 5% |
Efficiency | 96% |
Quality (Yield) | 98% |
A widget-making machine with 5 percent downtime (or 95 percent availability) has an efficiency of 96 percent. (ASTM and other governing bodies help determine some machine efficiency ratings. For others, it's as simple as looking at that machine's specific production.) Two of every 100 widgets the machine makes are rejected as being out of specification (98 percent quality). Since OEE is calculated by multiplying the three factors (availability, performance and quality), your formula looks like this: OEE = 0.95 x 0.96 x 0.98 = 89.376 percent
Let's look at a more practical example. A normal shift at a bottling facility takes 480 minutes. Machine operators take three breaks during their shift totaling 50 minutes, and they do two changeovers during the shift totaling 60 minutes of machine downtime for a total of 180 minutes of lost time. To calculate the availability part of the equation, we take:
300 minutes / 480 = 62.5 percent Availability
To calculate the performance part of the equation, let's assume the bottling plant produces 60 bottles per minute. Factoring in the remaining 300 minutes, the bottling system can make 18,000 bottles (300 x 60). Let's say the machines are running slower at 1.5 seconds of cycle time, slowing the maximum speed by two-thirds. This reduces the actual performance to 12,000 bottles. So, to calculate the performance part of the equation, we take:
To calculate the quality part of the equation, let's say out of the 12,000 bottles, 3,000 don't meet quality-control standards, making the quality rate of the bottles 75 percent. The quality part of the equation is calculated as:
Another way to look at it is 3,000 bottles / 60 bottles per minute = 50 minutes lost quality.
So, to calculate the overall equipment effectiveness (Availability x Performance x Quality = OEE), we'd take 62.5 percent x 66.7 percent x 75 percent = 31.25 percent OEE. This means we could technically produce 28,800 bottles, but in the end, only 9,000 bottles are cleared for sale (9,000 / 28,800) = 31.25 percent.

What Are the Six Big Losses When It Comes to Overall Equipment Effectiveness (OEE)?
Perhaps the biggest goal of implementing an OEE program is to reduce or eliminate the most common causes of machine- or equipment-based productivity loss, known as the six big losses. These six losses are broken down into the three main OEE categories (availability, performance and quality).
OEE | Six Big Losses |
---|---|
Availability Loss | Equipment Failure |
Setup and Adjustments | |
Performance Loss | Idling and Minor Stops |
Reduce Speeds | |
Quality Loss | Process Defects |
Reduced Yield |
Available Losses
- Equipment Failure: This is equipment that is not running when it is scheduled for production, causing unplanned downtime. Machine breakdowns, unplanned maintenance stops and tooling failure are common examples.
- Setup and Adjustments: This is production downtime due to changeovers, machine and tooling adjustments, planned maintenance, inspections and setup/warmup time.
Performance Losses
- Idling and Minor Stops: Sometimes called small stops, idling and minor stops are when equipment stops for a short period of time. This can be caused by jams, flow obstructions, wrong settings or cleaning. These issues are usually resolved by the operator.
- Reduced Speed: Sometimes referred to as slow cycles, reduced speed is when equipment runs at speeds slower than the ideal cycle time (the fastest possible time). Worn out or poorly maintained equipment due to poor lubrication practices, substandard materials and bad environmental conditions are common causes of reduced speed.
Quality Losses
- Process Defects: This refers to any defective part manufactured during stable production, including scrapped parts and parts that can be reworked. Incorrect machine settings and operator or equipment errors are common reasons for process defects.
- Reduced Yield: Reduced yield refers to defective parts made from startup until stable production is achieved. Like process defects, this can mean scrapped parts and parts that can be reworked. Reduced yield most commonly occurs after changeovers, incorrect settings and during machine warmups.
Five Benefits of Using Overall Equipment Effectiveness (OEE) to Improve Production
Implementing an overall equipment effectiveness strategy is a powerful advantage in achieving your production targets. It allows you to take a proactive approach by tweaking manufacturing processes in real time, reducing downtime, increasing capacity, reducing costs, improving quality and increasing efficiency. Let's take a look at 10 benefits of OEE.
- Return of Investment (ROI) for Equipment: Companies invest heavily in machinery, so it's important to maximize the return on this investment. If you can use an OEE strategy to produce 15 percent more product on the same equipment in the same amount of time, it can greatly impact your bottom line.
-
Increase Competitiveness: Manufacturers always strive to reduce losses during production to achieve maximum competitiveness. Using data from an OEE report helps you identify bottlenecks or weaknesses in production, allowing you to take immediate action.
Quality and competitiveness go hand-in-hand, and OEE's quality metric can help you identify problems in production causing scrap or rework parts. - Cutting Machinery Costs: An OEE strategy helps you understand your equipment's actual performance so you know whether it is working efficiently. It also alerts you to issues that may lead to future breakdowns and repairs. Overall equipment effectiveness lets you anticipate potential machine failure, reducing maintenance costs and downtime.
- Maximize Workforce Productivity: Use OEE to see why you experience operator downtime, reveal productivity data and pinpoint long changeovers or setup times. Information like this helps you appropriately allot resources, identify where excess capacity is occurring and determine where you need new hires.
- Easily Visualize Performance: Overall equipment effectiveness emphasizes visibility, letting you visualize production problems instead of having to rely on your best guess. By highlighting the biggest sources of productivity losses into one single percentage, everyone can see what's working and where improvement is needed.
Overall Equipment Effectiveness (OEE): A Case Study
Based out of Fort Collins, Colorado, New Belgium Brewing company started as a small-batch hobby brewery and quickly became the nation's third biggest craft brewery (eighth overall) by 2012. Making popular beers such as Fat Tire amber ale, New Belgium quickly found itself struggling to keep up with demand, especially when it came to bottling. With their brewing operations quickly reaching capacity, New Belgium was struggling to identify efficiencies and inefficiencies in their bottling lines. Their goals quickly shifted toward improving OEE. The goals were as follows:
- Increase the brewery's ability take advantage of more manufacturing capabilities.
- Improve Overall Equipment Effectiveness (OEE) so quality products are being produced, production efficiency is managed and make sure the production line is available during scheduled downtimes, package changes and maintenance procedures.
- Operate the brewery at full capacity and double case production.
New Belgium faced a few challenges when it came to meeting their OEE goals. It didn't have any way to view real-time information during unscheduled downtimes on various equipment, causing slowdowns; The production team were constantly reacting to unscheduled downtime on certain assets; and the bottling operation didn't have the ability to predict capabilities, which would allow them to effectively place brewery staff in certain areas to help meet specific production goals.
Over a five-year span, the brewery implemented a series of manufacturing automation initiatives, including an upgrade to their manufacturing automation software system to help streamline its bottling production and figure out its maximum potential. After an audit, the brewery quickly realized its existing lines are capable of producing 294,000 cases a week, but were only producing 150,000 cases a week due to scheduled and unscheduled downtime.
This issue, coupled with its still archaic manual data recording process, which involved managing paper production logs and spreadsheets, wasn't cutting it when it came to keeping up with the level of production the brewery was facing. They realized using a software-based system for production greatly helped in managing the various beer mixes and packaging options, as well as accurately managing scheduled and unscheduled downtime.
Upgrading their automation system also allowed for the massive amounts of data that was being collected to be put into context, making it easier to analyze and be turned int actionable information. This greater visibility of the overall production picture led to a real understanding of the actual production capacity, which helped predictable order fulfillment.
Finally, New Belgium needed a way to react more quickly to unscheduled downtime. Thanks to the data from the upgraded software, the brewery realized it need to increase its maintenance team by 60 percent. They added a process improvement and analysis team, educated key staff in Kaizen processes and trained other team members in Six Sigma to react to issues more quickly.
New Belgium needed an effective way to gather, processes and analyze data to better benefit its overall business production. It had a significant impact on the brewery's OEE:
- OEE increased from 45 to 65 percent in a little over two years.
- Downtime was decreased by over 50 percent.
- Scheduled run time efficiency increased by 25 to 30 percent.
- Production weeks broke records by producing 190,000 to 200,000 cases consistently.
- Packaging area capacity was extended to around 1.3 million barrels a year.
- The brewery maintained lower operating costs by delaying capital investments.
Overall Equipment Effectiveness (OEE) FAQs
How do I know OEE will work for my company?
Overall equipment effectiveness is common in manufacturing plants making individual parts (discrete plants). However, it is also often used in refineries to help identify actual output.
How do I get an OEE score for my entire production line?
The best way to get an OEE score for your entire production line is to measure OEE at the piece of equipment or specific machine that handles the majority of the work. In non-balanced production lines, measure OEE at the point of constraint.
Should changeover, preventative maintenance and lunches/breaks affect my OEE score?
Changeovers are part of one of the six big losses (setup and adjustment) and should be included in OEE. Preventive maintenance and lunches/breaks will probably affect your OEE score as well because they take away time that could be used for production. Exceptions to this include preventive maintenance being done during a planned shutdown and if your machinery can produce parts regardless of whether the operator is on break.
Since a world-class OEE score is 85 percent, should this be my target?
No. While 85 percent is an admirable benchmark, most manufacturers who are new to OEE kick out an OEE score of less than 50 percent. You should set OEE goals that will show improvement over time (usually three to five months).
What's the difference between OEE and TEEP?
Total effective equipment performance (TEEP) measures how much your operation could manufacture if your plant ran 24 hours a day, seven days a week, while OEE measures your productivity during planned production time.
What period of time is used to calculate OEE?
It's up to the manufacturer's discretion, but the most common period of time is one shift. Other time frames include one job, one day or continuous monitoring.
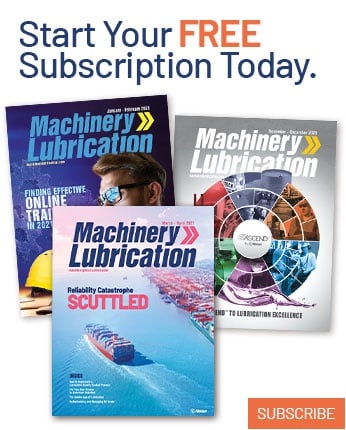