Preventive maintenance is an established routine of periodically inspecting equipment, noticing small issues and fixing them before they turn into major problems. Maintenance crews that practice preventive maintenance are often the unsung heroes of the plant. They're not celebrated for fighting fires because they've recognized the importance of keeping them from starting in the first place.
Contents
- Types of Preventive Maintenance
- Designing a Preventive Maintenance Program
- Preventive Maintenance Tools
- Benefits of Preventive Maintenance
Downtime due to the lack of proper maintenance can cost a company big. It's estimated that running a piece of equipment to the point of failure costs up to 10 times as much as implementing a regular maintenance program would, according to a study from Buildings.com. With around 82 percent of companies experiencing at least one instance of unplanned downtime in the last three years, costing $260,000 per hour, preventive maintenance programs are essential for most organizations. So, what is preventive maintenance?
Preventive maintenance is essentially an established routine of periodically inspecting equipment, noticing small issues and fixing them before they turn into major problems. The ultimate goal of preventive maintenance is nothing breaking down, or zero downtime. The main objectives of preventive maintenance are as follows:
- Enhance asset/equipment productive life
- Reduce critical equipment breakdowns
- Minimize production loss due to equipment failures
A lot of people use terms like preventive, predictive and prescriptive maintenance interchangeably, and while they are in fact different, the latter two can be viewed as types of preventive maintenance. All forms of preventive maintenance help manufacturers move away from a repair-and-replace model to more of a preventive model. Let's take a look at the types of preventive maintenance.
Types of Preventive Maintenance
As eluded to above, any maintenance that isn't reactive – sometimes referred to as "fighting fires" – can be considered preventive maintenance. There are multiple types of preventive maintenance that work in tandem with certain work order software and technologies to help you stay on top of maintenance schedules.
- Calendar-based maintenance or time-based maintenance is performed on equipment based around a schedule on the calendar. In other words, time is the trigger to perform a maintenance task. Servicing your air conditioner every spring or replacing your heating, ventilation and air conditioning (HVAC) unit's air filter every three months are common examples of calendar-based maintenance. Computerized maintenance management systems (CMMS) are often used to keep schedules straight and create recurring work orders when a scheduled task is due.
- Usage-based maintenance employs triggers based on the actual usage of each piece of equipment. Tracking usage with things like equipment monitors and the operating hours of each piece of machinery allows maintenance managers to set up a preventive maintenance schedule based on preset parameters. For example, when machine X reaches a certain number of operating hours, this creates a trigger to schedule a ticket for a maintenance technician to complete required maintenance.
- Predictive maintenance is a form of preventive maintenance (as previously mentioned) and is especially useful when used with CMMS software. Logging work order data into a CMMS lets managers review data and notice patterns in breakdowns over time. This information enables managers to predict when downtime will occur based on historical data and schedule maintenance tasks to prevent it.
- Prescriptive maintenance is similar to predictive maintenance, but it leverages machine-learning software – artificial intelligence (AI) and the internet of things (IoT) connectivity – to help schedule preventive maintenance tasks. Machine-learning software is designed to detect anomalies in a machine's behavior during production. If an anomaly is detected, it's flagged and reported for maintenance. Using AI-enabled prescriptive maintenance not only predicts possible failure but also attempts to provide an outcome-focused maintenance recommendation based on that machine's analytics.
How to Design a Preventive Maintenance Program
Preventive maintenance programs work off a proactive plan, with preventive maintenance making up 60 percent of the maintenance activity. A good preventive maintenance plan involves planning, scheduling, coordination and reliability support across the entire organization. Remember, the goal of a preventive maintenance program is to perform maintenance proactively and routinely to prevent failures before they occur.
If you've already implemented a preventive maintenance plan but haven't thoroughly overhauled it in a while, it's probably outdated. Whether you're updating an existing program or designing a new one, ask yourself the following questions as you're working through a plan:
- How much will a breakdown cost the company?
- What resources and maintenance techniques can be used to detect and prevent failures?
- How often should preventive maintenance be performed?
Let's discuss how to create a quality preventive maintenance program.
_extra_large.jpeg)
- What's your company's end goal? What do you hope to get out of implementing a preventive maintenance program? It's important to design the tasks and procedures in your program around organizational goals. For example, do you want to improve overall efficiency? If so, you might design your program in ways that directly affect reducing downtime and improving work completion rates. If your company's goal is to ensure it remains compliant, you might strive for results like increased planned maintenance and labor tracking.
-
Determine equipment hierarchy. This step involves taking stock of all your equipment or fixed assets and creating a hierarchy structure — the relationship between the most important machines and lower-ranking units. This lets you distinguish on which equipment you can perform maintenance compared with tangible pieces or parts. To determine a hierarchy, your team should discuss the total cost of ownership for each piece of equipment and how safety will be impacted should a component go down.
Look around your plant floor or at a plant floor layout of your assets. Take note of any natural groupings and create parent-child relationships for equipment. Start with the location, then identify the piece of equipment itself, and finally consider the parts that make up that asset. For example:
- Location: Where's the asset located? Note the site, building and/or room.
- Asset: Specifically name the piece of equipment (bottle filler, forklift, etc.)
- Parts: What parts go with the asset(s) (air-operated actuator, forklift motor, etc.)
In this example, the location is at the top of the hierarchy, while the asset (a bottle filler) might be a few levels above the air-operated actuator inside the bottle filler.
Another way to create an asset hierarchy is to use equipment criticality. Your team should ask what equipment failures would have the most damaging effect on production, customer orders or safety should they fail. These would be your highest-ranking assets.
-
Determine job plans. Every preventive maintenance program should include job plans – a list of necessary resources to perform the maintenance work. A job plan should include information on the scope of work and the tools and equipment needed to perform the work. Job plans help organize labor, keeping employees controlled and efficient. Consider including the following in your job plans:
- A step-by-step guide on how to complete the maintenance task
- A specified tool list required to complete the maintenance task
- A list of specific skills needed to complete the maintenance task
- A materials and parts list
- Helpful information like photographs, diagrams or maps
- Standard operating procedures for completing the maintenance task
- Critical safety instructions and procedures to be aware of while working on the task
Planning, along with scheduling, is the most critical part of preventive maintenance. It's been said that for every hour of maintenance planning, you save three hours of time spent on performing the maintenance task itself.
-
Establish long-term scheduling. When it comes to scheduling long-term preventive maintenance, you want to get as many of your critical assets on the schedule as possible. Use the data you collected from your hierarchy and criticality brainstorming session to determine when to schedule specific assets.
For each selected piece of equipment, create a yearly maintenance schedule based on manufacturer recommendations, performance and breakdown history, and input from your team. Plan daily, weekly, monthly, quarterly and annual tasks. A CMMS allows you to automate most of the process by letting you create work orders based on calendar- or usage-based maintenance.
-
Establish short-term scheduling. Once you've established the most critical maintenance tasks for the year, you can easily plan weekly tasks for your team. Short-term maintenance schedules can be layered in with the long-term schedules to ensure thoroughness. In addition to weekly maintenance tasks, weekly preventive maintenance should include things like procedures for completing the task, as well as parts and flex time for emergencies and/or audits. Tips for short-term scheduling include:
- Scheduling prerequisites: For job plans with the lowest required skill level, identify how many people are needed to complete the task, how many hours the task will take and the duration of work (half a day, full day, etc.). It's important to take the time to outline the schedules and job priorities.
- Establish short-term scheduling processes: For job plans with the highest required skill level, schedule multiple jobs for a crew if it's on the same system. Assign a team leader who holds responsibilities such as creating the daily schedules and coordinating resources.
- Set the parameters for scheduling control: Analyze and measure performance by looking at how successful the scheduling process is. Are tasks being completed correctly and on time? Are you still aligning maintenance tasks with your end goal? Always strive for continuous improvement of preventive maintenance scheduling.
-
Provide training. Without proper training, preventive maintenance programs will fail. If employees don't know how to perform the work assigned to them or understand the effect of preventive maintenance on the operation as a whole, the program will never take hold. Proper training shows employees how to perform maintenance correctly, which prevents wasting time on trial and error while also eliminating the cost of repairs due to improper handling of equipment. If your organization is using a CMMS to automate the majority of scheduling, it's critical that employees know how to use the software and see the tasks assigned to them.
In the spirit of kaizen, it's important to clearly communicate and demonstrate the benefits of preventive maintenance to promote and entertain innovative ideas from team members. It is also essential to celebrate successes and involve team members in the program design.
Preventive Maintenance Tools
Modern technology – specifically analytical and scheduling software – is the most common tool to help implement your preventive maintenance program and make it sustainable. Not only does it assist with scheduling, task generation and inspections for short- and long-term maintenance, but it also offers data integration from the data gathered by sensors so you can continuously improve the program.
Computerized maintenance management systems (CMMS) and their mobile apps are some of the most popular systems that maintenance teams use to keep a detailed and centralized record of all work done on each piece of equipment. CMMS software automates work orders, schedules work, manages workflow processes, aids with resourcing and routing, and creates records for reporting and auditing. Basically, a CMMS helps manage maintenance activities while equipment is operational – the time it's functioning as a productive part of the plant. CMMS software assists with executing and sustaining a preventive maintenance program by helping with:
- Task generation: Preventive maintenance tools like a CMMS allow you to easily control a large-scale maintenance calendar by automating meter-based tasks for all equipment. These tasks may include detailed descriptions, how-to documents and other information that may be important to perform the task effectively.
- Task schedules: In addition to task generation, software programs allow you to improve how you schedule them as well. Coordinate schedules based on labor resources and parts needed, and then set up automatic task scheduling in accordance with time- or usage-based criteria.
- Tools and sensors: Integrated with a CMMS, condition monitoring software enables maintenance managers to monitor multiple assets from anywhere. Sensor-integrated software allows for the use of multiple types of alerts for system monitoring and a variety of data graphs for each piece of equipment with real-time information about things like temperature, vibration and power quality.
- Maintenance inspections: Preventive maintenance software tools such as a CMMS allow you to record and track multiple types of data over time, including when inspections and audits occur. With the accurate recording of inspections, the software can automatically generate corrective work orders when equipment fails an inspection.
- Data integration: Not only does data integration help with analyzing asset data, but it also allows for seamless workflows through mobile devices. Maintenance teams can respond to alerts from anywhere and create, access and respond to work orders related to each alert in real time.
You may have heard of other software solutions associated with preventive maintenance, such as enterprise asset management (EAM), asset performance management (APM) systems or enterprise resource planning (ERP) solutions. While these can all be integrated with and supplement the features of a CMMS system, they're generally not good standalone tools for preventive maintenance. For example, an APM works with IoT and AI tools to collect and coordinate data, provide visualizations, and gather analytical data to continuously track the value and risks from each asset.
Integrating your CMMS system with an APM can improve asset reliability and provide valuable data on each piece of equipment as you develop your preventive maintenance program. Keep in mind when developing a preventive maintenance program, you're better off with a tool like a CMMS that focuses on features that assist with daily tasks and routines or calendar-based tasks.
The most common issue with preventive maintenance is when organizations find themselves performing too much or too little maintenance due to the fact that calendar-based maintenance doesn't account for the health of the equipment. Modern technology, such as the tools mentioned above, can help prevent this by optimizing and continuously improving preventive maintenance programs through the use of data.
New and emerging tools and technology are gaining steam and starting to prove useful in fine-tuning preventive maintenance programs. Things like 3D printing for creating spare parts or building molds and tools, embedded sensors to spot early stages of a breakdown, and even using virtual reality for training new technicians in a safe environment while cutting training costs are all modern solutions that help address critical elements of preventive maintenance.
Benefits of Preventive Maintenance
It seems as if organizations are starting to see and accept the benefits preventive maintenance offers. Of facilities that implement a maintenance strategy, 78 percent are switching to preventive maintenance, compared with 61 percent that still rely on reactive maintenance, according to a Plant Engineering maintenance study. Preventive maintenance tools like a CMMS are used by 59 percent of those facilities. Benefits of a preventive maintenance program include:
- Decreased equipment downtime and major repairs
- Increased equipment life expectancy, eliminating premature equipment replacement
- Reduced overtime costs due to employees working on a schedule as opposed to an emergency basis to attend to repairs and breakdowns
- Reduction in large-scale repairs
- Improved safety and conditions for employees
Taking on a proactive mindset by implementing a preventive maintenance program could be a great way for your organization to reduce major costs associated with equipment failure and downtime.
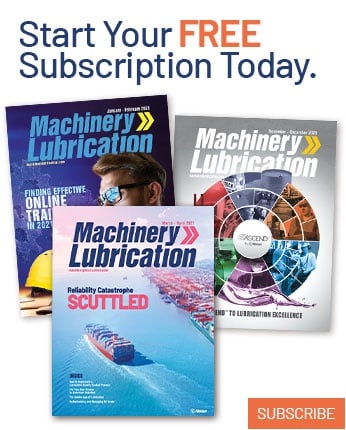