
Maintaining electrical equipment requires much planning and inspecting. Only through planned, periodic inspections will you be able to discover potential breakdowns. An observant workforce can help identify problems with machinery, as their sense of smell can direct them to burning insulation, their sense of touch can detect excess heat in bearings, their sense of hearing can recognize unusual sounds or vibrations, and their sense of sight can spot mechanical flaws and sparks.
Certain devices called motor controls can be used to monitor the operation of electric motors. Motor controls have a number of critical functions, including starting and stopping the electric motor, moving forward or reversing the path of rotation, selecting and regulating the speed of rotation, controlling or modifying the torque/force, and protecting the motor against electrical overloads and errors. Through the years, monitor control command sets (MCCS) have evolved from cabinets with basic electromechanical devices like circuit breakers, contactors and overload relays, to computerized centers that include variable frequency drives.
Below are three key ways to improve the maintenance of your electric motors:
Infrared Thermography
This non-invasive form of inspection employs an infrared camera to observe temperature and thermal patterns when the equipment functions at full load. Infrared thermography is used on a varied range of machinery, including MCCS, and can be helpful in predicting equipment breakdowns and planning corrective actions. It can also be used to detect electrical fault conditions such as loose connections, hot spots, poor contacts, unbalanced loads, overloading and overheating. Keep in mind that safety is essential when it comes to handling electrical equipment. If the machine needs to be scanned while the enclosure is open and the equipment is still running, personnel must follow proper safety measures and wear personal protective gear.
Maintaining De-energized Equipment
This type of maintenance demands more training than visual examinations. Engineers must follow specific guidelines for de-energizing, isolating and preparing equipment for inspection. This would include inspecting and repairing equipment before placing it back into service, verifying that the replaced equipment has the correct rating and is suitable for the application, and referring to National Electrical Manufacturers Association (NEMA) standards.
Maintenance After a Fault
If there is an error, excessive current may damage the MCCS structure, components, bus or conductors. Once a fault occurs, all the required equipment should be disconnected and isolated to prevent contact with live components. It is important to confirm whether the power has been cut off using a digital multimeter. A system can be back-fed if the tiebreakers or other power sources have not been recorded appropriately.
Proper maintenance will increase the life of your electric motors. It can trace potential problems and correct them before a massive breakdown or delay in production. Always follow the manufacturer’s guidelines for maintaining the equipment, lubricating the motor bearings and keeping the motor running smoothly. Finally, be sure that your equipment is well-ventilated and confirm the right voltage and current when performing maintenance checks on your motors.
About the Author
Jeson Pitt works with the marketing department of D&F Liquidators and regularly writes to share his knowledge while enlightening people about electrical products and solving their electrical dilemmas.
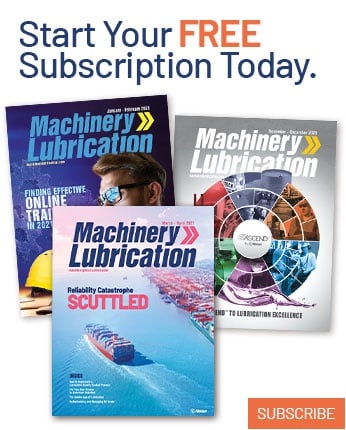