Dynamic electric-motor testing is often called on-line testing because it requires the motor to be running and generally assumes the motor is in its natural environment. Dynamic testing involves the connection of voltage probes and current transformers. Connecting dynamic test equipment is safe, quick and non-intrusive. Data is acquired and results are displayed in a summary format. The collected data is compared to the user-entered nameplate information and is presented in a pass/fail format with both current test data and trending logs displayed after each successive test.
The Need for Motor Testing
Every reliability technician knows that costs associated with motor failures can be devastating to any business operation. Finding that a motor is operating with conditions that create excessive heat or stress is a guide to the technician to make changes in the motor’s operation and to monitor its insulation. Knowing that a motor is in imminent danger of failing provides the technician with time to schedule repairs at his convenience rather than having the motor dictate to him due to a catastrophic failure. Reducing unscheduled downtime while increasing efficiency and profitability are common goals of all reliability technicians. Dynamic motor testing and monitoring is a relatively new concept aiding and advancing the capabilities of those responsible for the safe and continuous operation of electric motors and related equipment.
What Dynamic Testing Tells You
A motor is one part of a complete system that includes incoming power quality, the motor and the driven load. Many motor problems are created by poor incoming power quality, and many more problems can be attributed to the load and load-related issues.
State-of-the-art dynamic motor test equipment is capable of separating electrical issues from mechanical issues as well as defining power-related problem areas. Good test equipment will provide an enormous amount of information regarding the incoming power, including voltage levels, imbalances and harmonic content. A small amount of voltage imbalance will result in a much larger amount of current imbalance and increase losses within the motor. Harmonic distortion also results in wasted energy causing overheating due mainly to non-sinusoidal sine waves. These issues directly affect a motor’s performance and its ability to handle its load. Overall, poor power quality manifests itself as higher heat within the stator and rotor, reducing efficiency and eventually resulting in premature motor failures. Monitoring power quality and making necessary adjustments are essential in maintaining motor longevity.
Besides power condition, dynamic testing provides extensive information about the motor’s behavior and offers evidence of potential mechanical problem areas. The test equipment tracks current levels and unbalances, load levels and torque-related information. Combining this data with the power quality information, the equipment can predict de-rating factors that indicate potential problem areas.
Torque and torque ripple add another piece of the puzzle that is required for consistent and accurate diagnosis of the motor’s health. Torque ripple is defined as the division of maximal torque divided by average torque during the acquisition period. The torque ripple itself is a measure of how small the torque band is that surrounds a steady state average torque. Torque ripple is independent of power condition and current level. It provides a visual look at how the driven load is performing and is an indicator of rotor stress.
Dynamic testing can identify rotor bar problems with a high degree of accuracy, and trending logs make tracking them over time easy and predictable. Rotor bar and cage defects result in lost efficiency and higher heat culminating in premature motor failure.
Measuring and tracking efficiency is a very difficult task. The operating efficiency of a motor cannot be easily measured in a field application. Many standards have a number of requirements that commonly can only be fulfilled in a laboratory environment. These standards also usually concentrate on ensuring a proper description of a motor's capabilities under good operating voltage conditions. In the field, however, there is little room for requirements like uncoupling a motor or regulating the voltage level for a saturation run. Questions regarding a particular motor's capabilities are found to be secondary in importance when compared to the operating efficiency under the given conditions in the field. The result of such an environment is that true efficiencies are unrealistic to obtain.
Operating efficiencies, however, are of crucial importance to an energy-conscious management. The requirements for a true measurement of operating efficiency in a field environment are ample and unrealistic (like installing torque transducers on the shaft of the motor and measuring the input power to the motor at the motor terminals, frequently at high voltage levels). Instead of true efficiency measurement, efficiency estimation becomes the only field-friendly approach for energy management. The difference between operating efficiency measurement and operating efficiency estimation is that the former attempts to find the true operating efficiency via direct measurement, while the latter accepts a small measure of inaccuracy for severely increased user friendliness.
Case Studies
In a controlled laboratory experiment, vibration analysis and dynamic data were acquired on a new 5-horsepower, 460-volt motor. The motor was disassembled, and the outer race of the drive-end bearing was intentionally damaged (Figure 1).
Figure 1
The motor was reassembled, and new data collected. The common formula used in vibration analysis was applied to the data acquired, and the results were posted on both the vibration spectra and the torque spectra.
The resulting calculations concluded that the outer race defect should appear at 107 hz with sidebands related to the motor speed in the vibration spectra and twice the fundamental frequency in the torque spectra (Figures 2 and 3). The outer race defect with its sidebands was much easier to determine in the dynamically acquired data than the vibration spectra.
Figure 2. Vibration spectra
Figure 3. Demodulated torque spectra
Rotor Bar Problems
In another laboratory-controlled study, a 1-horsepower motor running under full load on a small dynamometer was tested thoroughly with the dynamic tester. The results were then saved and analyzed. The rotor was removed, and a 5/8-inch hole was drilled through one rotor bar, severing it completely. The motor was assembled and retested under identical conditions. Again, the results were saved and then compared to the original data (Figures 4 and 5).
Figure 4
Figure 5
The broken rotor bar was clearly defined in the current signature analysis without any difficulty or intensive diagnosis.
Cavitation
At a large electric power plant in North Carolina, mechanics noticed that one of three 15,000-horsepower pumps developed a lower flow level than the other two. The mechanics blamed the motor, while the electricians maintained the pump was at fault. Dynamic electric data was acquired and analyzed. Figure 6 shows the resultant torque ripples.
Figure 6
One pump displayed the large variations in the torque ripple, while the two pumps that were operating normally had the smaller torque signature. As a result of this testing, a diver was sent into the pit and found that the bolts on one end-bell had rusted off, allowing the flute that directed water into the pump to fall off. This situation caused the pump to circulate water outside the pump and created cavitation. Bolts on the other pumps were also in need of replacement and would have failed in the near future. The downtime required to make the repairs cost the facility several million dollars, but the increased productivity after the repairs easily compensated for those costs.
In conclusion, dynamic motor testing and the state-of-the-art equipment available today are rapidly becoming the tools of choice for reliability technicians worldwide. The technology is quite young, and new innovations are continuously expanding its capabilities and horizons.
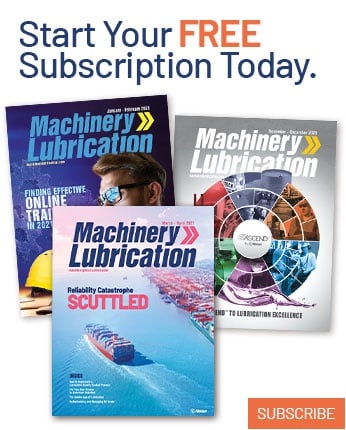