Widely publicized estimates show that systems driven by electric motors consume more than half of the electricity produced in the United States and more than 70 percent of the electricity used in many industrial plants.1 Now that energy and operating costs are at a premium, it makes more sense than ever to increase motor efficiency.
Many facilities find it makes sense to divide their motor efficiency strategy into three phases:
- Overall assessment
- Immediate improvements
- Long-term
This article briefly outlines Step 1 and provides details on Step 2. An upcoming article will provide details for Step 3.
Methods to optimize electric motor efficiency
Phase 1: Assessment
Here’s what a motor assessment involves:
- Survey and document how many motors, at what age, horsepower and ratings, with what level of controls are present in your facility.
- Identify the highest and most critical loads.
- For those key units, use a power logger to evaluate their energy consumption (power draw).
This will give you a general energy-consumption map for motors in your facility.
Phase 2: Immediate improvements
There are two kinds of immediate improvements that you can make.
- Changes to the units and to unit operation
- Repairs
Changes to the units may include replacing some motors with higher-efficiency or better-sized models, adding controls to others to right-size output, and rescheduling which motors run when compared to demand and utility rates.
To determine whether any of these changes make sense in your facility, use a motor efficiency calculator such as MotorMaster+ from the U.S. Department of Energy. It can help you calculate savings per motor and per efficiency step.
Otherwise, there are three inspection points that you should make to all motors that you intend to keep operational:
- Voltage unbalance
- Current unbalance
- Power factor
If tests show problems with any of these three variables, correcting those problems can yield immediate efficiency improvements. Logically, you should also incorporate these tests into long-term regular maintenance to sustain any short-term improvements you make at this stage.
Voltage unbalance
Voltage unbalance is a measure of voltage differences among the phases of a three-phase system. For optimum motor performance, the phase voltages should be equal or very close to equal. Besides causing poor motor performance, voltage unbalance shortens a motor’s life.
Voltage unbalance is 100 times the maximum voltage variation from average divided by the average voltage of the three phases. This calculation produces the unbalance as a percentage. The U.S. Department of Energy (DOE) presents the following example:2 If measured line voltages are 462 V, 463 V and 455 V, the average is 460 V. So, the voltage unbalance is:
[(460 – 455) x 100] ÷ 460 = 1.1%
Overall, voltage unbalance should be less than 1 percent and never more than 5 percent. Standard EN50160 requires less than 2 percent voltage unbalance at the point of common coupling. National Electrical Manufacturers Association (NEMA) specifications call for less than 5 percent for motor loads, but recommend that voltage unbalances at motor terminals not exceed 1 percent and that the motors be derated for higher percentages.3
Measuring for voltage unbalance should be performed regularly at motor terminals using a power quality analyzer to verify that voltage unbalance is below 5 percent. In addition, regular thermal inspections might reveal high-resistance connections in the switchgear, disconnects or motor connection boxes, which can cause voltage unbalance. Other possible sources of voltage unbalance include faulty power-factor correction devices, unbalanced or inconsistent supply voltages, unbalanced transformer banks, unevenly distributed single-phase loads, single-phase to ground faults or an open circuit on a distribution system primary.
Corrections should be done by an experienced electrician or power specialist. Begin by checking supply voltages from the adjustable speed drive (if one is used in the system). Also, check utility inputs to the plant and transformer outputs to the system. If balanced phases are found at these “sources,” then the best approach is to begin at the motor and systematically work back to the initial source, the utility’s electric supply.
Potential savings and ROI: The best way to calculate overall savings is to use a software tool such as MotorMaster+. Here’s how the basic calculation works, if you know the following (sample values appear in parentheses):
- Loading on the motor (100%)
- Horsepower (100 hp)
- Run time (8,000 hours per year)
- Efficiency at nominal unbalance for the loading (94.4%)4
- Efficiency at actual unbalance and loading (93%)
- One horsepower converts to 0.746 kilowatts
Using the sample values provided, the annual energy savings (AEs) following corrective action would be:
AEs = 100 hp x 0.746 kW/hp x 8,000 hr/yr x (100 ÷ 93 – 100 ÷ 94.4) = 9,517 kWh
If electricity costs $0.05 per kWh, the annual saving in dollars (AS$) will be:
AS$ = 9,517 kWh x $0.50/kWh = $476/yr
In industrial settings, many motors may be powered from the same unbalanced power supply. Therefore, potential savings will be much more than for a single motor, with the actual savings dependent on loading, run times, horsepower, etc.
Finally, remember that motors run hotter when their power supplies are unbalanced; roughly twice the square of the voltage unbalance (2 x % voltage unbalance). For example, at 2 percent voltage unbalance, a motor will experience an 8 degree Celsius temperature rise. Every operating temperature increase of 10 degrees C halves the life of motor-winding insulation.
Current unbalance
Current unbalance is a measure of difference in current drawn by a motor on each leg of a three-phase system. Correcting current unbalance helps prevent overheating and the deterioration of motor-winding insulation. The draw on each leg should be equal or close to equal. One cause of current unbalance is voltage unbalance, which can cause current unbalance far out of proportion to the voltage unbalance itself. When current unbalance occurs in the absence of voltage unbalance, look for another cause of the current unbalance (e.g., faulty insulation or a phase shorted to ground).
Current unbalance is calculated the same way as voltage unbalance. It is 100 times the maximum current variation from average divided by the average current of the three phases. So, if the measured current is 30 amps, 35 amps and 30 amps, the average is 31.7 amps, and the current unbalance is
[(35 – 31.7) x 100] ÷ 31.7 = 10.4%
Current unbalance for three-phase motors should not exceed 10 percent.
Measuring current unbalance should involve an experienced electrician or power specialist. As with voltage unbalance, it should be performed regularly at motor terminals using a power quality analyzer. The two measurements for unbalance – voltage and current – can be made and saved simultaneously with the same power quality analyzer.
Correcting current unbalance might include any or all of the following strategies:
- If the unbalance is the result of the supplied power, a power-factor correction device can solve the problem.
-
If the problem is the motor itself, due, for example, to faulty insulation or a phase shorted to ground, carefully weigh your options. The decision to repair (rewind) a motor vs. replacing it with a new one is difficult. According to the DOE4 …
- Rewinding almost always reduces a motor’s efficiency and reliability. Consider such variables as rewind cost, expected rewind losses, new motor purchase price (for both standard and energy-efficient models), motor size and original efficiency, load factor, annual operating hours, electricity price, availability of a utility rebate and simple payback criteria.
-
In most cases, buy a new motor if:
- the faulty motor is less than 40 horsepower and more than 15 years old, especially if it has been previously rewound,
- the motor is a non-specialty motor of less than 15 horsepower, or
- the rewind cost is more than 50 percent of the cost of a new motor.
In the latter case, increased efficiency and reliability should provide a fast return on investment.
Potential savings and ROI: ROI takes two forms – energy savings and long-term production savings (preventing motor failure and downtime). Possible utility rebates also come into play.
Energy savings can be difficult to determine, especially when rewinding is the chosen solution. Final rewind losses are unknown until after rewinding.
If you decide to buy a new motor, use MotorMaster+ software to calculate the annual energy savings (AS$) you can expect from the replacement. You need the following information:6
- Motor rated horsepower (hp)
- Load factor (L = percentage of full load ÷ 100)
- Annual operating hours (hr)
- Average energy costs (C = $/kWh)
- Existing motor efficiency (Estd, as a percentage)
- Efficiency rating of the new motor (Eee, as a percentage)
- The conversion factor from hp to kW (0.746)
Given this information,
AS$ = hp x L x 0.746 x hr x C x [(100 ÷ Estd) – (100 ÷ Eee)]
In general, premium-efficiency motors are about 1 percent more efficient than standard efficiency motors, and the energy savings will typically result in a payback period of less than 18 months. Compared to an existing rewound unit, a new premium efficiency motor will be considerably more than 1 percent more efficient.
Power factor
Bad power factor is generated by some types of equipment operation and results in penalty fees from the utility. Evaluate power factor on all major circuits and loads, including motors. The closer your power factor is to 100 percent, or “1”, the better (utilities usually charge a penalty for power factor less than 95 percent). Increasing your power factor will:
- Reduce your electric bill
- Increase electrical system capacity
- Decrease voltage drop
Power factor (PF) is caused by inductive loads (loads with coils) such as motors and transformers. It is expressed as a percentage or a number, with 100 percent, or 1, being ideal. Power factor is the ratio of real (working) power (kilowatts kW) to apparent (total) power (kilovolt-amps kVA). Apparent power is a combination of real power and reactive power (kilovars kVAR).
An increase in reactive power causes the apparent power to increase and, consequently, power factor to decrease. So, decreasing reactive power will increase power factor, and that’s generally a good thing.
Measuring power factor is best done with a power-quality analyzer. Before starting, find out:
- How your utility charges for low power factor or VARs
- What the utility says your power factor averages per month
- What your demand charge is
- How the utility measures power factor or VARs: peak intervals or averages?
The goal is to identify loads that are causing lagging reactive power and develop a strategy for improving power factor.6
Start at the service entrance, where the utility monitors its data, and check individual loads. The power-quality analyzer will allow you to find the average power factor over a specific recording period.
Correct power factor using the following strategies:
- Curtail or decrease the use of idling or lightly loaded motors
- Avoid operating motors above their rated voltage
- Replace failed standard motors with energy-efficient models
- Install capacitors in the affected circuit(s) to decrease reactive power
Potential savings and ROI: Use the information from the utility and from your investigation to calculate your savings. Let’s assume your utility adds a 1 percent demand charge for each 1 percent your power factor is below 0.97 percent. If your power factor averages 86 percent each month, then your operation is 11 percent (97 percent minus 86 percent) below the 97 percent threshold. If your demand charge is $7,000 per month, then your avoidable annual cost via power factor correction equals:
(11% x $7,000 per month) x 12 months = $9,240
Next steps
As you wrap-up your immediate motor efficiency investigation, evaluate your long-term maintenance practices and start making changes there, too. Include these same voltage and current unbalance checks in regular inspections. Also consider regularly inspecting connections and grounds, off-design voltage, and insulation resistance, for additional long-term performance improvements.
This article is courtesy of Fluke Corporation. To learn more about this subject, visit www.fluke.com.
Notes
1 Fact sheet: “Optimizing Your Motor-Driven System”. a Motor Challenge document. Motor Challenge is a program of the U.S. Department of Energy (DOE). For more details, visit http://www1.eere.energy.gov/industry/bestpractices.
2 Motor Systems Tip Sheet #7 (Sept. 2005): “Eliminating Voltage Unbalance”, an Energy Tips – Motor Systems document written for DOE’s Industrial Technologies Program.
3 Determining outside the laboratory the efficiency of a motor is difficult and involves extensive labor and equipment. Furthermore, ±1% in efficiency will significantly impact calculated dollar savings. (See Motor Systems Tip Sheet #2 (September 2005): “Estimating Motor Efficiency in the Field”, an Energy Tips – Motor Systems document written for DOE’s Industrial Technologies Program.) When the percent loading is known, MotorMaster+ 4.0 software automatically chooses the as-loaded efficiency based on available data.
4 Fact sheet: “Optimizing Your Motor-Driven System”.
5 From DOE’s fact sheet: “Buying an Energy-Efficient Electric Motor”, a Motor Challenge document; Question 5: “When is an energy-efficient motor cost effective?”
6 See DOE’s fact sheet: “Reducing Power Factor Cost”, a Motor Challenge document.
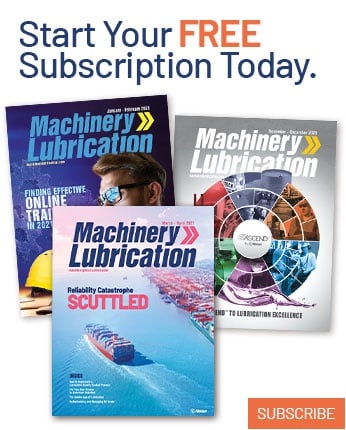