The words in the title of this article, which were spoken by Taiichi Ohno, have been one of his most popular and well-known sayings within our lean community. Typically, we use his famous words to stress the importance of establishing standard work as a baseline to measure any changes to signify actual improvement in our process.
Without standard work, we cannot be sure what impact our changes had on our process. The emphasis of standard work is clearly placed at the beginning of the kaizen process.
We teach the kaizen process to be four distinct steps:
-
Establish the existing standard work.
-
Analyze the current process.
-
Make improvements (Plan-Do-Check-Act).
-
Document the new standard work.
From these steps, we see that standard work is both the beginning AND the end of the kaizen process cycle. Not only is standard work required to begin kaizen, we also need standard work to finish kaizen.
How many kaizen events do we conduct where establishing the new standard work is not completed by the end of the event? Does our activity to document the new standard work normally end up on our homework list? What happens to our kaizen if the new standard work is not documented?
Documented standard work is just a simple written description (with pictures) of the safest, highest-quality and most efficient way known to perform a given task or process. It is best written by the associates who actually perform the task and should be written in the most direct and simplest form possible.
How many tasks and processes do we perform daily where there is no documented standard work? How many of the tasks or processes have changed while our documents remain the same, making them outdated.
In my experience, we do not place enough emphasis on documenting the new standard work in our kaizen event process, so we easily backslide. The result is still the same. If you don’t document the improvements into new standard work, there is no kaizen.
About the author:
Mike Wroblewski started his lean journey with instruction in quick die change from Shigeo Shingo. Mike is currently the lean sensei at Batesville Casket Company in Batesville, Ind.
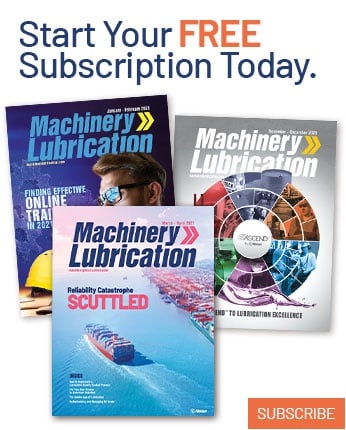