Manufacturing organizations make every effort to build the finest products available with unsurpassed quality, reliability, performance and value. This ultimately earns the customers' trust and strengthens their loyalty to the brand. However, these four elements (unsurpassed quality, reliability, performance and value) can run considerably deeper. They must apply to the people as much as to the product.
Often manufacturing organizations engage in kaizen (change for the better) to eliminate waste, improve procedures, maximize flow and ultimately create value for the customer. Continuous improvement organizations also continually monitor their processes through time study and observation.
They improve the inputs to the process to generate the desired output. This is all noble because processes can continuously be simplified to increase value. What is often overlooked is taking this recurrent observation and kaizen approach to the development of people. After all, people are an input to the stream as much as the tools and materials they use.
Organizations should consistently invest and develop people in continuous improvement to increase their performance, reliability, quality and value. Of course, this investment would mean that the training process and the progress of each individual are recurrently observed. Granted, this requires resources, time, commitment, conviction and faith.
Edward Deming once said, "The most important things cannot be measured." What's the benefit of spending money on training and development? You will never be able to measure it.
Why did you do it? Because you believe it will pay off – and it most certainly will. Increasing the overall human capital will produce what many organizations dream of, a truly sustainable continuous improvement culture. Over time, this program will not need as much recurrent observation due to the fact that the investment has created an intrinsic value in people. The culture actually becomes self-sustaining.
Once people value continuous improvement and see the use and benefit of the tools and the mindset, they want it and have the desire to help others understand it. Employees will begin to train new recruits with these values and theories as well as discuss it on the floor with their leads, engineers, managers and supervisors. They soon come to the plant to think not just to work.
In tandem, the organization is developing its future leaders with the foundation of continuous improvement. Eventually, there will be passionate waste eliminators and creative problem solvers at every level of the organization. The leaders will also be passionate about creating future leaders and assisting in the development of their employees and colleagues.
Just as the manufacturing organization strengthens the customers' loyalty to the brand by delivering quality and value to them, the organization strengthens the employees' loyalty to the company by delivering value to them.
This value is to kaizen, train and invest in the people. Increase their knowledge, abilities and opportunities through training, coaching and "learning by doing." This is an investment in culture and will take time and commitment. In the end, it's an investment that will yield results for years to come.
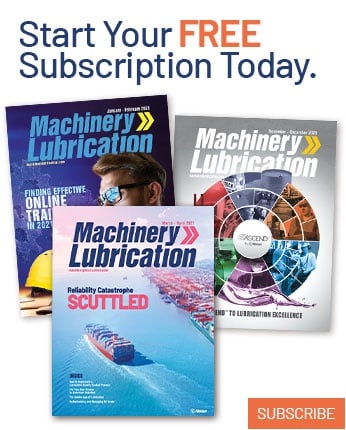