Kaizen is a philosophy that when fully adopted, creates a culture of continuous improvement. Read about kaizen, what it is, how to use it and more.
Contents
- What Is Kaizen?
- The Types of Kaizen
- The Kaizen Approach
- How Kaizen Reduces Waste
- Pros and Cons of Kaizen
What Is Kaizen?
The word "kaizen" is a Japanese word meaning "change for the better." In English, kaizen translates to "improvement" and encompasses both short- and long-term improvement processes. In lean manufacturing, kaizen refers to brainstorming ideas and implementing daily activities that continuously improve processes. It involves all employees – from the higher-ups to plant-floor workers.
The goal of kaizen is to "go lean" with manufacturing processes by improving current standardized processes and programs to eliminate waste and increase efficiency. Kaizen is sometimes referred to as part action plan and part philosophy. Action plans consist of organizing focus groups or teams and events set on improving specific areas within the organization. Teams should include employees from all levels and focus heavily on employees on the plant floor.
The philosophy of kaizen involves building a workplace culture that encourages active engagement in suggesting improvements and employing new standards. For a manufacturing company to truly go lean, this philosophy must become a way of thinking for both upper-level managers and plant-floor employees.
You may have heard of the term "standardized work." Kaizen goes hand-in-hand with this concept. Standardized work outlines current processes or best practices, while kaizen strives to improve upon those processes. Standardized work is seen as a living document that kaizen continuously improves. Let's take a look at the different types of kaizen, how to approach implementing kaizen into your existing processes and how kaizen can benefit your organization by eliminating waste.
The Types of Kaizen
There are multiple ways in which kaizen can be applied in your organization; some are short-term approaches that happen quickly, and others take a little more strategic planning in the form of a kaizen event.
- Point kaizen: Point kaizen is a very popular way to implement the philosophy thanks to its quick approach and the minimal planning it requires. Once someone notices a broken process or incorrect action, it is immediately addressed, and measures are taken to correct the problem. An example of point kaizen might be a supervisor doing a floor inspection and noticing a defect in equipment or a delay in a process. He or she then might ask the floor manager to perform a quick kaizen to remedy the issue.
- System kaizen: The opposite of point kaizen, system kaizen is meant to address system-level problems within an organization. It's an organized, upper-level, strategic-planning method meant to produce multiple planned kaizen events over an extended period of time.
- Line kaizen: Line kaizen refers to utilizing lean techniques in both an upstream and downstream department or process, thus forming a line between the two. For example, a short-term kaizen event might be implemented in the planning department and in the procurement department. Planning is upstream from procurement, which directly affects procurement.
- Plane kaizen: Plane kaizen is also referred to as value streams (several lines connected together) and is a level above line kaizen. Value stream forgoes traditional departments within an organization and structures it into product lines (value streams). In other words, changes in one line are implemented into other lines and/or processes.
- Cube kaizen: Cube kaizen refers to a situation where all points of the planes are connected to each other, resulting in lean processes across the entire organization. Improvements are made upstream, downstream and throughout the entire organization, including suppliers and customers. Often, cube kaizen requires amending standard business processes.
The Kaizen Approach
Since kaizen is about continuous improvement, it's not just a one-time event but rather a deliberate mindset of always thinking of ways to improve efficiency. This approach to continuous improvement is typically broken down into six steps.

- Brainstorm/Standardize: With a cross-functional team, think of ways to make straightforward, repeatable processes that will improve specific activities. For example, lay out the most efficient way to do a shift change and stick to that procedure each time.
- Measure: Ensure processes are efficient using quantifiable data. For example, how long does it take to complete a task using a new process compared to the old one? This is a trackable metric you can use to measure improvement.
- Compare: Compare the data from your measurements with your determined requirements. Does the new process save time while accomplishing the desired end result?
- Innovate: Continuously search for new and improved ways to do the same work and achieve the same result.
- Standardize (again): Once everyone is satisfied with a tested new idea or process, make it repeatable and easily followed by everyone.
- Repeat: Start the approach over again.
This approach to kaizen eventually becomes part of the mindset for the entire organization, making it second nature. Suggestion schemes are a great way to drive kaizen and the idea of continuous improvement. Consider suggestions from the entire team, not dismissing anyone's ideas. Suggestion schemes can be measured by the number of ideas the team submits.
Another way to drive continuous improvement is through the use of quality circles and self-directed teams. These teams consist of people doing work in specific areas and are led by the area's supervisor or team leader. Again, quality circles should be measured by the number of ideas that are suggested. It's important to note that kaizen doesn't need to be bureaucratic. If a team and its supervisor deem an idea worth implementing, they should be able to do so without going through multiple approval processes.
A few suggestions for employing kaizen with your team:
- Have your team keep an idea log of things they notice during their daily routine that seem broken or inefficient and could use improvement. It's easier to notice things as you're performing the action as opposed to sitting in a room and trying to recall them.
- Hold a monthly brainstorming session identifying areas of waste in the processes your team is currently using. Bring the idea log into play here and go through all the types of waste (listed below) to see where waste could be eliminated and how things can be improved.
- Make an actionable plan for how your team will adopt the changes. Find a balance between doing it right now and taking too much time to implement the idea, leading to more waste.
- Think of how proposed changes might affect others within the organization and consult them before putting any changes into practice.
How Kaizen Reduces Waste
The whole idea behind going lean using kaizen revolves around eliminating seven types of waste that hinder efficiency. Let's take a look at what those types of waste are so you will know what to be on the lookout for as you think of ways to improve your processes.

- Overproduction: Considered one of the most serious types of waste, overproduction can cause a domino effect, setting off many other types of waste and resulting in excess inventory. For example, having excess stock leads to multiple types of costs, including storage, wasted material and excessive capital held up in inventory.
- Inventory: Unprocessed inventory includes storage waste, capital lost in unprocessed inventory, the waste of transporting the inventory, storage containers used to hold inventory and other expenses associated with the storage of inventory.
- Motion: The waste of motion refers to all motion – from humans or machines – that could be minimized. Wasted motion can be something as small as an employee searching for a tool to dealing with machinery degradation.
- Defects: Defects are any produced products that do not meet design standards or the customer's expectations. Defective products are wasteful because they must be replaced. This requires more paperwork and labor. The company could also lose customers. Keep in mind that everything put into the defective product – from resources and material to labor – is wasted because the product won't be used. More often than not, defects expose waste in other areas of the organization that may have led to the defect in the first place.
- Overprocessing: Overprocessing refers to any part of the manufacturing process that isn't necessary. For example, this would include adding features on a product that most likely won't be used. In other words, you're adding more value than the customer wants.
- Waiting: The waste of waiting is best described using the example of the assembly line. If one stop on the line takes longer than another, the employees in the next stop are waiting. Any time waste is caused by slowed or halted production in a previous area of the production chain, the waste of waiting occurs. In the case of kaizen, thinking of ways to improve the efficiency of the area causing the delay should be a priority.
- Transport: Moving material from one position to another is considered the waste of transport, since the act of transporting itself doesn't add value to the product. Minimizing transport might mean having the facilities involved in the production processes close to each other or finding ways to minimize transportation costs using more efficient methods. Transport leads to other types of waste, including resources and time used to handle material, employing staff or a third-party to transport material, and having to train employees.
Pros and Cons of Kaizen
When implemented properly, kaizen can have positive and nearly instantaneous effects on your organization's efficiency, leading to an improved end result. In addition to eliminating waste, kaizen has a variety of positive effects centered around improvement, as well as a few limitations.
Pros of Kaizen
- Strengthening teamwork: Teamwork is essential in pulling off a kaizen event. Solving problems together as a team strengthens bonds among employees and gives them a fresh perspective and a sense of belonging as everyone's ideas are considered and worked out. Cross-functional collaborations are another big part of working through a kaizen event. Many kaizen teams include members of multiple departments because most processes flow into one another. Collaborating with other departments strengthens the bond of the entire organization.
- Improved leadership skills: All kaizen teams have a team leader responsible for the organization, coordination and implementation of a kaizen event. Part of the kaizen team leader's job is to ensure that all team members are performing their roles and progress is being made. Contrary to many people's beliefs about a kaizen team leader, the role doesn't have to be occupied by a manager. Enthusiastic employees with ideas to discuss can make great kaizen team leaders. Therefore, present them with a chance to take on a leadership role.
- Improved efficiency: Constantly looking for ways to cut waste out of current processes or procedures ensures efficiency across all departments. Improved efficiency might be as small as finding ways to reduce employee motion on an assembly line or as significant as eliminating unnecessary procedures from a work order process.
- Improved best practices: The previously mentioned standard work document – the current best practices guiding a business – is generally the basis for where a kaizen team will start looking for improvement. It's also considered a living document in the eyes of kaizen – constantly being looked at, dissected and improved. Continuously improving an organization's best practices is important because they are used to train new employees and measure current employees' performance.
- Improved employee satisfaction: An often undervalued advantage to kaizen, employee satisfaction can greatly affect things like productivity, quality of work and retention rates. When you listen to and value employees' ideas for improvement, especially if it's their area of expertise, their sense of satisfaction and worth increases. When they are able to contribute their creative input to the act of improving processes that directly affect them, personnel are more likely to take ownership of process improvements and become advocates for future quality improvements.
- Improved safety: Improved safety is essentially an automatic advantage when it comes to implementing kaizen. Just by eliminating multiple types of waste (motion, transportation, etc.), you reduce the chances for accidents in the workplace. Using kaizen tools like the 5-S system ensures workspaces are clean and orderly, minimizing the risk for accidents. Improved safety also has a positive effect on productivity. When employees don't have to worry about safety, they can focus their attention on their job.
- Reduced waste: Although how kaizen reduces waste and the advantages that brings to an organization has already been discussed, it's worth mentioning again. Reducing the seven types of waste is perhaps the biggest advantage of implementing kaizen due to the far-reaching effects waste reduction has on an organization.
Pros and Cons of Kaizen | |
---|---|
Pros | Cons |
Strengthening teamwork | Implementing company-wide change is hard |
Improved leadership skills | Additional training |
Improved efficiency | |
Improved best practices | |
Improved employee satisfaction | |
Improved safety | |
Waste reduction |
Cons of Kaizen
-
Change is hard: Implementing kaizen into an existing system means changing the existing system. Most organizations don't welcome open communication across all levels of employees. That is to say, they stand by the "This is the way it's always been done, and this is the way it is" way of thinking. Additionally, employees may fear that if they constantly bring up issues to management, it may be viewed as a negative, hurting their chances for a promotion in the future.
For kaizen to work, organizations must get on board with open communication and the willingness to change. This includes current employees. Sometimes it's challenging for long-time employees to adopt changes in the way they've been doing things for years.
Finally, it's always tempting to fall back into the old way of doing things, especially if certain changes are difficult to put into practice. This often occurs when the changes take a little longer to produce results.
- Additional training: Adopting the kaizen philosophy and methodology requires training employees and management on how to accomplish a kaizen event. This most likely will interrupt normal workflow while employees attend training.
Bottom Line
Kaizen can significantly improve your organization's standard procedures, workflows and processes, making the entire company more streamlined and efficient. Outside of workflow changes, it can produce noticeable changes in your company culture and employee engagement. If everyone within the organization is fully committed to making changes from top to bottom and adopts a mindset of continuous improvement, kaizen can transform how your business operates.
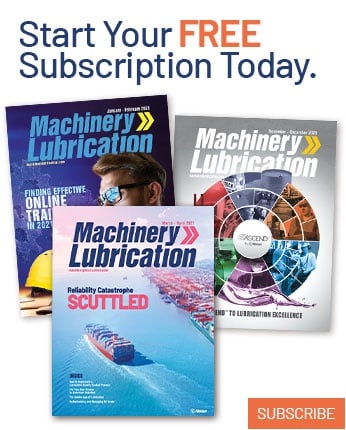