DMAIC is one of two methods used to implement Six Sigma. It stands for define, measure, analyze, improve and control. Below, we'll talk about how to implement DMAIC, the five phases and more.
What Is DMAIC?
DMAIC (pronounced də-MAY-ick) is an acronym for define, measure, analyze, improve and control. This data-driven improvement process is intended to detect and eliminate inefficiencies that result in defects. Though not exclusive to Six Sigma, it's one of two methodologies used to implement Six Sigma, which is designed to improve existing processes and projects.
Before using DMAIC, it's important to evaluate whether it's the right tool for your situation. DMAIC can't be employed in certain circumstances or scenarios, such as to design or create new processes. Its main focus should be on improving existing processes and projects. There are a few specific conditions to consider when deciding if DMAIC is a good fit, including the following:
- There's a glaring problem with an existing process or set of processes.
- You see there's a good chance to reduce things like defects and lead times while saving on cost and improving productivity.
- The process is quantifiable; the data can be measured, and the accumulation of data can be analyzed.
Once you've determined that DMAIC can potentially have a significant impact on your current processes, you can dive into the five steps of implementation: define, measure, analyze, improve and control.
The 5 Phases of DMAIC
The 5 Phases of DMAIC | ||
---|---|---|
Phase | Description | |
Define | Define the problem(s), customers and processes that involve the problem. | |
Measure | Establish a baseline for improvements by collecting data from the process in question. | |
Analyze | Find the root cause of the problems through analysis of the collected data. | |
Improve | Develop, test and implement solutions to improve the process. | |
Control | Develop and implement process controls to sustain improvements. |
Define
The define phase of DMAIC starts with a question: "What problem would you like to fix?" To answer this question, the team should put together a project charter, an all-encompassing living document that outlines a problem statement, a goal statement and a timeline. Your team uses the project charter to clarify things like issues being investigated, why you're examining them and what a successful outcome should look like.
-
Developing a problem statement: Your problem statement should include an identifiable measure, such as lead time and quality of the product. Lead time refers to the amount of time it takes from the customer making a request to the delivery of the product. Quality can mean a variety of things but generally refers to defects.
The problem statement should also address the severity of the issues. Ask yourself, "how big is the problem?" For example, this might be the number of defects per cycle or the number of late orders per month. If severity data isn't available during the define phase, your team can fill in the information during the measure phase. The define phase isn't meant to define the solution but rather focus on:
- What is the problem?
- Where is it having an effect?
- When has it been occurring (short or long term)?
- What is the extent of the problem?
An example problem statement might look like this: Over the last six months (when), 15 percent of produced products are defected (magnitude), up from 9 percent compared to the previous six months. This translates to a 6 percent decrease in productivity (consequence).
- Developing a goal statement: Your goal statement needs to reflect your problem statement. For example, if 8 percent of your products have defects, your goal might be to reduce that by half (4 percent). The goal statement defines exactly the point at which your team and the project will be considered successful. Once the root causes are identified, the statement can be adjusted during the analyze phase.
-
Develop a process map: One of the most popular tools to give your team an overall look at current processes is called a suppliers, inputs, process, outputs and customers (SIPOC) chart. The idea behind the SIPOC chart is that every process begins with a supplier who gives input to the process, resulting in output that is delivered to customers.
Another popular process map is a value stream map. This map shows the flow of steps within a process and any other information required to ensure a product or service is delivered to a customer.
Measure
The measure phase of DMAIC shows you how your current process is performing, which highlights the magnitude of the problem(s). It's all about gathering your data for analysis. Before we discuss the measure phase processes, let's go over some key definitions.
- Unit refers to a single item of the product.
- Defect is an issue with the product that came about due to an issue with the process.
- Opportunity refers to areas in the process where there is a possibility of a defect occurring.
Now that you understand these terms, let's see how they fit into the type of data we're going to collect and measure: defects per unit (DPU), defects per opportunity (DPO) and proportion defective (p).
-
Develop a data-collection plan: Standardize your data-collection processes to provide accurate results and better data. It might be tempting to use historical data, but that data likely would not have been collected using the same structures as your collection process developed here, de-standardizing the data. There are five steps to forming a data-collection plan:
- Clearly spell out the goals and objectives of the data you're collecting.
- Reach a mutual understanding of the definitions and data-collection methodology.
- Ensure data collection and measurement are repeatable, accurate, stable and reproducible.
- Follow through with the data-collection process.
- Follow through with the results.
Step three is important because it validates the measurement system; testing the measurement methodology is key before putting it into practice. Test for four things before launching into your data-gathering project:
- Repeatability: This refers to reaching the same outcome multiple times using the same equipment.
- Reproducibility: Factor in multiple operators, measuring the same items on the same equipment with the same outcomes, and it becomes reproducible.
- Accuracy: Accuracy can be determined by looking at the difference between the average measurement and the associated standard value.
- Stability: Stability is basically an extension of repeatability and reproducibility; what extent does the same operator get the same outcomes using the same machine over a long period of time.
- Data Collection: It's now time to collect your data. Be sure to continue with the validated data-collection process you've established.
Analyze
The analyze phase of DMAIC answers the question: "What's causing the problem?" This is where your team gets to the true caus(es) of the issues by doing a root cause analysis. The idea behind the analyze phase is not to implement solutions but to resolve problems. You do this by brainstorming potential root causes, developing a hypothesis as to why the issues exist and then working to substantiate the hypotheses. Teams should look at process and data analysis before coming up with solutions. Process analysis includes:
- Time analysis. This form of analysis focuses on the actual amount of time that work is being done during a process compared with the time spent waiting.
- Value-added analysis. This type of analysis looks at your processes through the customers' point of view. In other words, ask yourself what is important to the customer and enhance those attributes.
- Value stream mapping. Here, process data is combined with steps in a process that add value to help highlight where waste can be eliminated.
Graphically display data: Visually displaying collected data in charts can transform numbers into visuals, allowing the team to easily see and communicate findings to each other as well as to leadership for analysis. Popular graphs include run charts, histograms, Pareto charts and box plots.
Identify the root cause of the problem: One of the best tools available for process analysis, data analysis and root cause analysis is the fishbone diagram. It uses six categories to brainstorm causes of a certain issue: manpower, method, machines, measurement and Mother Nature. This tool is used together with the Five Whys technique, another brainstorming tool where you ask "why" at least five times. For example, why did machine "A" stop working? Because the circuit overloaded, causing a fuse to blow. Why was the circuit overloaded? Because the bearings locked up due to insufficient lubrication. And so on.
Update the project charter: Once you've determined the root cause(es) of the problems in question, you can update your project charter with any new information. Once the analysis phase is complete, many teams swap out team members because they may find the root cause stems from another department that doesn't have representation on the team. It's important to have the correct team members before moving onto the improve phase.
Improve
At this point, all your hard work has paid off; you finally know what's causing the problem(s) in your current process. Now, it's time to come up with a solution to the problem. The improve phase of DMAIC is where your team once again puts their heads together and brainstorms possible ways to mitigate these newly discovered root causes to the problem at hand. The goal of the improve phase is to identify solutions, test process changes, implement the solutions, and finally collect and analyze data to ensure the changes show measurable improvement.
Remember when we updated our project charter and made sure we had the right team members on the team after the analyze phase? This is where that becomes important. It's essential to have team members whose departments will directly be affected by these impending solutions. There are five techniques the team can use to come up with solutions:

-
Brainwriting. Brainwriting is a modified form of brainstorming and is a technique geared toward generating a lot of ideas in a short period of time. There are two types of brainwriting: 6-3-5 brainwriting and constrained brainwriting.
6-3-5 brainwriting works like this: six people write three ideas in five minutes on a pre-determined topic. Then, the group looks at and decides on the most effective option(s).
Constrained brainwriting revolves around the idea that on certain occasions, the team might want a group of constrained ideas based on a pre-determined focus, as opposed to a free-for-all barrage of ideas.
- Benchmarking. Benchmarking is a technique in which you're always looking for the best methods, practices and processes, and then adopting or adapting to their good features.
-
Assumption busting. Assumption busting is a technique that looks at a situation or possible solution and identifies the assumptions you're making about it. In other words, what seems so obvious that you wouldn't really think about challenging it? When you challenge what you think you know, new perspectives tend to appear.
For example, a possible solution to the problem of products not getting out on time might be eliminating one of three quality-control (QC) checkpoints during a process. The assumption might be that you can't afford to do that in case an inferior product slips through. A possible assumption buster would be to train the other QC inspectors to check for what a third was examining.
- Creative brainstorming: One type of creative brainstorming is called nominal group technique. This technique is meant to narrow down and prioritize a list of ideas. The word "nominal" is used because the team doesn't engage with each other during the brainstorming session, making it an effective tool for when issues are highly controversial, the team can't reach an agreement or there are a lot of new team members in the group.
-
Modified brainstorming. Modified brainstorming uses three techniques to amend the regular creative brainstorming process: the analogy technique, the channeling technique and the anti-solution technique.
The analogy technique asks teams to generate ideas based on an analogy and then translate that idea into a real, relevant situation. The channeling technique requires teams to categorize their ideas into "channels" or categories. Over a period of time, as the team brainstorms, they can "change channels" when new ideas start to lose steam. The goal is to capture a range of ideas (multiple channels) with as many ideas as possible in each channel.
Lastly, the anti-solution technique has the team brainstorm ideas for the opposite of the problem at hand. For example, rather than come up with ideas on how to get a completed work order form, the team brainstorms ideas on how to make sure work order forms won't get completed. Seeing things differently often enhances the team's view of the actual solution.
Control
The problem is fixed, a solution is in place and improvements are being tracked. Now it's time to sustain the solution to where the new process maintains the positive changes. The control phase of DMAIC is where your team creates a monitoring plan to measure improvements of the new process(es) and a response plan in case there is ever a dip in performance.
- Document the new process. During the control phase, your team should document the new and improved processes. This includes updating process maps, checklists with new procedures and other standardized documentation. The more digestible and easier to understand the documentation is, the easier it is for everyone to adopt the new way of doing things. The most powerful way to do this is by making the workplace visible. This is done by using things like the 5-S system to ensure each workspace is orderly and clean, and by labeling each workspace with important instructions.
- Celebrate success. Celebrating the success of a DMAIC process is not only important for team morale, but it also increases the momentum for change within the entire organization. Publicizing each success helps the company realize the possibility of future gains.
DMAIC vs. DMADV: What's the Difference?
If you recall, we mentioned DMAIC as one of the two methodologies for implementing Six Sigma. The second methodology is known as DMADV: define, measure, analyze, design and verify. Both methods are designed to improve efficiencies in a process and make them more effective; however, DMADV is meant to be employed when developing new processes as opposed to fixing existing ones.
To further understand the two, let's break down the similarities and differences between DMAIC and DMADV. Both DMAIC and DMADV use structured methods to solve problems, reduce variation in a process and make the process more efficient. They both collect and analyze data that guide decision-making; utilize teams who work together to solve problems; focus on the customer; and use many of the same tools (charts, graphs, brainstorming, etc.).
There are some important differences between DMAIC and DMADV. As previously mentioned, DMAIC looks to correct a current process, while DMADV is implemented into the design phase. DMAIC takes a reactive approach by reducing or eliminating defects; DMADV is proactive by preventing defects in the first place. DMAIC works by implementing very specific solutions; DMADV is part of the solution from the beginning. Finally, DMAIC implements controls to sustain improvements; DMADV seeks to verify and validate the finished design before implementation.
Implementing DMAIC: A Case Study
One of the best examples for how implementing DMAIC and Six Sigma can impact business performance is that of Continental Mabor, a tire manufacturing company in Famalicao, Portugal. A study done by professor F.J.G. Silva from the school of engineering at Polytechnic of Porto in Portugal examined how Continental Mabor improved the rubber extrusion process of both the tread and sidewall, reducing wasted material in the process. The study analyzed how the company used the DMAIC process to accomplish its goals.
Continental Mabor was seeking to improve the rubber extrusion process, specifically in the mixing, preparation and construction departments. The process works like this: The mixing team obtains the raw materials and transforms them into compounded sheets. The preparation team uses these sheets on seven extrusion lines, which all focus on the tread and sidewall of the tire. In this case, the construction team is the "customer" in the DMAIC process.
During the design phase, Continental Mabor put together a project charter to identify problems and review the scope of all teams and employees involved. They used a SIPOC diagram to lay out the extrusion process in detail. This highlighted the role each department plays to deliver the end products to the "customer."
For the measure phase, the DMAIC team put together a data-collection plan that included measuring the quantity of rejected material during the extrusion process. To ensure they were getting an accurate sample, they collected data for 30 weeks, conducting 10 three-hour trials every week. Once the measure phase was complete, they were able to determine the percentage of unused work based on material generated during the extrusion process.
Next, the focus turned to analyzing the 30 weeks' worth of data to search for the root cause of variation in the amount of wasted material. Using a fishbone diagram, the DMAIC team looked into the cause-and-effect relationship of inputs and outputs to see where unused material was being generated. Each potential cause was prioritized using a Pareto chart, so they could have a visual of which potential cause had the biggest negative impact. The analysis phase resulted in the discovery that one extrusion machine was not performing as well as the others, which led to a significant amount of excess material. Furthermore, they discovered the tread extrusion process had a faulty method of feeding the machines, which created stoppages.
During the improve phase, Continental Mabor implemented changes to the way employees fed the machines, as well as changes to the machinery itself.
Finally, with the changes in place, it was time to implement the control phase. The company collected data on how the improved processes were working. They found the amount of work from raw material was reduced by 5 tons per day. The improvements also had an impact on the bottom line of nearly $182,000 per year after factoring in the cost of the machinery improvements.
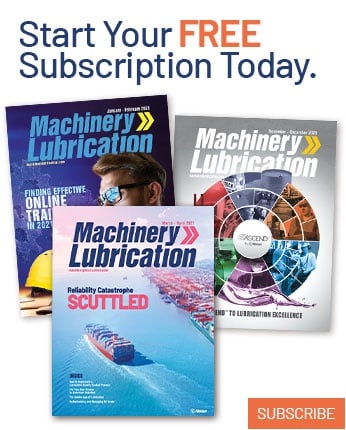