Autonomous maintenance increases efficiency by training operators to perform minor maintenance tasks. Below, we discuss implementing autonomous maintenance, sustaining it and more.
What Is Autonomous Maintenance?
Autonomous maintenance is defined as a maintenance strategy where machine operators continuously monitor their equipment, make adjustments and perform minor maintenance tasks on their machines. This is done rather than assigning a dedicated maintenance technician to perform maintenance and regularly scheduled upkeep.
Autonomous maintenance is the first pillar in the total productive maintenance strategy. An operator trained in autonomous maintenance means he or she has complete knowledge of routine tasks like cleaning, lubricating and inspecting. It requires operators to take ownership of their equipment and its surrounding area. This begins by getting the machine to a "like new" standard of clean and keeping it there, ensuring operators are trained on the proper technical skills for conducting routine inspections, and standardizing an autonomous inspection schedule.
Autonomous maintenance follows two core principles:
- To prevent equipment deterioration through proper operation, and;
- Bringing equipment to, and keeping it at, "like new" status through restoration and proper management.
Much of this relies on operators knowing when a machine upgrade is necessary or when a simple fix can get the machine running again quickly. Autonomous maintenance requires operators to master skills like detecting abnormalities by understanding the machine's components, making improvements, identifying possible quality issues and determining their causes.
With the ultimate goal of total productive maintenance being to enhance your organization's overall equipment effectiveness, there's a reason this starts with autonomous maintenance. It relieves skilled maintenance staff of having to worry about the simple, mundane maintenance tasks, so they can focus on specialized maintenance projects. This leads to multiple advantages like:
- Increasing operator knowledge of their equipment
- Keeping equipment in a "like new" state, ensuring they are clean and lubricated
- The ability to notice emerging issues before they become failures
By allowing machine operators to tackle these routine maintenance inspections and tasks, OEE is further maximized through the reduction of breakdowns and equipment deterioration.
How to Implement Autonomous Maintenance
Implementing autonomous maintenance may vary slightly depending on each plant's operation, but it's typically broken down into seven steps.
- Increase operator knowledge. Operators might be the master of running their machine to maximum capacity, but for autonomous maintenance to be effective, they need to know the ins and outs of their machine. This involves training from maintenance technicians on the technical details of how the machine's components work and their purpose, as well as training on problem-solving skills. In short, operators should have four equipment-related skills:
- Detecting abnormalities
- Correcting and restoring abnormalities
- Setting optimum equipment conditions
- Maintaining these optimum equipment conditions
Once these skills are reviewed in a classroom setting, operators can perform basic maintenance tasks on their machines while maintenance technicians observe to ensure everything is covered.
- Initial machine cleaning and inspection. This step is where equipment is returned to a "baseline" state with the goal of getting it back to a "like new" condition. All hands are on deck for this task, including members of production, maintenance, engineering and operators. Not only is the equipment thoroughly overhauled and cleaned, but the surrounding area is cleaned as well. The goal is to fully restore each piece of equipment to its full performance by identifying and eliminating signs of deterioration. Teams should look for and correct things like:
- Leaks
- Loose bolts
- Proper lubrication
- Cracks – both apparent and non-apparent
- Fluid contamination rates
- Removal of material from water and oil
- Removal of dust and dirt
- Conductibility restriction in electrical manufacturing due to oil and/or dust deposits
- Elimination of stoppages due to dust accumulation
It's a good idea to document the protocol while conducting this thorough cleaning so issues can be easily traced and operators have something to access that contains easy-to-follow steps.
- Remove the cause of contamination and improve access. Now that the initial cleaning is done and all equipment is restored, make sure it doesn't get to a poor state again. This can be achieved by eliminating all possible sources of contamination and improving accessibility for cleaning and maintenance.
This step also takes safety into consideration. Maintaining a running machine is dangerous, so improving the safety and visibility through better access points is paramount. A popular way to do this is by replacing opaque covers with transparent ones for quick and easy visualization of running parts. Removing the cause of contamination can be done by:
- Establishing and sticking to cleaning standards.
- Avoiding soiling. Quality sealing and machine covers are good places to start, but some contamination may only be contained by investing in things like pumps or dedusting – either pneumatically or by dry screening.
- Promoting cleanliness. Continually reiterate cleanliness during inspections and maintenance.
- Promoting orderliness. Making sure tools have their place and remain there increases efficiency.
- Develop standards for lubrication and inspection. This step can be adjusted as needed based on each piece of equipment and its operator. Establishing standards for operators on cleaning, inspecting and lubricating should start with the current documentation on file and end with improved ways to accomplish these procedures. Standards should indicate which components should be cleaned and lubricated, how they should be cleaned and lubricated, and all other maintenance responsibilities to be assigned. Standards will vary based on whether the machine is considered non-critical or critical.
- For non-critical machines, operators are trained by an experienced maintenance engineer to follow the established standards. Operators can then establish their own routine.
- For critical machines, a team of maintenance engineers dedicated to maintenance methods can be created to develop standards.
Once finalized, all standards should be documented and made readily available to operators.
- Inspection and monitoring. Now that they have a set of standards to follow, operators can modify their basic maintenance routine to streamline and improve tasks. The operator's maintenance tasks are tracked and compared with the maintenance department's own schedules (usually through a computerized maintenance management system) to ensure the duplication of tasks isn't an issue. Operators conduct the basic, often-overlooked maintenance tasks such as checking lubrication levels, locating leaks, tightening bolts, looking for impending mechanical issues like cracks and wear, and performing mechanical adjustments like tension measurements, sensor regulation, etc.
- Standardize visual maintenance. Standardizing autonomous maintenance and making equipment "visual" is an important step for maintaining the integrity of each piece of machinery. How do you make equipment visual? Examples include identifying the flow of fluids through pipes, replacing opaque coverings with transparent ones where possible, labeling the open/close direction of valves and levers, and marking "safe" or "normal" operating values on gauges and sight glasses in green with dangerous levels in red. In short, make things on the machine as obvious as possible.
- Continuous improvement. Periodically taking the time to step back and dissect standardized processes to see where there is room for improvement is important to ensure you're operating efficiently. Keeping good records of failures is vital to provide data that maintenance engineers can use when designing future machines, making them even easier to access and maintain.
Continuous improvement can also stem from team leaders and maintenance technicians regularly auditing operators' work. Not only does this allow them to point out areas of improvement, but it gives them a chance to congratulate operators on doing a good job.

Sustaining Autonomous Maintenance
Once your operators are properly trained on autonomous maintenance, the procedures are standardized and an auditing system is in place, it's time to focus on sustaining this process. There are a couple of simple tools you can incorporate into your daily routine to help sustain the autonomous maintenance process.
A daily stand-up meeting is a great way for operators and their direct managers to huddle up each morning to discuss how things are going. These meetings work by going around the circle and allowing each person to discuss what is working well and mention any issues they've encountered. Other agenda items include lessons learned, manpower status, management updates, and the day's targets and actions. Daily stand-up meetings might highlight struggles operators are dealing with or introduce changes from upper management that need to be incorporated.
Single-point lessons are excellent for assisting team members to implement changes, helping them not to overlook a step they are struggling to remember or communicate problems that have occurred in the past to prevent them from recurring. One-point lessons generally are focused on equipment subsystems, safety points and basic operating information. An example of a one-point lesson would be creating a stick-on label to be placed directly on a lever or guard to remind an operator who is struggling to remember to rotate the lever or a guard back into the safety position before continuing to the next procedure.
Other steps to sustain autonomous maintenance include:
- Track failure and breakdown data: This data is essential when you begin forming your autonomous maintenance procedures. Not only does it guide your operators on which equipment needs the most attention, but keeping track of this data over time lets you track improvement.
- Use metrics: Established metrics are the key to monitoring and tracking overall equipment effectiveness in regard to repairs and performance. Analyzing patterns of things like mean time between failures and mean time to repair helps you learn to predict and even prevent future failures.
- Document component wear: Use other means to keep track of component wear. Maintenance technologies like oil analysis, vibration analysis and infrared thermography can give you additional insight into equipment failures.
- Standardize work order creation: Using work order software helps automate and keep track of work order creation and maintenance data. Software that is integrated with a computerized maintenance management system (CMMS) lets you create a maintenance log sheet for each piece of equipment in your plant. Here, you can record every instance of failure, replacements and when the condition of the components changes.
Benefits of Autonomous Maintenance
Most organizations invest heavily in hiring, training and developing a highly skilled maintenance team to determine why critical assets fail and then repair them. Autonomous maintenance seeks to free up these technicians from performing low-skill tasks like inspections, lubrication and minor adjustments. Among others, there are three major benefits autonomous maintenance brings to an organization.
The biggest benefit is lower labor costs. This includes decreasing inefficiencies related to travel time and waiting for availability. By having an operator who is next to a machine at all times, these types of issues are greatly reduced.
Another benefit of autonomous maintenance is increasing the availability of highly skilled maintenance personnel so they can tend to more critical needs. Employing autonomous maintenance allows even the most tightly staffed maintenance departments to attend to critical issues while not sacrificing routine maintenance.
Finally, autonomous maintenance improves team cohesiveness by eliminating the "we/they" mindset. Traditionally, the operator has an "I use" mindset, while the maintenance technician holds an "I maintain and fix" mindset. Autonomous maintenance shifts this into a more cohesive "we maintain" attitude that fits directly into the pillars of total productive maintenance.
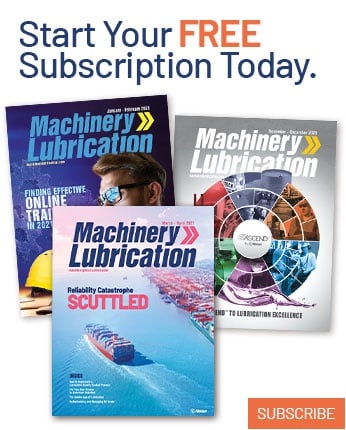