Sealless, self-contained pumps are a staple in the chemical industry. Although these assets typically aren’t large, they are expensive. The three-horsepower pump in this case study costs approximately $7,200 for the rotor and stator assembly. Our plant has many of these pumps, so monitoring them has become an important part of our predictive maintenance (PdM) strategy.
In this case, a call was received to troubleshoot a pump that was “kicking out” on thermal load protection. Initial observations indicated normal process conditions. Valve positions were in the correct locations, pressure was within historical range and the flow transmitter indicated expected flow. Experience has taught us there are other tests we can run to check for proper pump flow conditions. One is the temperature gradient throughout the pump; the other is monitoring run speed through vibration.
Photo 1. Infrared thermography images and vibration data
helped Dow Corning pinpoint pump problems.
This pump style houses process fluid to lubricate the sleeve bearings for obtaining hydraulic stability of the rotor. The infrared image (above) indicates the pump does have flush fluid flow to the rear bearing housing. Evidence of this flow is the cooler colors at the rear bearing housing. Even with the appearance of proper fluid flow, excessive heat buildup was apparent in the stator and rotor assembly (notice the white hot spot).
The next test was to take vibration data.
Graph 1. Initial data indicated fairly normal process conditions.
Graph 2. The vibration plot displays signs of a rotor problem.
The plot (Graph 2) shows the signature indicating the likelihood of a rotor problem. Multiple harmonics of run speed were surrounded by two times slip frequency. This signature can be driven by several faults, including shorted rings, broken/cracked rotor bars and shorted rotor laminations. At this point, we recommended scheduling a pump changeout. The spectrum supports the fact that the pump was running under acceptable flow conditions. The optimum run speed for this pump class is 3,450 RPM.
The rotor has a thick stainless steel covering
2 to 3 mils thick.
A thin stainless steel layer covers the rotor and stator windings; therefore, the efficiency is lower than typical two-pole motors. This pump was running at 3,466 RPM, well within the best efficiency point. We had to wait for the teardown to try to find the specific driver for this vibration signature. A unique and troublesome problem in doing an autopsy on these pumps is the rotor has a thick stainless steel covering 2 to 3 mils thick. Our machine shop had to carefully remove this covering to expose the rotor bars and laminations for inspection.
Removing the covering exposes the
rotor bars and laminations.
The rotor minus the covering clearly indicated the pectral signature cause. The rotor’s right side showed a clean separation between the rotor bars and laminations. The left side illustrated a breech of this separation as well as discoloration most likely caused from heat buildup.
We installed a new rotor in the existing stator and the pump was back to running under normal operating conditions. I am confident that if the pump continued to run this way undetected, we’d have eventually lost the stator. Rotor replacement costs approximately $3,000 of the $7,200 total. A catastrophic stator failure also has a potential for atmospheric release of the process fluid.
In conclusion, this case isn’t a typical failure mode for this pump class. Generally, we track the subsynchronous energy representing oil whirl/whip to assess bearing wear. This is critical for these pumps; the tolerance between the rotor and stator is 5 to 7 mils. Once you have rotor-to-stator contact, the integrity of the pump/motor is compromised and it must be scrapped. A bearing rebuild kit costs $400 as opposed to scrapping a $7,200 pump. This case also illustrates two additional powerful attributes that vibration analysis brings to troubleshooting and tracking equipment issues.
-
Not only can vibration analysis predict impending mechanical failures, it also can rule out hypothetical failures during the troubleshooting discussions.
-
Using vibration analysis on specific assets can indicate changing process conditions that may be the root cause to machine or product quality issues. Vibration analysis can indicate process changes by showing characteristic changes in the pump flow remove word.
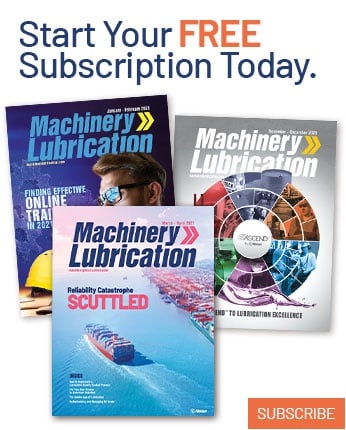