Maintenance manager Robert was up to his elbows in grease and looking for spare parts. On his way to the supply room, he met Ron, the corporate reliability manager.
Robert was in a hurry, but he took time to greet Ron and make small conversation. Robert told Ron that when time allowed, he would like to speak with him about several machine reliability issues.
“Where are you headed in such a hurry?” asked Ron.
“The press is down again and I’m looking for parts”, answered Robert.
Ron responded by asking, “When you get it repaired, will it break again?”
“Of course it will. We have a lot of reliability issues with the press.” said Robert.
Ron responded by saying, “Perhaps you’re working on the wrong thing.”
Robert did a quick double-take and chuckled. He thought Ron was joking. “When the press is down, that’s where I need to be. Would you have me working on something that isn’t broken?” chuckled Robert.
He realized that Ron wasn’t joking when Ron asked, “Is it possible that the press failed because the maintenance process is broken? A good, reliable maintenance process would help to insure that the press remains in reliable operating condition?”
The conversation was beginning to make Robert feel uncomfortable, and he had important work to do. Robert felt that Ron was a nice man, but was now talking some pie-in-the-sky theory. Walking away, Robert said, “Gotta go, Ron, but we’ll talk about the issues that I mentioned, for sure, when we get up and running. Nice seeing you.”
Except for the names, the above conversation is true and demonstrates that most equipment failures are a result of failed reliability processes. This article covers many of the reasons why equipment reliability processes fail. The authors have personally observed all of the reasons for reliability process failure discussed in this article.
Failure Mode: Implementation Failure
It can be rightfully argued that all equipment reliability process failure modes are somehow tied to poor implementation. Not establishing an initial direction is a critical mistake in the implementation process.
Establishing clear goals and expectations and a clear direction can increase the success rate of an equipment reliability process. If upper management fails to communicate the expectations of the program, accountability can never be achieved.
The authors have witnessed millions of dollars being dumped into reliability processes that had no established direction and goals. The Penn State manual Operating Equipment Asset Management identifies some critical elements that should not be overlooked when instituting the equipment reliability process.
Top-down vision, drive, participation, support and clear, ambitious objectives are elements that should not be overlooked on implementation. It’s a good idea to examine this entire publication before implementing an equipment reliability process.
Failure Mode: Not Understanding the Equipment Reliability Process
Sometimes a company will have the best of intentions for implementing an equipment reliability process, but no one in the company may have an understanding of how machine reliability is achieved.
Sometimes a person in the company may have the necessary knowledge, but they are overruled on important issues that could insure success of the equipment reliability process. Knowing how to maintain equipment for the desired reliability requires knowledge that is acquired through training.
If that knowledge isn’t present, no equipment reliability process will bring plant reliability. There are a few good ways to maintain machines and thousands of poor ways, but there is only one best way for any given machine.
It is critical to choose one of the good processes and work toward making it the best equipment reliability process for your plant. In short, it isn’t possible to maintain a machine to required reliability if machine reliability isn’t fully understood.
If managers and plant personnel don’t truly understand the equipment reliability process, they will lack confidence in the process and will be destined to failure. Many equipment reliability processs fail simply because the managers and practitioners don’t have confidence that it can deliver the required results.
Failure Mode: Lack of Accountability
These days, we hear much about empowerment self-direction. This sometimes leads to the idea that everyone can do their own thing as long as they do those things with good intentions.
The authors are strongly in support of empowerment and a self-directed workforce as long as the empowered conform to the directives of the equipment reliability process.
The equipment reliability process is not perfect and will need to be continuously revised and improved, but the basic framework, if correct when chosen, should remain intact. Any modification should be subject to a formal management of change. Everyone in the plant needs to be held accountable for their work.
Corporate managers often fail to keep the equipment reliability process on track by letting small factions steer off course with practices that vary from the equipment reliability process. This is the result of the corporate manager either not understanding the equipment reliability process or not having confidence in the equipment reliability process.
Too often, corporations turn over the management of an equipment reliability process to managers who have had success in non-maintenance areas, but have little or no reliability experience.
Combine the lack of reliability experience with no established goals or direction and you have induced a failure mode right out of the gate. How can people be held accountable when they don’t know what is expected from them?
Failure Mode: Market Conditions Cause a Change in Plans
Too often, companies are willing to invest in various programs when times are good. Sometimes this is even to the point of waste. But when markets go sour, policies are changed in order to conserve dollar assets.
In such times, equipment reliability processs may have funds cut to the point that past gains are lost. The equipment reliability process may not survive a bad market. Companies should develop spending strategies that are stable regardless of market conditions. A wasted dollar can never be recovered.
Some producer will sell products even in down markets. The lowest-cost, highest-quality producers will survive difficult times. A good equipment reliability process is an important factor in enabling a company to be the low-cost, high-quality producer.
Failure Mode: Commitment Falters over Time
When mangers fail in the implementation of the reliability process, it allows other failure modes to begin eroding the program. If the direction and expectations are not initially established, accountability has no teeth.
Without accountability, the commitment from upper management becomes viewed by the people as being more relaxed with each and every sunrise.
Before long, even upper management forgets the initial purpose of the program. As the perceived importance of the equipment reliability process lessens, the commitment is shifted to other programs or issues.
Failure Mode: Failure to Measure Results
You can’t measure what you can’t quantify, and what gets measured gets done. The difference between a well-designed metrics system and a poor one can be detrimental to improvement efforts.
A metric is essentially a clear, quantitative, objective measure to assess performance in a particular area or progress toward a goal. A good computerized maintenance management systems (CMMS) coordinator can pay big dividends when helping establish metrics and deciding how data needs to be measured within the CMMS.
Most systems can generate good, consistent reports if it is set up to do so. However, most of these systems are grossly underutilized, and companies are too dependent on CMMS coordinators to decide what can be measured and what can’t be measured. The metrics should be established by a committee with the equipment reliability process goals in mind.
Six Sigma has been used on the process side in a lot of companies for sometime now. It could be argued that the utilization of black belts and green belts on the maintenance side could be beneficial, and in some companies, they are utilized in that capacity.
But in the author’s experience, that generally was not the case. Managers sometimes concentrate on standard deviation of product moisture content and overlook mean time between failures. Assessment results can’t be consistent without good, solid metrics.
Too many times, the authors have witnessed variations in assessment scores from one facility to the next because of inadequate metrics, peer pressure and managerial perception.
Nothing can compromise the integrity of an assessment process more than the perceived inconsistencies of the assessment team’s scoring procedures.
Failure Mode: Cultural Integration
A company may establish a reliability steering committee, select champions and mentors, even train their entire workforce on cultural change. They may then hire outside people to oversee the equipment reliability process.
Is it really a good idea to hire outside people to fill roles such as plant reliability engineers, planners, schedulers, plant managers and maintenance managers, especially, if these people have little or no reliability experience?
Sometimes the outside people may come from a completely different industry that doesn’t understand the manufacturing process or from the same industry but from a run-to-fail culture. Fosters of equipment reliability processs should guard against infiltration of cultural integration.
If people are brought in from different cultures, they should be in complimentary roles and trained in the company’s culture before taking on major roles in the equipment reliability process. Too often, a little outside influence causes regression back into the run-to-fail maintenance of yesterday.
Failure Mode: Lack of a Strategy for Managing Equipment
Even though condition-based monitoring methods may be established, strategies for managing equipment are still needed. Condition monitoring is a requirement for good machine management, but other strategies also should be incorporated into the equipment reliability process.
Reliability-Centered Maintenance (RCM) and Total Productive Maintenance (TPM) are two good tools that should be considered to help with the management of equipment reliability.
Consider setting up pilot machine centers and conduct RCM or TPM projects. The information learned from these pilot projects can then be transferred to similar machine centers in other facilities.
Failure Mode: Low-Hanging Fruit Syndrome
When these types of programs are initiated, the benefits are quite obvious. Just about everything attempted – from instituting an oil cleanliness program to condition monitoring or failure analysis – reaps big initial benefits and everyone is happy.
But, just as soon as the low-hanging fruit is picked, a program with no direction or structure starts to look more like a dog chasing its tail. Unfortunately, this happens too often in industry.
Someone suggests an equipment reliability process and it seems like a good idea when you look around and see all of the potential for improvement. But, the equipment reliability process is an ever-changing process and every bit of beneficial juice has to be squeezed out of the reliability process.
Both authors agree that all of the potential failure modes of an equipment reliability process seem to point to several key elements, such as commitment to reliability, accountability and sustainability.
We have witnessed some success and eventual regression of equipment reliability processs based on some or all of these failure modes. There are other failure modes, but the ones mentioned here have been witnessed by the authors.
Read more: FMEA Explained: What Is It and How Do You Implement It?
About the authors:
Gary Fore, CMRP, has 22 years in the energy and building products industries, specializing in reliability engineering with a heavy emphasis on condition monitoring. He holds a bachelors of science degree in mechanical engineering and an associates of applied science in electro-mechanical technology. His certifications include: Certified Maintenance and Reliability Professional (Society for Maintenance & Reliability Professionals), Category III vibration analyst (Vibration Institute), CLS (Certified Lubrication Specialist), Level II infrared thermographer, and Machine Lubricant Analyst Level I (International Council for Machinery Lubrication).
Bill Hillman has 30 years experience in the steel industry and six years in the wood products industry. His entire career has been in equipment asset management, of which more than 20 years have been in predictive maintenance. Bill is a Certified Maintenance and Reliability Professional, past chairman on the board of the International Council for Machinery Lubrication, certified by the Society of Tribologists and Lubrication Engineers, and a certified infrared thermographer. He holds or previously held certifications by the Vibration Institute, NDT in ultrasonics, magnetic particle testing, and liquid penetrant testing. He is trained in Reliability-Centered Maintenance and is an experienced RCM facilitator. Bill is also trained in Total Productive Maintenance and 5-S. He is now a managing partner of Asset Management Specialists Company. Bill can be contacted at billcmrp@yahoo.com or 903-407-9488.
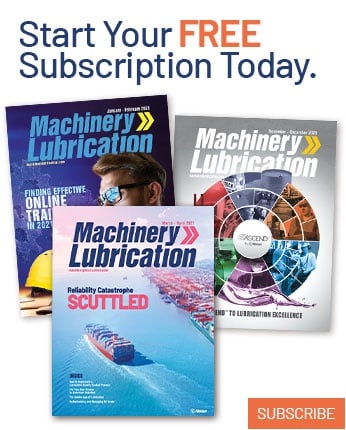