Imagine a business strategy—grounded in proven engineering principles—that any manufacturer could use to maximize output capacity, increase sustainability and generate gains. It exists, and there's never been a better time to implement it.
Tariffs are Today’s Reality
Tariffs are simultaneously introducing a challenge and an opportunity for manufacturers operating in the United States. While the effects will vary, overall short-term demand for products made in the USA is sure to go up, with long-term demand likely to follow suit in the coming years.
To prepare your plant for this opportunity, you must consider whether your factory can meet increased demand at a competitive price point, whether it is capable of scaling up both existing and new product lines, and what investments are needed to improve equipment reliability and optimize factory performance. It is also essential to plan how you will train your workforce to remain competitive against imports and domestic competitors, and most critically, determine who will lead this effort while you remain focused on running the plant.
Tariffs that Directly Affect Manufacturers
There are three types of demand manufacturers need to consider
-
Products Made in the USA
The demand for these products will go up. We need to maximize the capacity of our factories to make more products within our existing product lines. We can do this by maximizing the efficiency and effectiveness of every task our operations, production, maintenance and engineering teams perform -
New Products No Longer Made in the USA
The demand for these products will go up. We need to expand the capabilities of our factories to make new products. This will require new machines, adding space to house them and training for our teams to run them. Making new products will need new intelligence, new knowledge and new thinking. -
Critical/Essential Products No Longer Made in the USA
The demand for these products will go up. This opportunity will likely require building new factories or expanding existing structures.
This is already happening – factories are being constructed and expanded rapidly. The question is are you ready to lead the charge?
Who is Dealing With Tariffs?
The biggest hurdle comes from not knowing who is going to solve the tariff challenge while you are running your plant day in, day out. We need to make more products to replace the ones we used to get shipped from abroad. This will require someone who can obtain resources and knowledge to fill this gap in a timely manner.
Solving the challenges posed by tariffs cannot be accomplished by one person, one department, or by simply introducing scattered digital tools. It also won’t be resolved by speculative technologies or even longstanding government agencies like the National Institute of Standards and Technology (NIST), which have made multiple attempts with – at best – limited success.
So, who will step up to maximize factory output in the face of these complex challenges?
Not CEOs, Investors, and Owners (CEOIO), who need access to operational excellence and reliability training tailored for strategic decision-makers—resources that are currently scarce or fragmented.
Not plant managers and engineers, who despite their best efforts, have hit the ceiling of what traditional tools and methods can achieve.
Not U.S. government initiatives, such as those from NIST and the Manufacturing Extension Partnership (MEP), often rely on decades-old frameworks that struggle to address today’s hyper-complex manufacturing environment.
Not the National Science and Technology Council, which emphasizes advanced manufacturing (semiconductors, microelectronics, etc.) but does not always support the foundational process improvements more typical plants still require.
Not internal or external improvement consultants, who can sometimes offer siloed training or one-size-fits-all solutions that haven’t evolved much over the past 30 years.
Not technology providers—whether in software or hardware—who typically offer highly specialized tools that lack integration with broader factory needs.
Not IT departments, who may be adept at cybersecurity and system maintenance, but still struggle to bridge the gap between IT and OT (Operational Technology) to truly digitize manufacturing processes.
Each of these stakeholders is competent and knowledgeable within their own domain. However, coordinating across these silos—each with different priorities, budgets, and leadership styles—makes deploying and synchronizing a new, holistic method-technology extremely difficult. The result is the kind of stalled-out, fuzzy-chaos* environment that many plants face today.
*Fuzzy-Chaos?
Fuzzy-chaos is a term I use to refer to a situation where people know action is needed but keep deferring it, hoping someone else steps up or it will simply go away. We all saw tariffs coming. How many plants truly prepared?
So the question remains: Who will normalize this fragmentation and lead the charge to truly maximize factory output capacity? Without someone responsible for them, the efforts cannot begin.
How are Tariffs Being Dealt With?
To leverage tariffs, US factories must produce better products and produce them faster. Those products need to have a lower Cost of Goods Sold (COGS) and must be delivered on time. In other words, each factory needs to maximize their output capacity regardless of who will conduct the effort.
The Past
Over the last 35 years, manufacturers have tried to improve the performance of their factories by introducing continuous improvements, technologies and obtaining training/services.
A quick inventory of the tools and initiatives applied over the years can help us understand what worked, what didn’t, and where we stand today. This retrospective also highlights opportunities to leverage new intelligence and thinking through the latest innovations.
Most factories have relied on a combination of three major tools—each with its own set of challenges.
1. Continuous Improvements Until Stagnation
Programs like TPM, Lean, Six Sigma, Lean Six Sigma, Theory of Constraints, and internally developed methods have been widely used. While these approaches can bring early success, they are notoriously difficult to sustain long term. A key reason is that return on investment (ROI) is rarely monitored, making it difficult for executive leadership (CEOs, COOs, etc.) to commit to future investments with confidence. If they don't clearly see what they'll gain, their appetite for continued funding inevitably wanes.
2. Aging Technologies Deployed Without Integration
Factories have gradually implemented decades-old technologies in the hope that persistence will eventually pay off. On the hardware side, this includes motors, drives, gearboxes, pumps, injection molding machines, CNCs, sensors, PdM tools, and various process instrumentation. These technologies often come from a wide range of OEMs, resulting in inventory and troubleshooting chaos. Though newer models may offer flashy user interfaces, they frequently lack any added intelligence or interconnectivity. Without integration, valuable insights are lost.
Software technologies are also commonly used—ranging from Excel to industrial systems like MES, ERP, CMMS (IT side), and PLCs, HMIs, SCADA (OT side). More modern concepts such as Digital Transformation, Industry 4.0/5.0, and AI are emerging but remain in early or siloed phases. Connectivity is complex, flexibility is limited, and vendors often expect upfront investments without being able to guarantee results. This raises skepticism, particularly when data quality cannot generate intelligence and ROI uncertain.
3. Sporadic Training and One-Off Services
Training, though essential, has historically been one of the most neglected tools. Sources like universities tend to be overly theoretical, while OEMs focus narrowly on their own products. Service providers and subject matter experts typically offer fragmented, niche-focused content. On-the-job training, while common, is expensive due to trial-and-error learning. In-house programs are rare and usually lack structure or sustainability—despite being the area of greatest opportunity.
There’s a broader issue too: very few organizations truly understand or support the long-term value of structured training. Moreover, there's little to no training aimed at executive decision-makers, who must learn how to invest wisely in improvements, technologies, and services. Without this strategic education, investment decisions remain minimal and misaligned, resulting in negligible ROI. Meanwhile, even service providers with proven tools often can't deliver improvements at the speed today’s market challenges, such as tariffs, demand.
In addition to the individual limitations of these three approaches, the largest obstacle is how siloed-off their implementations often are. These disconnected efforts can’t be synchronized to create intelligent processes or a unified operational vision. For frontline workers and the CEOIO, this disconnect makes it hard to see how breaking down these silos may actually improve factory performance. After all, if you’ve been trained and operated as a hammer your whole career, it’s hard not to see the factory’s challenges as nails.
Unless tools are integrated and synchronized across systems, even the best technologies and practices will fall short—especially when it comes to handling disruptive pressures like tariffs.
The Present
With a clearer understanding of past challenges, we can now look to today’s resources to create a plan that truly maximizes factory output capacity.
What do we have today that we didn’t have in the past? A lot.
- We now have access to modern methodologies, technologies, intelligence, and accumulated knowledge that can solve challenges once considered unsolvable.
- We can detect and resolve systemic stresses before they become entrenched in departmental silos.
- We can finally visualize and digitize the factory as an interconnected system—engineered to fulfill business objectives and generate measurable output and revenue.
- We can achieve the objectives above quickly.
This strategic, system-wide view is what executives—especially CEOs, investors, and owners (CEOIO)—have needed to truly engage with operational improvement efforts.
By adopting this broader perspective, we can finally begin recognizing and addressing stresses that limit our current output, such as:
- Machinery Breakdowns
- Overlapping Improvements
- Fuzzy Chaos* Attitude
- Disjointed Solutions
- Business Engineering Strategy
Understanding these elements can help us pinpoint where to intervene. For example, the presence of gaps in our strategies (or a complete absence of unified strategies) allows short-term fixes to override more sustainable solutions.
The Future
Some are waiting for AI and robotics to rescue US manufacturing. While this will come to fruition someday soon, at this moment it is not a reality for most industries. What we can do today is to prepare for the factory of the future by creating a system that will take full advantage of robotics and AI when those technologies become more ubiquitous. We can start today by gathering intelligence and doing our best to turn every action into revenues, profits and increased market share opportunities.
The least we can do is to begin developing a system that moves away from reactive management. I am hoping we can put an end to this management style and resulting culture.
Conclusions
Tariffs are not just a challenge—they’re an open invitation to reinvent how we operate. Learn from your past, inventory your present, and design a future you can scale with confidence.
Your strategy must align people, technology, and process. You don’t need a miracle—you need a system that gets your operations, maintenance, engineering, and production teams pulling in the same direction: forward.
Move fast. Demonstrate ROI. Secure CEOIO support. The factories that win will be the first to optimize their systems to take advantage of the opportunities presented by tariffs.
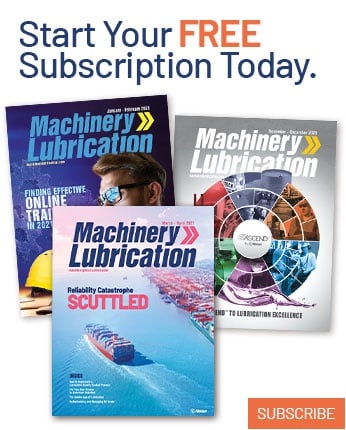