Manufacturing is a highly demanding industry that relies on the hard work of skilled and dedicated professionals who have their own needs and expectations for working comfortably and efficiently. Accurately addressing these needs and expectations as management can greatly improve job satisfaction, workforce engagement and employee retention — key ingredients for boosting your shop-floor productivity.
In this article, we’ll explore four keys that management should adopt to help empower their manufacturing workforce and create the ideal work environment.
Key No. 1: A safe work environment is important.
Although workplace safety must be a priority in any business, it’s even more important in manufacturing because of the potentially hazardous chemicals and machinery that are commonly used in the production process. Keeping your workers safe comes with added benefits like reducing workplace injuries, preserving your company’s reputation and saving money from the direct and indirect costs associated with occupational accidents.
For your workers, attention to safety makes a difference. Safety helps build a positive work environment, which is vital in maintaining your workforce’s mental health.
Some technologies that can help improve safety on the manufacturing floor include:
-
IoT sensors: IoT sensors can collect a worker’s health data (such as heart rate, oxygen levels, etc.) to monitor them while on duty. They can be used to detect falls, temperature variations, toxic fumes or other changes in air quality. They can even automatically shut down machinery if there is excessive heat or the worker is too close. IoT sensors can also send up-to-date information to cloud-based dashboards that plant managers can access in real-time, alerting them about dangerous situations and helping them mitigate risks.
-
Wearable devices: IoT sensors and other types of monitoring technology are usually integrated into wearables, such as smart helmets or smart vests. Smartwatches, on the other hand, can allow workers to access real-time information when making data-driven decisions, responding to notifications or receiving alerts that keep them aware of hazards or potential accidents.
-
Automation and collaborative robots: Automation is intended to replace repetitive and time-consuming tasks that most workers find monotonous, which, in turn, could allow them to focus on more fulfilling or creative tasks that involve problem-solving or critical thinking. Additionally, automation and collaborative robots can take over difficult or dangerous tasks, potentially resulting in better standards for workplace safety and overall better job satisfaction.
Source: Blackline Safety
Key No 2: Effective staff logistics are necessary.
Organization in manufacturing is crucial. An effective manufacturing staff scheduling system makes sure your workers are in the right place at the right time and have access to the required materials and equipment.
With the aid of well-functioning manufacturing logistics, workers can feel confident that they have the resources needed to help them accomplish their tasks, and that their time and efforts will be spent effectively. As a result, they can focus on tasks without worrying about disruptions or delays and complete them quickly and efficiently, which could lead to an increase in the shop-floor’s overall productivity.
An optimized workflow reduces cycle time and increases throughput, thereby, enabling faster delivery. Lean methods, like Just-In-Time (JIT), synchronize the production process with demand to reduce inventory costs and waste.
Work optimization also focuses on continuous process improvement to eliminate non-value-adding activities through techniques such as Value-Stream Mapping (VSM), which allows manufacturers to visualize the entire production process, identify bottlenecks and eliminate any unnecessary steps.
When conducting VSM on a particular internal process or workflow, manufacturers will do a close examination of each stage to spot which steps eat up time without adding any real value. Once they’re able to identify and cut these unnecessary steps, the whole process becomes smoother and becomes more focused only on the stages that provide real value.
Lastly, cross-training enables greater flexibility:
-
When an unexpected spike in demand occurs, a cross-trained workforce can be swiftly rearranged to meet that demand without sacrificing efficiency or quality.
- In the event of machine breakdown or maintenance, workers can be reassigned to other areas of the production line, ensuring minimal disruptions to the overall schedule.
Optimized employee scheduling forms an integral part of work optimization and helps to better align workforce deployment with management’s strategic goals.
Key No. 3: Proper training is a must-have.
A lack of knowledge and training in manufacturing can lead to human errors that cause serious accidents, most often involving occupational injuries and loss of productivity.
Source: Limble CMMS
While on-the-job training is irreplaceable in some areas, modern technologies provide other options to impart proper training to your workforce.
For example:
-
Online training: Your workforce learns the basics through online videos, calls and conferences, webinars and digital documents. Additionally, learning management systems (LMS) help organize and deliver online courses and training materials.
-
Virtual reality (VR) devices: VR devices replicate real-life scenarios that workers can encounter on the manufacturing floor and allow them to practice and perform tasks in a simulated environment without the risks or costs associated with real-world training. Workers can use VR to develop their skills and confidence in a safe and controlled setting before they must perform that task in real life.
-
Augmented reality (AR) devices: By showing digital overlays on real-world images, AR devices (such as headsets or smart glasses) provide step-by-step instructions to workers, enabling them to perform tasks (such as repairing a machine) with real-time visual guidance.
-
Connected worker technology: Remote mentoring, training materials and other enterprise resources are instantly accessible — “hands-free”— allowing workers to simultaneously perform tasks and access training materials without having to pause their work or physically manipulate a device.
Key No. 4: Data and analytics are crucial for decision-making.
Workers need access to real-time data to make informed decisions and improve processes. Data and analytics keep them away from guesswork and being counterproductive, which can result in more confident decision-making since they can rely on data to back them up. Additionally, they don’t have to run unnecessary risks: outcomes are positive as long as the provided data is accurate and the analysis is not flawed.
Some of the technology solutions that provide these benefits are:
-
IoT ecosystems: The Internet of Things (IoT) refers to a network of physical objects that share data with each other and in a central hub called the IoT gateway. By gathering and analyzing data from multiple IoT-connected devices, the IoT gateway can provide valuable insights to facilitate informed decision-making.
-
Cloud computing: Cloud computing is replacing traditional data and analytics infrastructure because it is more flexible and cost-effective. The cloud lets you store and process large amounts of data, so if you need more space, you don’t have to buy new hardware. You simply need to add computing resources on a pay-as-you-go basis.
For workers, the cloud is important, as the data is not stored in a piece of hardware but in remote servers, which can be accessed anytime, anywhere and on any device. Cloud computing essentially allows them to make data-driven decisions more easily.
-
Connected worker platforms: Connected worker platforms collect real-time data from sensors and mobile devices. This information is then fed into a cloud-based system that workers can access (after it is processed and analyzed) and use for decision making.
Conclusion: What matters most?
It is your responsibility as management to ensure your workers have the right tools to perform their tasks and duties in a safe and efficient manner. If your shop floor has access to the latest technology, it’ll surely help your workforce do their job more effectively and increase their overall job satisfaction.
In the drive to always get more done, are you also keeping in mind to always try putting the workers — the heart and soul of the manufacturing industry — in the best position to succeed? Are you truly empowering your workforce? If you get into the habit of asking yourself these questions, you’ll be sure you’re doing your part in creating a more worker-friendly and efficient manufacturing industry.
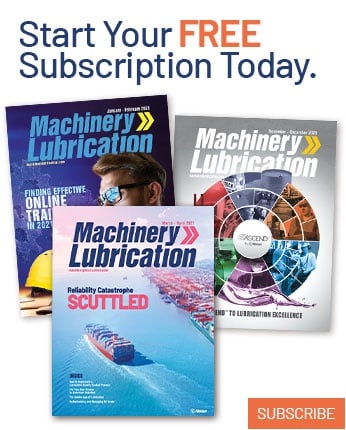