The Role of Leadership
Leadership within industrial manufacturing sets the tone for the entire organization. Effective leaders understand that maintenance and reliability are not just cost centers but strategic assets that contribute to competitiveness, product quality, and overall operational excellence. Leaders who prioritize maintenance and reliability initiatives can shape a culture of continuous improvement and a strong focus on asset care.
Effective leaders can help to drive the effectiveness and efficiency of:
Vision and Strategy: Visionary leaders formulate a clear strategy for maintenance and reliability that aligns with broader organizational objectives. They establish measurable goals, allocate resources appropriately, and champion the importance of proactive asset management.
Resource Allocation: Adequate funding, skilled personnel, and advanced technologies are all critical for successful maintenance and reliability programs. Strong leadership ensures that these resources are allocated efficiently, preventing disruptions and minimizing downtime.
Change Management: As technologies evolve and industry landscapes shift, adaptable leaders drive the adoption of new methodologies and best practices in maintenance and reliability. They encourage a culture that embraces change and innovation.
Adapting to Change: Manufacturing environments are dynamic, with technologies and processes evolving rapidly. Training fosters adaptability, allowing employees to stay up to date with the latest advancements and adjust their strategies accordingly.
Leadership Support: Strong leadership champions training initiatives, ensuring that resources are allocated for continuous skill development. When leaders prioritize training, employees feel valued and motivated to enhance their skills.
Cultural Reinforcement: Effective leaders can help to reinforce a culture of learning and improvement. Organizations that encourage a culture of lifelong learning create an environment in which employees actively seek opportunities to upgrade their skills. It was once said, "What’s worse: we train our employees and they leave, or we don’t train them and they stay".
Cultural Foundations
Organizational culture functions as the invisible framework that shapes behavior, decision-making, and attitudes within an industrial manufacturing setting. An optimal culture promotes collaboration, accountability, and a sense of ownership over the production processes and assets. Leaders who know and understand the importance of reliability — and how critical it is to optimizing production — can help to engrain reliability into the culture, similar to how safety and quality have been integrated over time.
Safety First: A culture of safety underpins successful maintenance and reliability efforts. Leaders who prioritize safety communicate its importance, encourage adherence to best practices, and create an environment where employees feel comfortable reporting potential issues. It has also been studied and proven that companies with high reliability have better safety records.
Collaboration and Communication: Open-communication channels foster collaboration among different departments, inlcuding engineering, operations, and maintenance, and lead to better decision-making and problem-solving. A culture of transparency reduces misunderstandings and finger-pointing.
Continuous Learning: Maintenance and reliability practices are continuously evolving. A culture of learning encourages employees to acquire new skills and knowledge, helping them to stay ahead of emerging technologies and industry trends. Training and investing in your workforce can help close the skills gap that industrial manufacturing companies are facing. Trained employees are also more likely to suggest improvements to existing processes and identify opportunities for cost savings and efficiency gains.
Diagnostic Skills: When companies invest in their employees through training and skills development, maintenance staffs become armed with the ability to diagnose problems accurately, which can help in reducing downtime significantly. Training in diagnostic techniques enables them to identify issues at their root cause, leading to quicker and more precise solutions.

The Synergy: Leadership, Culture, Maintenance, and Reliability
The synergy between leadership and culture significantly impacts maintenance and reliability outcomes. When leadership and culture are aligned, several benefits emerge:
Reduced Downtime: A culture of proactive maintenance and reliability practices, fueled by supportive leadership, minimizes unplanned downtime, leading to increased operational efficiency.
Enhanced Asset Longevity: Strong leadership drives a culture that emphasizes proper asset care, extending the lifespan of equipment and reducing the need for frequent replacements.
Optimized Resource Utilization: Effective leadership ensures that resources are allocated efficiently, along with eliminating wastage and maximizing the return on investment in maintenance and reliability initiatives. Because a company can run more efficiently, leadership can more easily take advantage of emerging technologies associated with Industry 4.0 (as long as the foundational elements and practices of reliability are in place). They can be in a better position to integrate automation and data analytics, as well as Internet of Things (IoT) Training programs that can familiarize employees with these technologies, and empower them to harness the potential of smart manufacturing for improved maintenance and reliability.
Improved Employee Engagement: A positive culture that values employees' contributions and provides opportunities for growth enhances morale and job satisfaction. Engaged employees are more likely to be diligent in maintaining equipment. The modern industrial worker wants to be in place where they can grow, thrive, develop, and contribute to the organization through meaningful work.
Conclusion
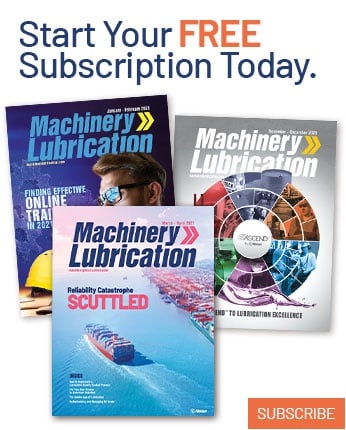