Different manufacturing companies might have different goals - the most crucial ones must work in tandem. Some of these goals are selling more products, reducing manufacturing costs, improving production efficiency, increasing profits, and reducing production disruptions. Out of these, improving efficiency can help achieve the other goals - it cuts unnecessary costs, boosts, throughput, and increase profits as well as productivity. That being said, let’s take a look at 5 tips that can help organizations improve manufacturing efficiency.
Inspecting Current Workflow for Issues
Unsurprisingly, this is one of the first steps organizations must take to improve manufacturing efficiency. It’s quite simple - without evaluating the current workflow utilized in plants and facilities, organizations won’t be able to detect room for improvement. They must inspect every aspect of the workflow such as the throughput, capacity utilization, frequently malfunctioning assets, level of worker efficiency, collaboration levels, and so on.
Inspecting the exiting workflow thoroughly will lead manufacturing organizations to the next point.
Detect the Bottlenecks
When an organization inspects its current workflow within one of its plants, it’s quite natural that it will find at least a significant bottleneck in the production process, if not more.
For instance, upon inspection, a maintenance manager finds that one of its conveyor belts has been down for the past few days. The semi-finished products cannot use the offline conveyor belt for progressing to the next stage of production. These goods are either stuck or are being diverted to another conveyor belt - increasing the load on the latter. The offline conveyor belt creates a bottleneck as parts of the production are halted or delayed.
Bottlenecks aren’t exclusive to machinery - there can be administrative ones as well. Identifying such issues is one important part of improving manufacturing efficiency as it helps identify where the problems lie and address them effectively.
Reduce Waste if Possible
Waste can refer to several objects - time, energy, space, effort, materials, etc. Fortunately, inspecting the workflow and identifying the bottlenecks can highlight redundant processes, wasted materials, unused space, ventilation issues that lead to reduced productivity, and so on.
Working on the issues can help reduce wastage, improve manufacturing efficiency, and even generate revenue.
Processes that create excessive waste can be worked on to bring waste down to a negligible level by using more efficient practices, materials, or equipment.
Moreover, as recycling is a huge focus now, organizations can recycle and reuse the waste, and if not possible, then sell the recycled materials to interested parties - creating a win-win situation.
One fine example is machine lubrication - doing it excessively creates problems for the equipment, builds up debris, increases costs, and wastes resources. This can be optimized with lubrication management - questions like which machinery requires how much lubrication and on which days for optimal performance must be addressed.
Provide Proper Training to Relevant Employees
Improving efficiency is not all about the equipment - it’s about the people who operate them as well. One of the most common yet effective ways to improve manufacturing efficiency is by helping employees understand how to operate the machinery. If the employees efficiently operate the equipment, it will lead to reduced wastage and desirable results.
There are a few approaches to providing employees with the right knowledge. Teams that are directly involved with the machinery, such as the maintenance teams and machine operators, must be provided with training sessions. How the machine works, red-flags, common troubleshooting tips, as well as do’s and don’ts can be the subject of these sessions.
On the other hand, the machine operators need a direct approach - something which on-the-job training helps with. However, these must be closely supervised to avoid safety incidents. This also helps the machine operators work in a standardized manner - reducing waste and working in the safest and most efficient way possible.
Ensuring training sessions for only new employees isn’t enough - the experienced ones need training too as there might be new practices that help to handle the equipment more efficiently.
Ensure Preventive Maintenance
One of the biggest impediments to manufacturing efficiency is equipment failure and malfunctions. The saying “an apple a day keeps the doctor away” is applicable for equipment as well. However, for equipment, the apple is maintenance, and if organizations ensure it, then the equipment won’t be breaking down and requiring a “doctor”.
Organizations that understand this concept ensure preventive maintenance, that is, performing maintenance tasks even if the equipment is working properly. For them, utilizing solutions like CMMS software is quite common as they help streamline maintenance, improve collaboration, and simplify repairs.
Ensuring preventive maintenance helps organizations in several ways.
Via scheduled inspections and maintenance tasks, preventive maintenance helps detect if a piece of equipment has any underlying issues. This helps address the problems before they become serious and cause malfunctions. Preventive maintenance also helps equipment operate more reliably by servicing them regularly whenever needed. Moreover, since preventive maintenance is a proactive approach, it provides constant care to the equipment, helping them last longer, compared to corrective or reactive maintenance.
All of this helps the equipment run smoothly and reliably, reducing downtime in manufacturing facilities, and improving efficiency.
Efficiency is the Key to Improve Manufacturing Processes
Several organizations heavily focus on improving efficiency as it’s the last piece of the puzzle for them. While there will always be halts, bottlenecks, and equipment failures, some of the issues can be addressed if the right strategies are implemented - one of which is preventive maintenance. Not only does it improve manufacturing efficiency, but it also reduces workplace safety incidents and reduces replacement and repair costs down the line.
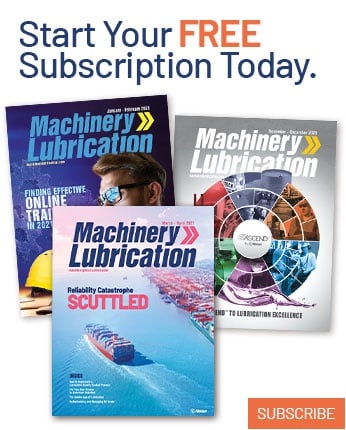