For weeks, everyone’s been hyper-aware of the good work frontline workers do to help us through this pandemic. We see so much imagery of healthcare workers in full protective gear, working tirelessly in emergency departments, postal and delivery workers walking up to our doors with important packages; and grocery store workers stocking shelves to make sure shoppers get what they need.
But there’s another essential frontline worker who is just as important amid this pandemic, but, because of lack of visibility, rarely gets mentioned in media: the factory worker.
We’re seeing how supply chains are being disrupted – resulting in grim shortages on shelves because of COVID-19. Protecting essential factory workers is key to the continued production and distribution of so many valuable consumer products (PPE, groceries, pharmaceutical drugs, etc.).
In this question and answer session with Parsable's Ben Cheng, we further explore the role technology is playing in keeping plant workers safe.
Reliable Plant: Tell me about the frontline factory worker, why do you think these workers play such a critical role in this pandemic?
BC: Throughout this pandemic, many frontline workers were quickly visible in our neighborhoods -- those working at our grocery stores, holding down our hospitals, delivering our mail and packages. Manufacturing frontline workers play just as important a role, though they're less visible because most consumers don't really think about how products get made and end up where they're needed. These workers are the people who power the heart of our supply chains -- the plant floor where raw materials go in and finished product comes out.
Without people to operate plants, the world would be at a loss and entire supply chains would be disrupted. The groceries and personal hygiene products would never make it to the supermarkets. Every product that's in high demand and is considered essential, especially during this pandemic, wouldn't get into anyone’s hands without the massive frontline factory workforce showing up every day to do their jobs, taking risks in the process.
But this situation begs the question: How are we supporting these workers? They play such an important role during this time of crisis, but who is watching out for them? We keep seeing cases of plant closures and high infection rates among plant workers. We need to better support them; they’re putting their health at risk, in many cases with little protection or insufficient adherence to safety measures.
RP: What are the biggest roadblocks or challenges that industrial frontline workers face today?
BC: Safety. Parsable works with global industrial companies with hundreds of sites and tens of thousands of employees, and it's top of mind for every one of them. It's the most immediate and critical issue that industrial companies are dealing with right now.
Beyond safety adherence itself, it's how to scale it across an organization. For large enterprise companies, having new safety protocols rolled out one plant at a time, each one taking months to implement, just isn't an option during this time when every day brings uncertainty. And with regulatory bodies like the CDC updating their recommendations often, by the time you finish implementation at a site, a new standard is available. The deployment process needs to be re-imagined. Time is not on your side.
For frontline workers, the reality is, it's difficult to follow social distancing guidelines when you have to move around throughout a plant, often in close proximity to one another. Social distancing is often impossible for certain production processes and the sheer number of people those processes require. A major rehaul of work standards -- if not the work itself -- is required, and that involves not just operations but human resources and many other stakeholders.
Another challenge is simply keeping up with production. By that, I mean either keeping up with the pace of production or keeping up with new processes as many manufacturers turn to making products outside of their typical arena, like face masks, ventilators and hand sanitizer. Rising demand requires faster work, and pivots in production processes require faster onboarding. It's a significant challenge these operations and, in turn, these frontline workers face.
RP: How is technology keeping them safer?
BC: There is almost an irony to factory workers pushing out millions and millions of PPE when they are, in many cases, not adequately protected themselves. On the factory floor, keeping workers safe goes beyond PPE -- it means limiting the spread. And that's where technology comes into play.
Connected worker technology, which essentially digitizes standard, paper-based operating procedures with the intent of helping continuously improve safety, productivity and quality across any operation touched by a human worker, is an answer. One obvious way that digitizing procedures helps keep workers safer is by eliminating contact with surfaces like paper, and eliminating the need to exchange documents with others on the plant floor. Digital sign-offs ensure social distancing protocols are maintained while still providing verification that necessary product quality and safety criteria are met.
But connected worker technology goes far beyond that. By incorporating safety measures directly into standard operating procedures, it can advise and alert workers to ensure they meet safety guidelines, like reminders to wash their hands, wear a mask or take their temperature. Any time new standards or updates are introduced, these can be quickly added to digital procedures and every worker who follows those procedures immediately gets the latest version, whatever plant they're in. By ensuring proactive safety steps are embedded within the work itself, it benefits everyone on every plant floor. This is safety at scale.
Connected worker technology also digitally captures operational and human activity data, which has undeniable value at a time when we're trying to limit face-to-face contact. For example, in the case of shift handovers, these typically require active information to be exchanged and issues to be talked through between one shift to the next. This includes factors like changes in the production schedule, equipment problems, and jobs that were not completed. A digital, mobile connected worker solution can track the real-time activity and progress level of tasks and procedures, decreasing and even eliminating the need for shift leaders and teams to talk face to face.
RP: Is connected worker technology helping them better meet growing production demand?
BC: Absolutely. Connected worker technology helps guide people to do their work effectively and accurately, which is so important right now for so many organizations as they pivot product and/or rush production to meet heightened demand. Many of our customers are actually operating at 24/7 capacity. As new workers are added to the frontlines, they can get up to speed quickly in their initial onboarding. For current workers who may be tasked with new or different responsibilities, having digital, multimedia work instructions and real-time collaboration through SMS text, video, photos and more makes it easier to transfer knowledge.
Also, because connected worker technology captures human activity data, plant managers have more access to what's happening on the plant floor. The technology can uncover roadblocks and pinpoint or reveal factors that may be causing it. Having that level of insight can help managers better adjust and control overall workflows and keep production moving at the pace it needs to, and with the quality of work it needs, to meet quota and customer expectations.
RP: Anything else you’d like to add on this topic?
BC: I’ll just add that technology can't and shouldn't be the only safety measure that plants put in place for their employees, of course. Plants need to have comprehensive, strict and crystal-clear safety policies in place to make sure they are not unwittingly putting employees at risk in any way. That really needs to start from the top down, and requires collaboration across all departments and functions, not just the safety management or EHS team. Most, if not all, of our customers recognize this, and also recognize that connected worker technology is a critical component of truly building a safety-first culture.
Ben Cheng Bio:
As Vice President of Customer Operations at Parsable, Ben manages the company’s customer success, value consulting and support teams to ensure a world-class experience and to drive positive outcomes for new and existing customers. Ben has nearly two decades of experience ranging from sales and marketing to planning, supply chain optimization, business excellence, and IT, with a focus on big data, advanced analytics, and the Internet of Things (IoT).
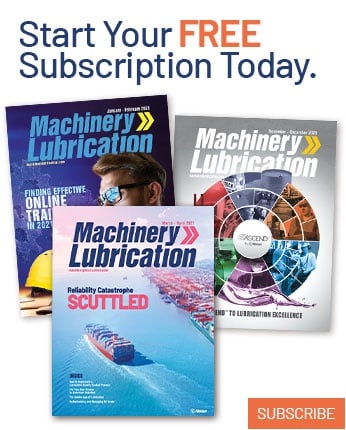