The efficiency of your supply chain can be a make-or-break factor for your company's success. At the heart of this efficiency is your warehouse layout: a poorly designed warehouse can lead to a cascade of inefficiencies, from delayed shipments to increased costs.
This guide offers a 6-point evaluation framework for an effective warehouse layout: we'll explore the critical elements that go into designing an effective warehouse layout, helping you avoid common pitfalls and maximize operational efficiency.
1: Recognize the Warehouse's Primary Objective
Understanding the primary objective of your warehouse is the first step in any design or redesign process. Are you storing perishable goods that require temperature control? Or perhaps you're in the electronics sector, where anti-static measures are crucial? Each industry has unique requirements that your warehouse layout must accommodate.
An effective warehouse design must strike a balance between maximizing storage space and ensuring easy access to products. This involves a deep understanding of your inventory — knowing which items are fast-movers and which are slow-movers — and planning your space accordingly.
Adaptability is key. Your warehouse should be designed to quickly adapt to changing business needs, whether it's a sudden spike in demand or the introduction of new product lines.
-
Takeaway: Your warehouse layout should be a living, breathing entity that aligns with your primary objectives and can adapt to changing business conditions.
2: Prioritize Flow and Accessibility
Inefficient movement within a warehouse can have a domino effect, leading to increased labor costs, delayed order fulfillment, and even workplace accidents. The layout should aim to create a 'golden path' — the most efficient route for moving goods from receiving to storage, picking, and finally, shipping.
Warehouse Management Systems (WMS) have evolved to include features like heat maps, which show the most frequently accessed areas, and dynamic slotting algorithms that suggest optimal locations for products. These tools can be invaluable for optimizing flow and reducing travel time within the warehouse.
Strategies like zone picking (where workers are assigned to specific areas) and wave picking (where multiple orders are picked simultaneously) can further optimize flow. These strategies, however, require a layout that supports them, with clearly defined zones and efficient routing paths.
-
Takeaway: Flow optimization is a multi-faceted endeavor that involves layout design, technology, and picking strategies. Each element should be carefully considered and aligned with the others.
3: Decipher Optimal Storage Solutions
The range of storage solutions available today is vast and varied. From selective racking, which offers high accessibility but lower density, to drive-in racking, which offers the opposite, the choices are numerous. The decision should be based on a variety of factors, including product size, turnover rate, and even the type of equipment used in the warehouse.
A detailed SKU (Stock Keeping Unit) analysis can provide insights into product velocity, seasonality, and other factors that can influence storage decisions. For example, fast-moving SKUs might be best stored in a gravity flow rack, which uses rollers to automatically move products forward as items are picked.
-
Takeaway: Optimal storage solutions are not a matter of 'one-size-fits-all' but require a deep understanding of your inventory characteristics and operational dynamics.
4: Uphold Safety and Compliance
Safetyshould be a foundational principle of your warehouse design. This includes not just the obvious elements like fire exits and safety barriers but also less obvious factors like ergonomic design to reduce strain injuries.
Compliance is another complex landscape, with various regulations at the federal, state, and even local levels. These can include fire safety codes, OSHA regulations, and even industry-specific guidelines. Non-compliance can result in hefty fines and legal complications but, more importantly, it can put your employees at risk.
Regular safety audits, including third-party inspections and internal reviews of your warehousing services, should be part of your operational calendar. These audits can identify potential safety hazards and compliance issues before they become critical problems.
-
Takeaway: Safety and compliance are ongoing processes that require regular audits, employee training, and a design that inherently minimizes risks.
5: Ensure Flexibility and Scalability
Market demands are not static; they are influenced by a host of factors including seasonality, economic conditions, and consumer trends. Your warehouse layout should be agile enough to adapt to these fluctuations without requiring a complete redesign.
Modular storage systems, like adjustable pallet racking or modular mezzanines, can be easily expanded or contracted. This allows you to quickly adapt to changes in inventory levels or even to add new functionalities like packing stations or quality check areas.
-
Takeaway: Flexibility and scalability are not just buzzwords; they are essential design principles for any modern warehouse aiming for long-term success.
6: Integrate Tech
The integration of technology into warehouse operations is part of a broader digital transformation affecting all industries. From automated guided vehicles (AGVs) that move products within the warehouse to IoT sensors that monitor temperature and humidity in real-time, technology is reshaping the warehousing landscape.
Advanced analytics tools are one facet of this tech renaissance: they can process the vast amounts of data generated by modern warehouses to provide actionable insights. These can range from optimizing workforce allocation to predicting maintenance needs for warehouse equipment.
-
Takeaway: Technology integration is a complex but necessary step for modern warehouses. It requires not just the adoption of new tools but also a cultural shift towards data-driven decision-making.
Measuring the Success of Your Warehouse Layout
Don't just set it and forget it; your warehouse layout should be regularly reviewed and updated based on performance metrics. KPIs like picking accuracy, inventory turnover rates, and employee satisfaction can provide valuable insights into how well your layout is performing.
Additionally, employee feedback can offer ground-level insights that are often overlooked but can be invaluable for continuous improvement.
Given the rapid changes in market demand, especially exacerbated by factors like global supply chain disruptions and e-commerce booms, is your current warehouse layout agile enough to adapt? Can you swiftly reconfigure storage solutions, adjust picking routes, or even repurpose zones? And how effectively is your warehouse leveraging Industry 4.0 technologies like IoT, AI, and robotics to not just improve but revolutionize operational efficiency?
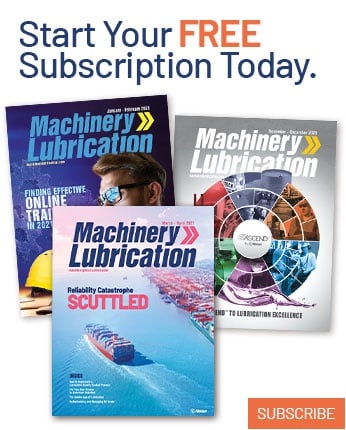