Manufacturing and process industries lose an estimated $20 to $60 billion each year due to unscheduled downtime and poor asset quality. Most organizations are fully aware of this and say improving uptime is their main goal for implementing a predictive maintenance plan.
Predictive maintenance is a maintenance plan that monitors the performance and condition of equipment under normal operating conditions to reduce the likelihood of failure; the goal being to predict when a failure might occur and then attempting to prevent the failure by implementing corrective maintenance.
Predictive maintenance is only successful through condition monitoring — the continuous monitoring of assets during normal operating conditions. Condition monitoring is done through three facets: online, periodic and remote monitoring. These facets are achieved by implementing things like infrared thermography, acoustic monitoring, vibration analysis and oil analysis.
Reliable Plant wanted to find out what types of maintenance programs are being used in plants across the world and how maintenance personnel view certain topics related to predictive maintenance. We polled nearly 150 maintenance managers and supervisors across more than 20 industries, including power generation, petroleum, mining, food processing and paper, and asked them about their current maintenance plans. Following are some of the key findings:
- 76% of respondents say they currently use preventive maintenance (down slightly from a 2018 study), while 65% currently use predictive maintenance (an increase of 11% from a 2018 study).
- Almost 60% of respondents said they use a reactive (run-to-failure) maintenance plan (up by 9% from a 2018 survey).
- Compared with nearly 10 years ago, maintenance personnel still view vibration, oil and thermography analysis as the best methods to predict early machine failure, with 62% looking solely at vibration analysis.
- Regarding internet-connected predictive maintenance, the majority of respondents are most concerned with the lack of internal skilled personnel (71%), followed by data standardization issues (69%).
- Only a little more than 5% use internet-based systems for their predictive maintenance plans.
What types of maintenance are currently used at your plant?
Implementing predictive maintenance is very cost-effective, saving organizations between 8% to 12% over preventive maintenance and up to 40% over reactive maintenance, according to the Department of Energy. Despite this, preventive maintenance is still favored by 80% of maintenance personnel, based on a maintenance survey by Plant Engineering last year. That same survey showed predictive maintenance was used by 51% of plants. Given this information, we wanted to see what types of maintenance plans our respondents are currently using.
When asked what type of maintenance is currently being used in their plants, preventive and predictive maintenance were the most common at 76%, down slightly from last year. Predictive maintenance is being used by 65% of maintenance personnel, an increase of 14% from the Plant Engineering survey. It's interesting to note that nearly 60% of respondents say they use reactive (run-to-failure) maintenance. Rounding out our responses are proactive maintenance (monitoring and controlling root causes) at 40% and prescriptive maintenance (detecting and prescribing to fix problems) at 34%.

Which technology provides the best overall early warning of pending machine failure?
A 2010 survey by machine reliability solutions company AzimaAI showed vibration, oil and thermography analysis (in that order) were the primary components of predictive maintenance programs among respondents. In fact, those three were used by a large margin — 85% for vibration analysis, 75% for oil analysis and 71% for thermography analysis.
When it comes to predictive maintenance tools, we wanted to know which technology is the best method of early warning detection in the eyes of our respondents. Coincidently, this seems to coincide with AzimaAI's survey from nearly a decade ago. More than half (51%) of respondents said vibration analysis is the best method for detecting potential issues, followed by oil analysis at 23% and infrared thermography at 11%. Twenty-one percent of respondents said ultrasonic and motor current analysis were the best predictors.

While most believe vibration analysis provides the best early warning detection of machine failure, oil analysis is often overlooked as the unsung hero.
"We know that oil analysis can provide signs of failure before vibration in most cases or even pre-failure signs," says Bennett Fitch, director of product development and LPD services for Noria Corporation. Fitch goes on to explain this lack of knowledge could be due to inefficient oil analysis programs, missing metrics on pre-failure catches and marketing trends, among other things.
Do you currently view and analyze predictive maintenance data in real time?
Analyzing real-time data is one of the biggest benefits of a predictive maintenance strategy. This data can come from a continuous stream of information from onboard sensors (often IoT sensors) built into machines or from things like oil sight glasses that allow you to see the current condition of lubricants. Real-time data can also come from instruments like infrared cameras and vibration sensors. Structured and unstructured data is then routed to a scalable database where it can be analyzed to form maintenance plans and schedule tasks.
Reliable Plant wanted to get insight into how much real-time, condition-based monitoring occurs when it comes to using the previously mentioned technology. When asked if they currently view and analyze predictive maintenance data in real time, 25% of respondents said they do not view and analyze any of the listed technologies in real time. Of the 20% who analyze only one technology, real-time vibration analysis monitoring is the most commonly used at 62%. Nearly 55% of respondents analyze more than one technology, with the most common pairing being vibration and infrared thermography. The full results are as follows:
- Vibration analysis: 55% Yes, 45% No
- Oil analysis: 34% Yes, 66% No
- Infrared thermography: 46% Yes, 54% No
- Ultrasonics: 34% Yes, 66% No
- Motor current analysis: 30% Yes, 70% No

How concerned are you with the following issues regarding internet-connected predictive maintenance solutions?
Integration with the internet is all but a given when it comes to implementing predictive maintenance. The vast amount of condition-based historical information needs to be tracked somewhere, and that is most likely through an integrated enterprise asset management (EAM) or computerized maintenance management system (CMMS) software or other type of system. In fact, nearly half of maintenance personnel use an integrated EAM/CMMS or historian software to collect and track data, according to a study from Plant Services.
Modern plant equipment is much more intelligent than equipment from the past, as most machines now interact with internet-based software to provide and track real-time data. We asked respondents which best represents the current level of predictive maintenance at their facility: computer-based, SCADA-based, wireless-based, internet-based or none of these. Somewhat surprisingly, only around 5.5% of respondents said they use internet-based systems. The majority (65%) said they utilize a computer-based system, while around 4.9% use SCADA-based systems or none of the above (19%). That's nearly 89% of plants not using internet- or wireless-based connectivity. One possible reason for this could be due to a lack of skilled personnel.

As of 2018, finding skilled workers to fill open positions was ranked as the No. 1 challenge by respondents, followed by a lack of knowledge capture/transfer and retraining/upskilling, according to the 2019 Workforce Survey from Plant Services. This problem does not seem to have gotten any better over the last decade. Insufficient staff, not enough in-house expertise and poor training were the top three barriers for a successful predictive maintenance plan, based on a 2010 survey from Azima.
Reliable Plant wanted to know the biggest concerns maintenance managers and supervisors had with internet-connected predictive maintenance solutions. We asked about issues relating to security, information technology (IT) integration, return on investment, data portability, lack of internal skilled personnel, vendor incompetence and data standardization. The greatest concern among respondents was the lack of internal skilled personnel (71% were concerned or very concerned). This was up 11% from 10 years ago and still the top concern.
Of respondents who monitor more than one technology in real time, most were concerned or very concerned how it would integrate with IT. Finally, the biggest issue for those who aren't currently monitoring in real time is data standardization.

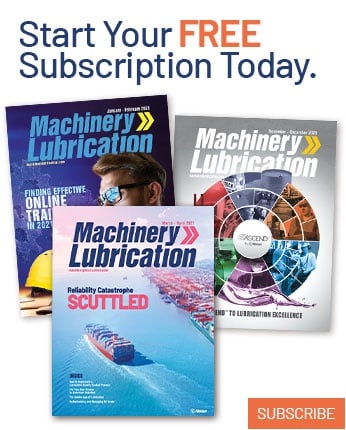