When considering what an organization must have for consistent production, more often than not a facility’s safety is not the first thing to come to mind. But dig a little deeper and you’ll find that the safety of a facility comes from the very aspects that make for efficient production. What are these key factors? From the technical know-how of operating machines through training to maintaining machines that operate at high levels, every aspect of safety leans toward efficiency. Below are five necessary steps to improve the safety of a standard production facility.
1. Ongoing Safety-Focused Training
All new machine operators and maintenance technicians should have a mandatory training process so they can be eased into using and maintaining complex assets. This requires each employee to go through the same safety training exercises using each machine at the facility. Even if one has been working at the plant for a long time, machines are constantly changing as technology evolves. Schedule a few days each year with your employees and conduct the necessary training to ensure everyone stays up to date with the safest way to use the equipment.
In addition, having a safety test administered at the end of the training helps to confirm that personnel understand their own experience level. It might seem like wasted time from normal production, but it’s not. Unfortunate accidents cause huge declines in output through long delays. This alone should give you enough reason to dedicate time to safety awareness training.
2. A High-Performing Asset Is a Safe Asset
As the saying goes, “You can hurt yourself far worse with a dull knife than a sharp one.” This applies to heavy machines, too. New machines work with ease and can get the job done fast. However, after enough wear and tear, every machine comes to a breaking point. If you are running the equipment past its recommended limits and don’t pay close attention to its performance and condition, you are asking for trouble. This situation can result in an endless list of problems that create hazards for both the user and those around the machine as well.
Using proper lubricants will help keep machines functioning at their highest level for longer periods of time. On the contrary, one of the quickest ways to run down a machine is to not oil it or grease it regularly. This not only leads to a machine that functions in unpredictable ways but also one that can break down unexpectedly and even put an operator in danger in the process.
Maintenance strategies such as predictive maintenance are very useful in increasing the reliability and availability of critical assets. By better understanding your equipment and identifying when it will begin to wear down, you will know what you can do to prevent a machine breakdown. Ultimately, machines that are operated in the optimum condition by people who know how to interact with them are highly unlikely to cause safety problems.
3. Keep Your Facility Tidy and Organized
It is common to race the clock throughout the day. In a plant where many people are operating large machines and each individual is trying to work at the quickest possible speed to make progress on the busy schedule, accidents can occur that otherwise could have been prevented. This might involve empty boxes obstructing a lane, spilled liquid that will be cleaned later, wires and tape that will be put away as soon as the next order is filled, etc. During the pressure of the day, it’s understandable that organizing and cleaning tasks may get pushed back to whenever one has time. In the end, though, this can be a big safety concern.
Keep in mind that a facility’s safety is increased tenfold the moment an operation makes cleanliness and order the main focus. By acting on spills and accidents as soon as they happen, the hazard is almost removed completely. When each team member does his or her part, everyone can have more peace of mind. Waiting for someone to get seriously injured before introducing necessary changes is simply bad practice.
4. Review Your Facility's Layout for Possible Dangers
You may have worked at your facility for years and know where everything is, but that doesn’t mean everyone else does, too. Verify that there is quality lighting in every area of your facility, especially around signs. Also, the message behind each sign must be fully understood by all employees to ensure everyone knows what safety precautions to take.
If your facility has piping systems, take great care in labeling each of the pipe’s contents. When there is a damaged pipe, repair or replace it before the damage increases. Always expect the worst and prepare accordingly.
If there are chemicals in your facility, each worker must have sufficient understanding of the hazards and risks involved in the unfortunate event of a chemical leak. This would include what steps must occur, how to deal with an accident and what to do if you have been exposed to the chemical.
Floor markings provide another great way to stay on top of possible dangers. These types of markings are used to alert facility personnel of dangerous chemicals. They can notify anyone in the area about which places are not safe to walk and can alert personnel of hazardous zones in a facility that are normally safe.
5. Routine Machinery and Building Safety Checks
Scheduled safety checks are key. Set a date at the beginning or end of the month and devote a large portion of the day to evaluate the following:
- Employees are using protective equipment at all times.
- Daily proactive maintenance checks are being performed.
- Walkways and stairwells are free of debris.
- Emergency exits are unlocked and easily accessible.
- Stray cords are put away.
- Liquids are dried and cleaned from all surfaces.
- All chipped concrete or holes have been covered or smoothed out.
Lessons Learned
Safety is the backbone of all plants. Without safety, you have accidents and machine failures, which lead to delays and people getting hurt. However, with safety, you have efficient and consistent output, which is the goal of all organizations. By keeping safety at the heart of every decision you make in your facility, there’s no question you will lead a successful operation.
About the Author
Bryan Christiansen is the founder and CEO at Limble CMMS, which is a mobile computerized maintenance management system that helps managers organize, automate and streamline their maintenance operations.
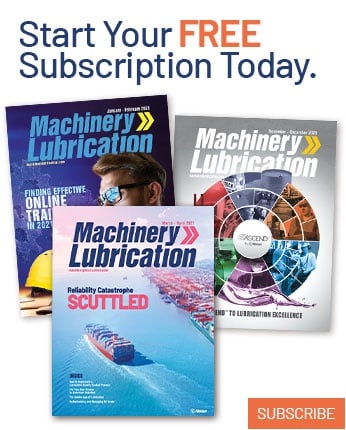