Material handling is accompanied by numerous risks, especially when done manually. Tasks such as lifting, carrying and pushing can make the workplace unsafe for employees. Material handling injuries can also be quite expensive with medical costs, lost productivity and decreased employee morale. As an organization, you must take preventive measures to minimize injuries and the costs associated with them. Following are six material handling tips that can help.
1. Minimize Ergonomic Risk Factors
Ergonomic risk factors are those problems that cause unnecessary physical fatigue in employees. These risk factors are commonly found in the manual material handling environment. Three primary factors include stressful postures while handling materials like bending or twisting, highly repetitive motions such as frequent reaching and lifting, and forceful exertions like carrying or lifting heavy loads. Identify all such ergonomic risk factors and minimize them by putting control measures in place to limit the exposure of employees to all possible risks.
2. Provide Personal Protective Equipment
Offering protective equipment to workers will greatly minimize injuries when moving materials manually. Basic protective equipment includes eye protection, helmets, gloves, steel-toed safety boots and metal fiber or plastic metatarsal guards to protect the in-step area from impact or compression.
3. Upgrade Your Equipment
You can minimize manual material handling by upgrading your equipment. Use conveyor belts as well as forklift and conveyor belt scales to move materials rather than carrying them manually. This not only will help to reduce the material handling risks but also increase productivity and profitability.
4. Reduce Noise and Vibration
Noise and vibration are widespread in many plants, making it imperative to protect your employees’ hearing. Vibration causes noise, but it can also lead to work-related musculoskeletal disorders and general employee fatigue. By introducing the right equipment, such as wheel materials, you can greatly decrease noise and vibration. Matching the wheel materials to the floor surface will minimize vibration and noise as well. You can also use shock-dampening casters and softer wheels to reduce noise and g-forces on a wheeled cart.
5. Respond to Reports of Employee Fatigue
Physical weariness and fatigue are common occurrences in manual material handling tasks. Regardless of whether you have an excellent ergonomic process that caters to the workers’ capabilities, daily manual work can take a toll on your employees’ health. Cumulative fatigue eventually will give way to a musculoskeletal disorder. Therefore, you must encourage employees to report any signs of discomfort and fatigue so you can respond quickly and put control measures in place to prevent fatigue from developing into serious injuries.
6. Use the Right Equipment
Manual material handling is risky, time-consuming and laborious. By choosing the right equipment, you can make the process safer, faster and efficient. Conveyor belt systems offer numerous benefits for handling weight loads of various sizes and styles. Material handling equipment is also available in the form of storage equipment (shelves, racks and pallets) and bulk material equipment (trucks, silos, drums and grain elevators). Designate and train the appropriate individuals on the correct procedures and verify that they always follow the rules. Regardless of the size of the equipment and the simplicity of using it, ensure that only authorized and trained individuals operate it.
About the Author
Kevin Hill leads the marketing efforts at Quality Scales Unlimited in Byron, California. Besides his day job, he loves to write about the different types of scales and their importance in various industries. He also writes about how to care for and get optimized performance from different scales in different situations.
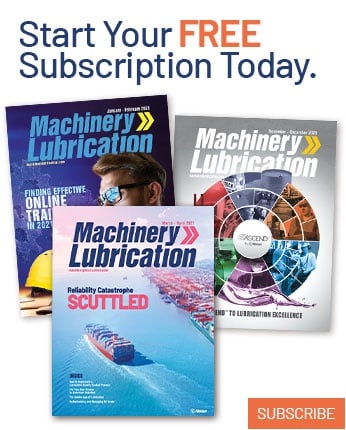