"We don't have a safety culture."
This is the lament of every frustrated environment, health and safety (EHS) officer who is trying to reduce injuries while fighting unsafe attitudes every step of the way. The truth is that every organization has a safety culture, but if you find yourself reminding everyone why personal protective equipment (PPE) and proper lockout/tagout procedures are important, you’re probably working within a weak safety culture. So how can you bring safety to the forefront of everyone’s mind, from management to the factory floor?
The Cost of Unsafe Practices
The first step to solve any problem is to understand it. Since management sets the tone for attitudes about safety, that’s where you need to start. It’s not as though the upper echelons want to see injuries; they just don’t see the point of spending more money on safety tools or PPE that isn’t mandated by regulatory bodies. That stuff is expensive, right? Well, yes and no.
Sure, the price of safer tools is higher than the price of cheap, unsafe versions that get the job done, but at what cost? Let’s look at lacerations, one of the most common injuries across workplaces. According to the Occupational Safety and Health Administration (OSHA), a single laceration injury costs an estimated $19,713 in direct costs and $21,684 in indirect costs, for a combined total of $41,397. In addition, the estimated sales required to cover total costs is a whopping $1.3 million. And remember, that’s only for one laceration. That safety knife doesn’t look so pricey now, does it?
Once management understands the cost implications of business as usual, they often get onboard with preventive measures. The next step is to ensure all employees take safety seriously.
10 Quick Ways to Turn Around Unsafe Practices
Sometimes all we need to get going is a bit of momentum. It may not feel like you’re doing much, but a few changes can give you a quick win and get people moving in the right direction. They also tend to cost less and therefore are more likely to be approved by any management that’s still skeptical about the value of safety.
Before you start, and whenever possible, find a meaningful way to measure the effect of these changes. Any time you can show numbers (especially with dollar signs attached) that make a clear case, you’ve got a stronger argument for change. Try any or all the following quick starts:
1. Post Signs, Posters and Visual Aids
Make it clear at a glance that safety is a priority. Include signs in any language your workers speak, and don’t forget to rotate poster locations every so often so they don’t become visual "background noise."
2. Use the Power of Checklists
These can be used for any regular safety inspection — daily, quarterly or yearly — and serve as a great reminder so employees don’t overlook safety details. Filling out a checklist doesn’t add much time to a worker’s day, but it can save a life.
3. Integrate Safety into Existing Training
Chances are some type of training is already occurring at your plant. Add a safety component to what’s already there. For example, work with your human resources department to add safety into their onboarding procedures for new employees. This starts workers off on the right foot and doesn’t cost much more than what you’re already spending on training new hires.
4. Encourage Safety Suggestions from Workers
These can be anonymous if you feel workers will fear reprimands for speaking out. When aluminum giant Alcoa did this in the 1980s, it improved their safety record and had a positive ripple effect on the bottom line to boot.
5. Incorporate Safety Quizzes
If you don’t know where to start, head to Google and search for "how to write a successful workplace safety quiz."
6. Utilize Online Resources
Speaking of the internet, it’s a boon of fantastic and free safety resources, including training ideas, videos, quizzes, safety plans, checklists, etc. If you can name it, you can probably find it.
7. Change How Safety Information Is Delivered
You know your workers best, so consider new ways of disseminating safety information tailored to their habits. A daily email or tweet with a safety tip of the day might be a great way to reach millennials, for example.
8. Distribute Safety Tips
Walk the floor and pass out safety tips according to what you observe. Keep in mind that people don’t react well to a perceived scolding, so make it clear that your primary concern is their health and safety; you’re not trying to "catch them" doing something wrong.
9. Include Employees in Safety Presentations
If you already have regular safety training sessions, consider co-presenting the material with an employee. It doesn’t have to be a safety expert. In fact, it’s better if this is just an average employee. It forces them to learn the material well and gives listeners a break from listening to the same voice all the time.
10. Ask for Advice
Ask people what kind of training would help them make safety a priority. People love to be asked for their advice, and even if you don’t implement every suggestion, you’ve got them thinking about safety.
Long-Term Changes: Strengthening Your Safety Culture
Once you’ve done the quick and easy stuff, it’s time to look at making a deeper culture change. This includes the attitudes and habits that don’t change overnight but offer the most meaningful and long-lasting returns. This is the hard stuff, but it’s also the rewarding stuff.
Understand Priorities
Work on understanding everyone’s priorities so you know how to sell them on a new idea. Some jobs focus on efficiency, for example, so take that into account with any new safety procedure that will affect workflow.
Perform a Safety Audit
Perform a safety audit to prioritize safety improvements. Find out where company injuries are the worst and start there. Track your progress so you can include lessons learned in your next area of focus.
Have the Right Tools
It is essential that everyone has the right tool for the job at hand. Accidents often happen when a tool is used for a task it’s not designed to handle.
Consider Ergonomics
Don’t forget ergonomics while you’re considering better tools. Repetitive strain injuries are expensive for the company, as they take a long time to heal.
Be Innovative When Presenting Safety Information
Up your safety presentation game by researching novel ways to present materials. Again, the internet is a great starting place for ideas.
Have Toolbox Talks
Incorporate toolbox talks into your daily routine. These quick, to-the-point chats start a shift off right by introducing a focused safety topic that sets the tone for the day. Sometimes small messages repeated often are more effective than an hour-long lecture.
Employ Safety Experts
Take advantage of local trainers and experts from safety councils, training consultants or manufacturer representatives. This mixes up the training and saves you time researching narrow topics where others have greater expertise.
Ensure Incidents Are Reported
Get serious about your company’s incident reporting structure to ensure you hear about every incident. Even more importantly, make it an ironclad rule that appropriate follow-up happens every time. This is essential to building trust.
Research PPE Options
Research every piece of PPE and evaluate its purpose and effectiveness. Make sure you know about all the options out there so you can make the best decision for your work environment.
With a strong safety culture, everyone benefits: employees and their families, managers looking to meet company goals, and yes, even the bottom line. Good luck and work safe!
About the Author
TJ Scimone is the founder and CEO of Slice Inc. Since 2008, he has worked with world-renowned engineers to rethink every aspect of safety while creating a unique line of cutting tools.
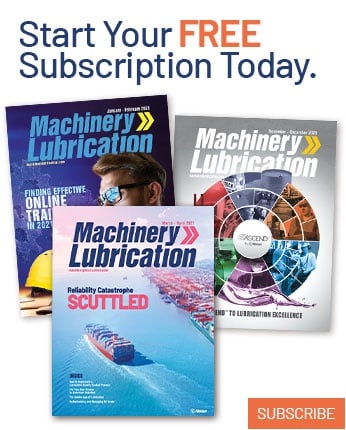