Employee recruitment and retention are among some of the biggest challenges for manufacturing today, as technologies like robotics and automation are being introduced that require new skill sets not traditionally required for plant workers.
The reality is that the nature of the work manufacturing organizations do has fundamentally changed. With more and more processes relying upon technology, manufacturers need employees who are highly skilled in technology, data science and engineering.
The manufacturing industry is changing, but that does not mean it is dwindling. On the contrary, the United States has the second-leading manufacturing economy in the world. According to MarketWatch, "the value added by U.S. factories is more than $2 trillion a year, equal to the next three countries (Japan, Germany and South Korea) combined. U.S. manufacturing is still the envy of the world."
As baby boomers retire out of the field, turnover rates are increasing and manufacturing is left with a new workforce comprised of millennials. Millennials are defining the way work is being done, and they have high expectations for their work environments. They use technology in almost every aspect of their personal lives and have come to expect the same level of technological conveniences at their places of work. If a company is not providing technical benefits like mobility, ease of use and self-service, then millennials will find other jobs that meet these expectations.
Turnover in the industry is alarmingly high, but at least equally concerning is the growing skills gap. Over the next decade, nearly 3.5 million manufacturing jobs will likely need to be filled. The skills gap is expected to result in 2 million of those jobs going unfilled.
With the bulk of the manufacturing workforce retiring, the need for technological know-how on the rise, and the flood of millennials with high expectations taking over the potential employee pool, how are manufacturing organizations going to reduce turnover and fill in the skills gap?
The answer lies in creating a workplace that addresses and meets the needs of the new workforce. One can't change the entire way an industry is managed without also stepping up to advance the workplace environment for employees. Since manufacturers need to retain this new millennial-led, technologically savvy workforce, they should work toward meeting their expectations. If factories and plants are becoming digital, so too should the human resources (HR) function.
There are five steps manufacturing organizations can take to get them on the path toward having an efficient, effective and engaging digital organization:
1. Transition to the Future of Work
As mentioned previously, manufacturing organizations need to meet the demands of the new, millennial-led workforce. That means understanding how work is being done today and how it will be done tomorrow. Manufacturers that look ahead to understand how work will be done in the future and how to meet the needs of the future workforce while also equipping themselves to be ready for future shifts will likely see that they are often more prepared for future changes in the type of work being done and in the workforce that will do the work.
2. Create the Simply Irresistible Experience
Employers can drive employee engagement by creating a "simply irresistible experience." Focus on five strategies: meaningful work, supportive management, a positive work environment, growth opportunities and trust in leadership. By prioritizing employee engagement and satisfaction through a simply irresistible experience, manufacturers will likely attract and retain the skilled talent they need.
3. Optimize the Human Capital Balance Sheet
Human capital is one of the biggest elements of any profit and loss (P&L) statement. If your spending and return on investment are not being monitored, analyzed and optimized properly, the bottom line will be affected, which can in turn damage brand reputation — a hit manufacturers cannot afford to take when competing for highly skilled talent. By proactively managing the human capital balance sheet and developing processes focused on value, manufacturers can drive long-term positive results, both for the bottom line and for talent management and retention.
4. Activate the Digital Organization
With a digital organization and mobile, online, easy-to-use systems, manufacturing organizations can optimize their HR efforts while at the same time meeting the demands of their employees. Having a streamlined digital workplace not only helps to retain and attract the incoming workforce, but it also is good for the bottom line. Automated digital tools can enable an organization to predict when/if future issues could arise, indicate where people need to be better trained, identify labor spend inconsistencies or misalignments, improve scheduling processes, open communication between staff and managers, provide easy time entry, and facilitate the ability to quickly disseminate information to the entire company.
5. Sustain Organizational Performance
Steps 1-4 explain how to rebuild an organization in a way that can attract qualified talent and improve the bottom line, but in order to reduce turnover and improve employee retention, you must sustain this new organization and its high performance. It is not enough to complete the first four steps once and just sit back and enjoy the fruits of your efforts. Manufacturers should consider becoming ever adapting and growing, just like their employees. The moral of the story is that for today's employees to feel motivated, connected, appreciated and engaged, the flexibility and technology that they experience every day in their personal lives must also be available to them in their careers.
Manufacturing is at an interesting crossroads where automation is decreasing the amount of human power needed to operate a facility while the bulk of the manufacturing workforce is retiring rapidly, leaving upward of 3.5 million manufacturing jobs open. It isn't too late for manufacturers to reduce turnover and fill their open positions with qualified employees. Uncertain times in the United States are proving to breed more company loyalty, which is good news for employers. This alone though does not guarantee your workforce will stay put in the future. Manufacturers must step up to meet the demands of this new workforce by establishing a digital workplace.
About the Authors
Michael Gretczko is a principal at Deloitte Consulting LLP and general manager of ConnectMe, which delivers a modern solution for the digital workplace.
Brian Day is a senior manager at Deloitte Services LP focused on taking ConnectMe to the marketplace.
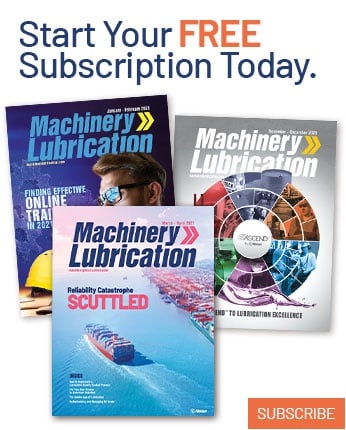