The U.S. Chemical Safety Board has documented the frequency of chemical accidents as well as the devastation they can cause for workers and communities. Even a cursory review of the organization's website reveals the need for chemical safety standards. Below are nine key safety tips for plants that store chemicals.
1. Develop a Chemical Hygiene Plan
The Occupational Safety and Health Administration (OSHA) specifies certain elements that must be included in a plant's chemical hygiene plan. These requirements are spelled out in the details of 29 CFR 1910.1450.
2. Never Skimp on Training
Industrial accidents cost industry millions of dollars every year, but safety is much more than a budgetary line item. It is an important responsibility to workers and their communities. To ensure the safest possible operations, provide regular training to every employee who comes in contact with chemicals. The training should cover how to handle and package the material, the required safety gear, and emergency and evacuation procedures in the event of a spill. Training should be repeated at frequent intervals so that it is fresh in the minds of all employees.
3. Standardize Procedures
While every chemical has some unique aspects for safe handling, there also are many steps that apply for all chemicals. To make it easy for your team to follow safe handling procedures, start with the common steps, such as always wearing safety equipment and inspecting containers before putting chemicals in them. This helps reinforce the basics and makes it easier to follow the unique requirements of specific chemicals.
4. Practice Good Housekeeping Techniques
Neatness counts when it comes to safety. Keeping aisles clean and clear will prevent trips and falls, and putting tools or equipment away after use will help to avoid incidents such as dropping or knocking containers of chemicals off benches and tables.
5. Provide High-quality Safety Gear
Doing everything you can to keep your employees safe includes providing the right high-quality protective clothing and gear to protect them while handling chemicals. OSHA specifies the equipment that should be provided and requires that it meet the quality standards established by the American National Standards Institute (ANSI). Provide training and instruction on the usage of the safety gear, and ensure that people use it at all times.
6. Ensure Adequate Ventilation
Many chemicals are volatile and can cause issues even at low concentrations. To prevent problems, verify that the heating, ventilation and air conditioning (HVAC) systems in place are operating effectively and that they are adequate for the space. Consider adding additional fans if necessary to meet OSHA indoor air quality guidelines.
7. Use Tools and Containment
Using containment trays when handling volatile or dangerous chemicals is a good practice that can limit the damage from accidental spills. In addition, before transferring chemicals from one container to another, it should be a standard operating procedure to inspect all containers to confirm they are clean and free from chips or cracks.
Some chemicals require storage in air-tight containers; others need to be stored in a specific temperature range or in containers made of certain materials. Your team should know where to find the documentation for safe handling of every chemical you use. You must also have the right containers available for every chemical on your premises.
8. Segregate Incompatible Chemicals
Some chemicals ignite, explode or burn when combined, so keep them segregated unless your process requires them to be mixed. To prevent accidental combinations due to spills or vapors, store these incompatible substances at a safe distance from each other. Designate different areas of the stockroom for each chemical and make sure material handlers understand the importance of keeping them segregated.
9. Practice Spill Response
Accidents happen, so your team must know what to do in the event of a chemical spill. As is the case with fire drills and other emergency procedures, you should have spill-response drills and well-documented procedures. Take the time to train people on the correct procedures. These drills should be taken seriously and occur at intervals that are frequent enough so people will know what to do.
By following these guidelines for the proper handling of chemicals, you can help ensure the safety of your team and community.
About the Author
Lynn Place has 30 years of professional experience in the manufacturing, market research and advertising industries. Lynn is the vice president of marketing for SolvChem Custom Packaging Division, specializing in consumer packaged goods, new product development and strategic planning.
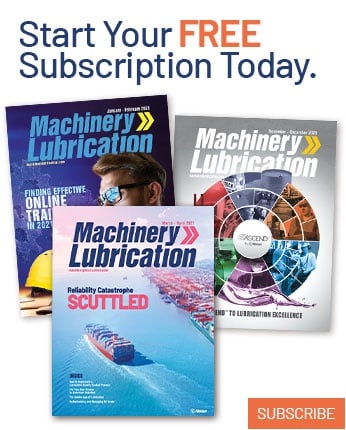