Maintenance operations present certain challenges. Unexpected repairs, efficient management of technician time and keeping up with preventive maintenance are just a few major areas that maintenance managers must address. However, these challenges can be met through effective planning and scheduling and by using technology.
Focus on the Basics
Planning and scheduling are two of the basics or fundamentals of maintenance management. If you do not have appropriate basics in place, no amount of technology can help. Once you determine the appropriate process flow and planning requirements for your maintenance operation, technology such as a computerized maintenance management system (CMMS) can help you tremendously. The trick is to make sure that your CMMS supports your process flow and planning and scheduling model.
Planning and Scheduling
In many cases, maintenance technicians find themselves “fighting fires” that come in the form of urgent work orders. Without effective planning and scheduling, time is wasted because priorities are not set and needed parts are not available.
When technicians are sent to complete work orders without proper planning and scheduling, they are frustrated by miscues, wasted time (looking for parts, unnecessary travel, etc.), and incomplete repairs. The requesters get frustrated when the job is delayed and they don’t know the reason why.
Planning is essentially reviewing jobs before they are dispatched to technicians in order to determine the necessary parts and tools and if they available, the level of skill set and time required, if a permit or special equipment is needed, if outside contractors are required, and if there are drawings or sketches to attach to the work order. Once the job is planned, it then must be scheduled. Part of scheduling is assigning an individual to do the job.
Many people think developing a planning and scheduling system for a maintenance department is a complicated task. However, it is similar to the process of starting a home-improvement project. You think through the steps, choose materials and then schedule the project.
The maintenance supervisor often believes more technicians are necessary. However, in most cases, it is inefficient work flow that leads to low labor productivity. Think of it this way: If you have a crew size of 50 technicians and you improve the productivity by 20 percent, you just hired 10 new technicians.
Managing Parts
A planning and scheduling system is not complete without establishing effective parts management. To ensure parts are available when work orders come in, the following steps must be taken:
-
Add a parts list to each piece of equipment. Technicians will not waste time looking up part numbers and corresponding vendors.
-
Instruct technicians to record substitute parts when discovered. This information can save another technician significant time later.
-
Review frequently used parts and delete obsolete items.
Receiving and Prioritizing Work Orders
Work orders are the key to successful planning and scheduling. Smooth maintenance department operation relies on how work orders arrive and how they are handled. In many maintenance operations, new work orders arrive by phone. With a large number of work orders per month, significant staff time is devoted to answering calls. In addition, it is easy for details to be lost when orders are delivered verbally.
Increasing the number of work orders arriving electronically instead of by phone can save time and reduce frustration. Electronically submitted work orders minimize communication problems because the requester’s exact words are recorded for easy reference.
An objective classification system is necessary to schedule work orders appropriately. A prioritization model should be used to code certain tasks as “urgent,” “important” or “could be completed at a later date.” It is important to limit the priority ratings to a few categories. Too many priority ratings are not practical. This system can be adapted to fit the needs of different operations.
The Role of the Planner
A planner serves as a central gatekeeper, making decisions regarding work orders. The planner’s tasks include making scheduling decisions based on preliminary investigations, grouping work orders for one building or location, confirming the availability of parts for the job, determining the availability of work areas and/or equipment, limiting interruptions to technicians’ work by assigning urgent requests only to dedicated or pre-assigned technicians, ordering parts, reviewing and revising preventive maintenance procedures, and participating in continuous improvement of work orders and the planning and scheduling process.
Stay on Task with Preventive Maintenance
An effective planning and scheduling process pays just as much attention to ensuring preventive maintenance is completed on schedule as it does to urgent work orders. To maintain regular preventive maintenance, the maintenance operation can predetermine the amount of time needed and the parts that are necessary to complete the work.
Benefits of Planning and Scheduling
Maintenance planning and scheduling prioritizes and organizes work so that it can be executed in a highly efficient fashion. Asset longevity is improved and compliance requirements can be met because preventive maintenance is completed on time. Another benefit is that planners can assign jobs based on the technician’s location.
This is especially helpful at a large operation where it may take a technician 20 or 30 minutes to report back to the maintenance department in order to receive the next assignment.
Most operations stay in a reactive mode and do not see a high level of productivity. Once planning and scheduling is implemented in conjunction with the effective use of technology, your operation can begin to operate in a proactive mode, increasing efficiency, lowering maintenance costs, reducing emergencies, and improving asset reliability, thereby boosting productivity.
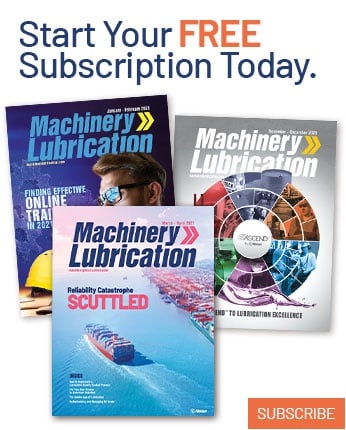