It is sad how quickly a good predictive maintenance program dies, even though the program has gotten a manager promoted, convinced you and others that there is a lot of value in doing PdM to improve maintenance practices, saved money and gained credibility.
The demise of a good program is usually due to the loss of the program champion. He was promoted because he saved tons of money and improved his maintenance practices – just overall improved the company’s bottom line.
With a new department manager, the program fundamentally has started from the beginning. The new leader may not have any experience in the PdM world and cannot identify the need for continuing the process; he just sees costs for new equipment, training, equipment calibration, equipment upgrades, etc.
In today’s world, with such a severe downturn, this is even more prevalent. Cutting costs for everything is the rule – it’s a shortsighted rule, but it’s one that we live by today and will probably live by into the near future.
The new department manager may just see the loss of an electrician or millwright, the people side of things. He has seen plenty of good workers disappear to retirement or leave for another job or get pulled out of the department to work in other parts of the plant.
So, he sees his PdM people as being involved with non-value-added work when they could best be used somewhere else in the department or to satisfy his manpower-sharing commitment.
The new manager also sees his people as being needed to keep the machinery producing, so preventive maintenance work and breakdown work are the priority, especially PM work, which he feels is much more important.
That is due to the fact that PM completion is a measurement management has deemed as important, a key performance indicator which impacts monetary gains for the manager. PdM doesn’t. Therefore, doing PMs makes sense because it affects his bottom line.
One thing we forget is that the manager is human, too, driven by a different set of rules, most we are not aware of and don’t fully understand. We somehow have to come to terms with that reality because it is now our reality as well.
In this environment, the infrared thermographer, vibration analyst and motor testing personnel press on because they all have developed a fan base that knows what their technologies can do and have bought them in to their day-to-day processes – to the point of building PMs for a lot of their equipment using the different PdM technologies.
They know that the information generated is extremely important for them to make informed decisions. So these PMs need to be performed. They add value. So, they always get done to the benefit of the department.
All of the people who rely on the PdM analyst to give them needed data are the new champions of the PdM process. They continue to rely on this information. The analysts know this as well and they continue to perform their duties, though they are somewhat frustrated because it seems to them as if their efforts are not being rewarded.
Then you get moved to the Central PdM Group – heaven. You get to do the work you love all of the time.
May you be successful in your career in your chosen field. I hope you find it very rewarding
Please respond to this blog post with your comments, questions, and stories of predictive maintenance success and failure.
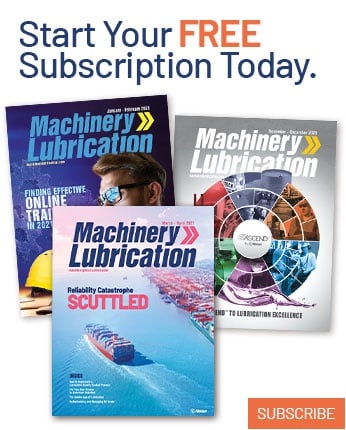