Invented more than 2,000 years ago, threaded fasteners are still the most important detachable hardware used in machinery design and assembly. They can be found on practically any mechanical component, frequently holding together very critical parts.
With more than 300 billion fasteners being consumed in the U.S. every year in assembly applications from automobiles and aircraft to household appliances, it is crucial that these fasteners provide predictable, uniform performance by staying tight once they are installed.
Despite centuries of improvement, threaded fasteners still fail. Fastener failure results from one of two causes. Tension relaxation is frequently caused by temperature changes, and involves the expansion and contraction of bolts and substrate materials, which reduce bolt tension and clamping force in the assembly.
A second cause of fastener failure is self-loosening, which is caused by lateral sliding motion between fastener contact surfaces. While many mechanical methods, such as spring washers, wire retainers and locking bolts, have been developed in an effort to prevent uncontrolled loosening of fasteners, mechanical locking methods add substantial cost to the fastener assembly and cannot prevent the sliding motion that causes self-loosening.
Chemical threadlocking adhesives can inexpensively and permanently prevent threaded fastener failure. Introduced nearly 50 years ago by Loctite Corporation, these single component anaerobic adhesives are unique liquid resins that harden (or cure) to a tough solid when exposed to metal ions in the absence of air.
This anaerobic cure mechanism allows the adhesive to flow and evenly settle to fill the grooves of threaded fasteners without curing prematurely. Any excess threadlocker that overflows the threads during application will remain liquid, and therefore can be easily wiped away.
As a liquid threadlocker cures, it forms polymer chains that find their way into every tiny imperfection in the threads. Thread friction increases with the application of threadlockers as a result of the interfacial connections that key to the surface roughness of the metal.
The adhesive completely fills the microscopic gaps between interfacing threads to positively lock and seal threaded assemblies, preventing lateral movement and protecting the joint from corrosion that can result from moisture, gasses and fluids.
Just a few drops of liquid threadlocker will keep a fastener torqued down in an assembly until the user wants it to come apart. Whereas threadlockers provide 100 percent contact between metal parts, a typical nut and bolt assembly may have as little as 15 percent metal-to-metal contact.
Threadlocking adhesives are highly reliable, low-cost materials that improve torque control, reduce galling and provide lubricity to achieve controlled torque during assembly. Available in different strengths for different applications, threadlockers will hold critical clamp load pressures even in the most severe environments. These adhesives offer high shear strength, good temperature resistance, rapid cure, easy dispensing and good vibration resistance.
Factors to consider when selecting threadlockers
A number of factors must be considered to ensure selecting the right threadlocking adhesive for an application. In certain applications, bolts must be removable and reusable for ongoing equipment maintenance and repair. Contrary to common belief, any bolt that has been locked with threadlocking adhesive may be reused by removing old adhesive before applying new and reassembling.
Threadlockers are available in low-strength formulations for easy removal, medium-strength grades that can be removed using common hand tools, and high-strength formulations that offer the highest holding abilities. However, no threadlockers are permanent; even the highest strength threadlockers can be removed using standard hand tools following direct exposure to temperatures of 450 degrees Fahrenheit.
The strength and viscosity of the adhesive needed for an application are directly related to the size of the fastener used. Low-strength threadlockers are used on screws up to one-quarter-inch in diameter, such as adjustment and calibration screws, meters, gauges and other fasteners that will need ongoing adjustment.
Medium-strength materials are for fasteners up to three-fourths of an inch in diameter used in machine tools and presses, pumps, compressors, and as mounting bolts. High-strength threadlockers are best used on fasteners up to one inch in diameter found in permanent assembly applications such as heavy equipment and a variety of mounts.
Low-viscosity penetrating threadlocking formulations also are available that easily wick into pre-assembled fasteners up to one-half inch in diameter.
The operating conditions of the end-use environment also dictate the threadlocking formulation that should be selected. The newest threadlocking technologies offer many advantages formerly unavailable, including surface insensitive varieties, high-temperature formulations, chemically resistant materials and formulations engineered to withstand extreme vibration.
The type of metal used on the fastener also is critical to the performance of the adhesive. If the fastener is made of two inactive metals such as stainless steel, zinc, magnesium, black oxide, cadmium, anodized aluminum or passivated titanium, a primer may be required to facilitate cure. If only one inactive metal is present, however, no primer will be required.
Applying threadlockers
In applying threadlocking adhesives, the adhesive must wet the total length of the thread engagement area. Proper wetting is dependent on the size of the thread, the viscosity of the adhesive and the geometry of the parts. If the parts are large, then wetting both faces provides the necessary reliability for adequate adhesive application.
For through-hole nut and bolt assemblies, threadlocker should be applied only where the nut and bolt will meet when the assembly is fully tightened, as only adhesive between the threads will cure. For blind-hole assemblies such as cap screws, threadlockers should be applied to both the bolt and the mating threads. If adhesive is applied only to the bolt, air pressure will force the liquid threadlocker to escape as the bolt is torqued down, which will result in incomplete cure and possible assembly failure.
Liquid threadlocking adhesives can be applied with manual, semi-automatic or automatic dispense systems. However, pre-applied fastener coatings are becoming increasingly popular as an alternative to manual or automatic adhesive dispensing methods. Pre-applied coatings feature microcapsules containing adhesive that is pre-applied to an assembly’s threads as a dry film.
When the fastener is assembled, the capsules are crushed, releasing the adhesive threadlocker. In addition to cost and logistical benefits, the use of pre-coated bolts also provides advantages for quality assurance, as the quantity of adhesive dispensed for the coating is very consistent.
Anaerobic threadlockers fixture in minutes at room temperature and fully cure within 24 hours. Full cure of anaerobic adhesives may be achieved more rapidly using short-term exposure to heat (e.g. 30 minutes at 120 degree Celsius). In assemblies where a liquid primer or activator is required to accelerate cure, the primer is applied to one or both fastener surfaces before the adhesive is applied. No mixing of components is required.
As a general rule, anaerobic threadlocking adhesives should not be used on plastic threaded assemblies as substrate softening or stress cracking can occur.
New developments
The greatest challenges faced with traditional anaerobic adhesives have been: 1) promoting cure on a wide range of metallic and non-metallic substrates that may be contaminated with grease or oil, 2) long-term exposure to elevated temperatures greater than 300 degrees F, and 3) long-term exposure to high levels of mechanical stress.
Certain materials, such as oils, can impede or even completely prevent threadlocking adhesives from curing by anaerobic reaction, requiring assemblies to be well cleaned before the adhesive is applied. Also, passive substrates such as zinc dichromate/phosphate plated steel, magnesium, cadmium, stainless steel, aluminum and thermoset plastics could once only be bonded by treating the materials with solvent-based primers before applying anaerobic adhesives.
New surface insensitive threadlocking formulations have been developed to be forgiving of oily and contaminated surfaces, curing in spite of residues that would inhibit cure of traditional threadlocking adhesives. In addition, these threadlockers also are designed to cure more easily on inactive surfaces, reducing applications where primers are needed.
Traditional threadlocking adhesives withstand limited temperatures (minus-65 to plus-300 degrees F) without failure. New anaerobic adhesives that incorporate innovative new proprietary chemical technology have been formulated to maintain their integrity at temperatures up to 400 degrees F. These products are ideal for applications that endure extreme thermal cycling, such as automotive and aerospace assemblies.
While traditional high-strength anaerobic adhesives can withstand some level of vibration, the combination of elevated operating temperatures and strong ongoing vibration typically prove to be too much for conventional anaerobics. New toughened formulations have been engineered to provide better overall performance under extreme thermal and mechanical stress. Because these materials are tougher than traditional anaerobics, they are less impact sensitive and can withstand prolonged exposure to intense vibration, rotational, shear and tensile forces.
A high-performance application
Ryobi Outdoor Products, a leading manufacturer of gas-powered string trimmers for consumer lawn maintenance, was developing a high-powered blower designed to reach speeds up to 210 mph and to run at more than 8,000 rpm. Under these extreme operating conditions, engine components were subjected to temperatures of 500 to 600 degrees F and to high vibrational forces.
Knowing that conventional mechanical solutions would not solve their assembly challenge, design engineers at Ryobi investigated the newest anaerobic threadlockers available. New to the market was Loctite 266, a surface-insensitive, high-strength, high-temperature threadlocker designed to fixture in 40 minutes and fully cure in three hours. Because the adhesive was tolerant of oil and other mild surface contaminants, application was quick and easy, requiring no surface preparation.
On the Ryobi assembly line, the adhesive was applied to zinc dichromated steel bolts that join the muffler to the cylinder head, and the crankcase to the cylinder. Three hours later, each assembly was tested at wide-open throttle for six minutes at 6,000 rpm before it would be approved for customer use.
“The rapid cure of this product has allowed us to perform our engine tests at the end of the assembly line,” says Bill Gest, vice president of new products at Ryobi. “This allowed us to introduce our new blower to market on time, and to ship our products faster and decrease our projected in-process inventories. This new blower unit has helped us maintain our competitive edge in a very competitive market.”
About the author:
Mike Shannahan is the manager of OEM marketing at Loctite Corporation, a Henkel company. Henkel operates worldwide with leading brands and technologies in three business areas: Laundry & Home Care, Cosmetics/Toiletries and Adhesive Technologies. Founded in 1876, Henkel holds globally leading market positions both in the consumer and industrial businesses with well-known brands such as Persil, Schwarzkopf and Loctite. Henkel employs approximately 50,000 people and reported sales of $18.86 billion and adjusted operating profit of $1.84 billion in fiscal 2009. For more information, visit www.loctite.com.
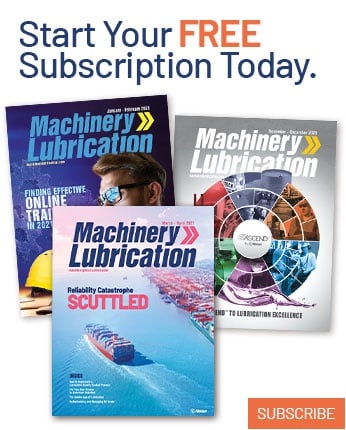