It’s always disappointing, but no longer surprising, to find people who actually believe that once you pay for material and put it on the shelf in the storeroom, it no longer costs anything to keep it there. The fact is, there are significant costs associated with holding spare parts on the books.
Few companies are self-insured, and most pay premiums to their insurance company to the tune of maybe 5 percent or more of the total inventory value. Even fewer are cash-rich, and have to borrow money for major capital improvements and other projects.
While the cost of capital (i.e. interest rate) is relatively low these days, another 5 percent or more is very realistic to borrow funds even in today’s economy. Every dollar invested in inventory represents another dollar that has to be borrowed somewhere else.
Then, of course, there’s the Governor. For states that have an inventory tax, the spare parts inventory is taxed on total value, not on the inventory items that are used in the daily operation. If you own it, it gets taxed.
Taking into account embedded costs like salaries and wages, buildings and utilities to manage the spare parts inventory, the total administrative exposure for carrying cost can add up to as much as 20 percent or more. And that cost is not just a once-and-done expense.
That’s every year, year after year, for as long as you carry storeroom inventory investment as an asset. It becomes clear that if you buy a spare motor for $5,000 to keep in the storeroom inventory “just in case” you need it, that motor will cost you an additional $1,000 each year that you carry the spare motor in inventory.
It doesn’t take long to double the cost of a spare part. Plus, if the motor isn’t under a scheduled preventive maintenance program, there’s a good chance that when the motor is put into service it will not perform as expected or have the life expectancy of a new motor.
The good news is that if you are turning your storeroom inventory on a regular basis, you are more likely to be able to reduce these carrying costs by minimizing the inventory on the shelf. But what if you aren’t using it? Many people say (with conviction), “Don’t get rid of it, just hang onto it. We might need it someday.
Besides, it doesn’t cost anything to hold onto it.” Well, it is clear that isn’t the case. If it costs money to house usable inventory, then it stands to reason that it also costs at least that much to maintain obsolete or unusable parts as well.
In fact, one could argue that it actually costs more to keep obsolete and excess inventory of spare parts in stock, because those items consume valuable storekeeper time and storeroom space to count, move, clean and perform other non-value added activities associated with trying to keep the inventory straight.
Each time a spare part is moved or handled during its time in the storeroom, there is a cost involved. Inventory management practices that do not review inventory regularly to identify obsolete items and target items over the maximum stocking levels also drive up the carrying cost of spare parts inventory.
During inventory reviews parts that have damage from rust, corrosion, and assemblies that have been cannibalized or broken should be removed from the inventory and replacement parts ordered as needed.
It is critical for the storeroom to provide the right part, in the right condition, at the right time and at the right cost to support equipment reliability and production up-time. Creating supplier partnerships and striving to have only spare parts that have been identified as critical to the production process in the storeroom inventory are positive steps to reducing the spare parts inventory investment and inventory carrying cost.
Taking the steps necessary to remove obsolete inventory and reduce inventory exceeding the maximum stocking level are two areas of inventory management that have an immediate effect on reducing carrying cost exposure. Some of these costs are harder to quantify than others.
However, the general concept of inventory carrying costs, as well as the additional costs associated with maintaining obsolete and unusable materials, should be easy enough to rationalize that even the staunchest unbeliever can be convinced to rethink their position.
This article appeared in the April edition of RxToday. For additional information, visit the Life Cycle Engineering Web site at www.LCE.com.
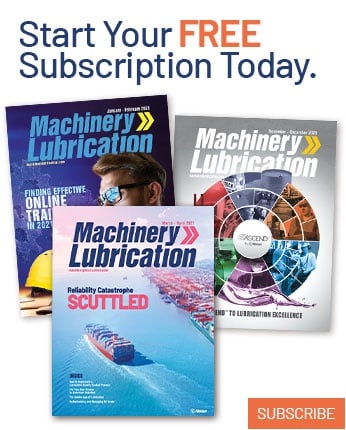