A3 refers to a European paper size that is roughly equivalent to an American 11-inch by 17-inch tabloid-sized paper. The A3 format is used by Toyota as the template for three different types of reports:
- Proposals
- Status
- Problem solving
There is no “magic” in the steps through which the structured A3 Problem Solving template takes a team. These steps are basically:
- Identify the problem or need
- Understand the current situation/state
- Develop the goal statement – develop the target state
- Perform root cause analysis
- Brainstorm/determine countermeasures
- Create a countermeasures implementation plan
- Check results – confirm the effect
- Update standard work
These steps follow the Deming Plant-Do-Check-Act (PDCA) cycle, with steps 1 through 5 being the ”Plan”, Step 6 being the “Do”, Step 7 being the “Check” and Step 8 being the “Act”.
On the A3 template, the steps are typically laid out like this:
Surprisingly, the steps and the format look very much like templates created by U.S. companies in the 1980s and 1990s.
Ford Motor Company created an 8.5-inch by 11-inch 8D Problem Solving template:
Johnson Controls Inc. created a Problem Solving Document (PSD) that uses both sides of a form that folds to an 8.5-inch by 11-inch size, but it is larger than tabloid size unfolded.
If U.S. companies had the templates and knowledge of the problem-solving tools, why aren’t U.S. companies better problem-solvers?
The answer is that when most organizations start their lean implementation, they jump to using the lean tools. However, there are four components of a lean implementation: lean planning, lean concepts, Lean tools and lean culture. All four of these components must be implemented in parallel. The lean tools are ineffective without the support of a developing lean culture.
The Four Components of Lean
This supporting lean culture is highlighted by how Toyota views problems:
- Problems are seen as opportunities to improve their processes and, ultimately, their products.
- The people assigned to solve the problem view the assignment as an opportunity to improve their problem-solving skills. They understand that they learn more and become a better problem-solver each time they perform the process.
In Toyota, no problem is a problem!
Compare this to how a typical U.S. company associate views problem-solving. We view it as a burden or maybe even a punishment. We get through it so we can check it off our to-do list.
A3 is a structured and very useful problem-solving template. To be successful, this template must be supported by a lean culture that changes how we view problems. Otherwise, A3 Problem Solving will just join the list of “programs of the month”.
Read more on lean manufacturing best practices:
Eight Easy Steps to Creating a Pareto Chart
How to Reduce Manufacturing Waste
Kaizen Events: When and How to Use Them
About the author:
Larry Rubrich is the president of WCM Associates LLC. For more information, visit www.wcmfg.com or call 260-637-8064.
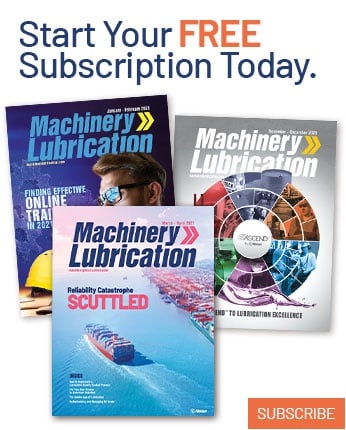