The manufacturing productivity gap among North American automotive manufacturers is smaller than ever as quality advances are driving productivity improvements and all manufacturers get more from their workforce and capital investments, according to The Harbour Report North America 2006, the annual study released June 1 by Harbour Consulting.
The difference between the most and least productive in terms of total (assembly, stamping and powertrain) labor hours was 7.33 hours per vehicle in 2005, down from 9.08 in 2004 and less than half the 16.56 HPV gap in 1998.
DaimlerChrysler’s Chrysler Group continues to show the fastest rate of productivity improvement, doing 6 percent better in 2005 across assembly, stamping and powertrain measures. Since 1997, Chrysler Group has improved its assembly labor hours per vehicle by 31.7 percent to 23.73 HPV. In that same period, General Motors has also improved its total manufacturing hours per vehicle by a comparable
31.3 percent to 33.19 HPV.
“Nissan’s labor productivity lead equates to a $300 to $450 per vehicle cost advantage relative to less productive manufacturers,” said
is noteworthy and a testament to the Global Manufacturing System and Ford Production System.”
In overall productivity, four of the six companies with assembly, stamping and powertrain operations in
Nissan Motor Company led the industry, at 28.46 hours per vehicle, across assembly, stamping and powertrain, followed by Toyota Motor Corp. at 29.40 and Honda at 32.51 HPV. But General Motors was close behind at 33.19, followed by Chrysler Group at 33.71 and Ford Motor Co. at 35.82 HPV.
Among assembly plants, Ford’s
2008.
“Ford Atlanta historically has had one of the best workforces of any assembly plant in the industry and the data proves that,” Harbour said. “The decision to close the plant had nothing to do with the dedication of the people, from whom Ford has cultivated many competitive practices over the years.”
“Nissan’s performance reflects the hard work at
The Habour Report, the auto industry authority on manufacturing efficiency since first published in 1989, measures assembly, stamping and powertrain productivity performances – plant by plant, and company by company – for North American automotive manufacturers. The labor hours per vehicle measure calculates the total salary and hourly labor content required to produce one vehicle.
This year’s Harbour Report provides an even broader assessment of factories, adding
While the six major manufacturers are closer than ever on labor productivity, there remains larger gaps on several other manufacturing attributes, including capacity utilization.
DaimlerChrysler, Ford and General Motors still have a wider variation in capacity utilization among their assembly plants, while they continue to work on plant flexibility. By closing plants in the next two years, Ford and General Motors will see improvement on capacity utilization. Others, such as Toyota, which had its assembly plants running between 97 percent and 109 percent of capacity, are integrating their design, engineering and manufacturing organizations to increase flexibility and use common parts and processes.
The other differentiator is profitability. Nissan, Toyota and Honda each earned a pre-tax margin of more than $1,200 on every vehicle they sold in North America. Chrysler Group earned $223, while Ford lost $590 and General Motors, $2,496, on each vehicle sold in 2005.
This reflects a variety of factors, including the large difference in health care and pension costs, lower average revenue, as well as higher costs of rebates and low-interest rate financing required to trim inventories.
Other highlights from this year’s assembly, stamping and powertrain chapters include:
ASSEMBLY
All but four of Chrysler’s assembly plants improved their HPV from 2004. Five plants registered gains of more than 5 percent – Brampton, Ont.; Jefferson North; Toledo South, Toluca, Mex., and Windsor.
General Motors had five of the 10 most productive assembly plants: Oshawa #2 (16.08 HPV for Pontiac Grand Prix, Buick Lacrosse and Allure); Fairfax, Kan, (17.62 HPV for Chevrolet Malibu and Malibu Maxx); Lansing M (17.82 HPV), which closed in 2005 after building out the Pontiac Grand Am and Chevrolet Malibu Classic; Oshawa #1 (17.91 HPV for Chevrolet Impala and Monte Carlo) and
Spring Hill, Tenn. (18.34 HPV for Saturn ION). GM plans to idle Spring Hill car production at the end of 2006 and idle Oshawa #2 when it builds out the current models in 2008.
General Motors also led in six of the 15 vehicle segment ratings: sub-compact car (Saturn ION/Spring Hill), compact car (Chevrolet Malibu/Fairfax), luxury car (Cadillac CTS/Lansing Grand River), small crossover (Chevrolet HHR/Ramos Arizpe), full-size SUV (Chevrolet Silverado, GMC Sierra/ Fort Wayne) and large van (Chevrolet Express, GMC Savana/Wentzville).
Nissan had three assembly lines in the top 10: the Altima lines in Smyrna, Tenn. (16.90 HPV), and Canton, Miss. (17.73 HPV), and the Frontier pickup truck line in Smyrna (18.17 HPV). Nissan also led with the most productive assembly performance in four of eight vehicle segments in which they compete: large car (Maxima), full-size SUV (Armada), mid-size SUV (Pathfinder) and small pickup
(Frontier).
Toyota’s Georgetown #2 plant, which produces the Camry and Solara, ranked eighth at 18.08 HPV. Overall, Toyota’s assembly performance was flat year-over-year, excluding the two lines at Princeton, Ind. When Princeton is included, Toyota’s hours per vehicle degraded by 9.6 percent. Nonetheless, Toyota’s North American production volume is growing so fast it needs the equivalent of one new
assembly plant of capacity each year to meet demand.
STAMPING
Toyota again led in stamping labor productivity, although its 1.42 stamping hours per vehicle degraded 3.6 percent from 2004. Toyota regained the lead in press productivity with a record 792 average parts per hour.
Harbour uses a stamping index that weighs each of several measures in a process that creates a composite score of stamping productivity. On that basis, Toyota’s Cambridge stamping shop ranked first, followed by Toyota Georgetown, Honda East Liberty, Honda Marysville and Toyota Princeton. Of the 10 best stamping plants, Toyota had three; Honda, two; DaimlerChrysler, Ford, General Motors,
Nissan and NUMMI, one each.
In total stamping labor productivity, Nissan ranked third, behind CAMI, with 2.11 HPV. Chrysler Group was fifth (behind NUMMI), improving 6.7 percent to 2.64 HPV.
“As in assembly, Toyota is among the best in the industry,” said Harbour. “It is not a matter of spending more than competitors. It reflects regular kaizen improvement activities and the flexibility that comes with well coordinated engineering and manufacturing.”
Ford has also shown a renewed commitment to upgrade its stamping technology after several years of limited investment, and its performance is showing a steady climb despite aging equipment.
GM, Chrysler and Ford all have placed greater emphasis on metal stamping in recent years. Each has a specific strategy to maximize output from fewer presses that run more parts at higher rates and better quality. Their discrete performances, in total, still lag that of Nissan, Toyota and Honda.
POWERTRAIN
Five of six participants improved engine productivity when comparing plants that were included in last year’s report. Toyota still led the field at 2.90 HPE. Honda finished a close second at 3.27 HPE while GM was third at 3.60 HPE.
Toyota’s four-cylinder engine lines at Buffalo, W.Va., and Georgetown finished 1-2 in the individual plant rankings. Nissan’s Decherd, Tenn., and General Motors’ Spring Hill engine plants ranked third and fourth, GM had three engine plants in the top 10.
“Toyota remains the benchmark in engine productivity,” said Michelle Hill, director of North American benchmarking for Harbour Consulting. “Toyota’s four-cylinder line in Buffalo, W.Va., was again the report’s most productive engine operation for the fifth consecutive year at 1.82 hours per engine. It’s only the third time The Harbour Report has had an engine plant with an HPE measure below 2, and both times it was Toyota West Virginia.”
Aided by significantly higher volume, Nissan’s Decherd engine plant showed outstanding results and improvement from 2004 across its four-, six- and eight-cylinder lines.
Chrysler widened the lead it assumed last year over GM and Ford in transmission productivity, improving to 3.55 HPT from 3.86, while Ford came in at 3.80 and GM at 3.86 HPT. For the second straight year, Chrysler’s Kokomo, Ind., led all plants producing rear-wheel drive transmissions (42RLE) and was the No. 1 plant overall, beating GM Toledo. Chrysler Kokomo also had the best productivity measure among producers of front-wheel-drive transmissions (A604 line) at 3.47 HPT.
OVERALL
More than just year-over-year performance, The Harbour Report looks at several years of results to determine which companies are developing systems and processes related to quality, lean manufacturing, continuous improvement, worker involvement, technology, level of product complexity, process design and layout.
“Since our company started 26 years ago, we look at how companies are managing their resources,” Harbour said. “Lean manufacturing and continuous improvement efforts do not always produce immediate improvements, nor are they immediately recognizable. But as shown in The Harbour Report 2006 results, companies that are producing consistent, sustainable improvements to their manufacturing operations are providing automakers with a cost advantage over their rivals.”
More information and performance results can be found in The Harbour Report North America 2006, the annual study created and published by Harbour Consulting, a Troy, Mich.-based manufacturing and management consulting and automotive research firm. Harbour Consulting completed its first study of automobile manufacturing in 1981. Today, The Harbour Report is considered the authoritative guide to automotive manufacturing in North America, and is a leading competitive analysis tool used by OEMs and suppliers to benchmark performance, develop strategies and improve operations. Copies of The Harbour Report North America 2006 can be ordered through the company’s Web site at http://www.harbourinc.com, or by calling 248-649-4490 or toll-free at 800-208-1353. The report is $595 and payment by credit card is accepted. More information about the report and Harbour Consulting is available on the company’s Web site.
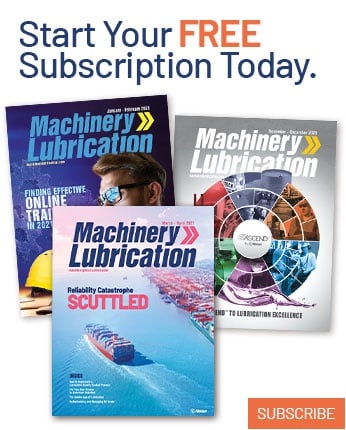