The manufacturing industry is changing – it’s becoming more advanced as new digital tools promise improved productivity and profits. However, labor remains a key resource. Many companies are experiencing skilled labor shortages due to an aging and retiring workforce, competition for labor, and the new digital native demographic of younger workers.
As manufacturing processes become more digital, we will need to retrain our existing workforce while recruiting and training our future workforce. We will need to rethink training and workforce development, making them exciting, up-to-date, and engaging.
Those that innovate will stand above those that don’t.
Evaluating Teaching Methods
Every student learns differently; some are visual learners, some are better at remembering information they read independently, but most learn best when participating in hands-on educational activities. Despite this, historically, workforce development has centered on classroom training where an instructor presents the information and provides reading materials, such as manuals, for independent study.
In this environment, the workforce is being told what best practices are, instead of shown. This makes it difficult for information to be absorbed, which creates a large disconnect between the learning and the application of information.
To solve this gap, on-the-job training will become paramount. With the arrival and adoption of digital technologies, such as augmented reality (AR), we are now able to extend workforce development into the field, allowing the information to be truly absorbed and applied. From documentation to instructions and how-to support, the modern factory work environment will become digital.
The Global Labor Shortage Problem
There are several challenges currently impacting the industrial labor market. To start, demographic shifts and aging populations are creating an ongoing shortage of qualified workers. According to the World Bank, over the next decade, the number of people of working age will decline in the United States by over 3%. Employers will need to find new ways to attract and retain highly skilled workers, with 83% of manufacturers surveyed stating this as their top challenge.
These trends are coupled with increasingly complex products and processes. In other words, workers will need more new skills than required in previous decades. This problem creates productivity deficits. Almost half of the frontline workers say the skills gap negatively impacts their productivity.
Developing New Skills
In the manufacturing environment, no matter our role, we have multiple skill sets that we are required to continually develop and maintain.
Augmented reality enhances workforce development by providing employees with interactive and immersive learning experiences. AR also provides real-time feedback and guidance on job performance, as well as immediate access to resources, such as manuals and tutorials. Additionally, AR helps reduce training costs by allowing employees to learn at their own pace in a virtual environment.
Augmented Reality
Advanced computer-generated simulations that enhance the user's environment in real-time.Source: Reliable Plant
In its full implementation, AR provides users with the ability to perceive and use digital data on top of their physical environments. The data can include pointers to the physical space where an activity needs to be performed, and with a built-in camera, video analytics can determine when the task is completed.
On the simpler end of the scale is remote assistance, where the worker is connected to a remote expert in a video chat environment with annotations from the expert being displayed over the physical environment. This also provides the opportunity for the worker to train and practice using augmented reality in a classroom or lab environment before they ever enter the field. This increases worker confidence and reduces the likelihood of human error.
Deploying Augmented Reality in the Facility
Building the Business Case
AR helps upskill workers by replacing traditional training and guidance materials with a more effective, immersive experience. The first step is prioritizing the business case for AR in the workplace.
For example, it’s not uncommon for unplanned downtime to be partially attributed to operator error. Recovering from these errors can be expedited by deploying the remote expert function of AR technology. With this feature, a remote expert virtually collaborates with the operator, assisting in getting the production equipment back online while simultaneously training the operator on how to avoid making the same mistake in the future.
The remote expert functionality reduces the need for experts to physically be present at the facility, which not only speeds up the resolution time, but allows the experts to service more workers in a shorter period of time. The remote expert feature is often the first use case for AR technology adoption, as it is simple to implement and promotes remote collaboration.
Did You Know?
Applying the augmented reality in industrial settings can improve new hire productivity by 40% and reduce training costs by 50%.Source: PTC
Creating Digital Work Instructions
The next step in a typical AR workforce development journey is digital work instructions, which can be used to create updated and improved training materials that more accurately reflect the day-to-day operations and requirements of workers.
Digital work instructions are developed in three steps:
- Capturing the workflow and worker knowledge.
- Editing a sequence of steps that include safety and work measures.
- Deploying the work instruction set for use by all team members.
Experienced workers are great resources to capture workflow and knowledge. By applying digital devices while they perform the necessary work, team members can not only describe each step in real-time, but they can take pictures and videos which can be used as supplemental materials when building the new training documents.
When editing the sequence digital work instructions, additional documentation and steps can be included, such as safety measurements that should be top-of-mind both before and after each step. This allows for a more in-depth look at every aspect that should be taken into account during the completion of a work order.
A work procedure management system is typically used to store, maintain and deploy the digital work sequences to the devices used in the field by team members. It also allows for work progress to be tracked in real time. When the work sequences include images, voice narration, videos, and even three-dimensional drawings, they also serve as training material to be reviewed in preparation for performing the task.
Adding Augmented Reality Overlays
The third step is deploying the AR technology, which will allow the captured information, images and videos to be overlayed onto the worker’s physical environment. These materials can provide real-time information, such as that stored in the control system. The images can also be used for spatial orientation, which can indicate in their physical space where a step should be performed.
This ability to annotate a physical space enhances the ability of both senior and junior workers to complete steps accurately and efficiently by providing on-demand information at the right time where the worker is physically located in that moment. This technology also allows for video inspections to take place, which can automate quality checks after each step is performed, which can catch missteps as they happen and reduce the likelihood of human error.
The Benefits of Augmented Reality
Augmented reality technology with digital work instructions addresses several goals of manufacturing workforce development.
Benefit #1
AR reduces the skills gaps by deploying guided remote assistance that helps reduce the human error element and provides real-time training for an enhanced learning experience.
Benefit #2
Implementing AR digital work instructions that include photos and videos builds a library of knowledge that can be actively updated and maintained. This library will develop into the single source of truth for the manufacturing workforce, which streamlines the training process and ensures all team members can be upskilled, trained and retained.
Benefit #3
Instructions and information are presented in a technology-rich, highly visual format that supports the evolving nature of a worker’s job, allowing them to learn and retain the information more effectively and permanently than traditional classroom methods.
Benefit #4
A digital work environment attracts a new generation of workers while actively improving the safety, efficiency and accuracy of the work performed on the plant floor.
Benefit #5
When compared to conventional classroom training sessions, AR effectively reduces both the time and cost needed to train team members.
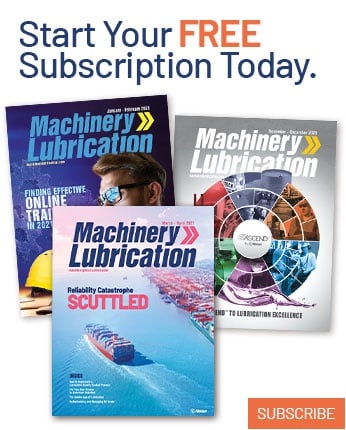