In the Toyota Way by Jeffrey Liker (2004), the book’s author identifies 14 management principles that make Toyota the world’s greatest manufacturer. One of these 14 principles is “Become a Learning Organization.” Many have tried to become learning organizations, but, according to Liker, no one has succeeded like Toyota. Toyota’s learning organization has three key elements according to Liker; I will touch on each of them:
-
Identify root causes and develop countermeasures. Toyota identifies root causes primarily using a very simple method called the “five why’s.” This simply entails asking the question “why?” as many times as possible to determine the root cause of a problem:
Figure A (Source: Peter R. Scholtes, The Leader’s Handbook, McGraw-Hill, 1998)
Level of Problem |
Corresponding Level of Countermeasure |
There is a puddle of oil on the shop floor. |
Clean up the oil. |
Because the machine is leaking oil. |
Fix the machine. |
Because the gasket has deteriorated. |
Replace the gasket. |
Because we bought gaskets made of inferior material. |
Change gasket specifications. |
Because we got a good deal (price) on those gaskets. |
Change purchasing policies. |
Because the purchasing agent gets evaluated on short-term cost savings. |
Change the evaluation policy for purchasing agents. |
-
Use hansei: Responsibility, self-reflection, and organizational learning. In a nutshell, this concept is about reflecting on mistakes/weaknesses and devising ways to improve. Hanseiis a concept that Toyota uses as a practical improvement tool like kaizen. Toyota actually conducts hansei events (like kaizen events) to improve products and processes. As hansei is utilized, the improvements are fed back into the organization and disseminated.
-
Utilize policy deployment (hoshin kanri).This is Toyota’s process of cascading objectives from the top of the company down to the work group level. Aggressive goals start at the top level and each level develops objectives to support these goals. Many systems like this are being used at companies across the United States, but often they are failures because the objectives rarely support important company goals; they usually are put in place to ensure that an individual gets his/her incentive! At Toyota, objectives are always measurable and concrete, and they always support executive-level/company goals. The process as it permeates the organization follows the simple PDCA (Plan-Do-Check-Act) process. This ensures that the success is being measured and monitored on a regular basis.
The last point that Liker makes regarding Toyota’s learning organization is the number of years it has taken for Toyota to achieve its success. For example, it took Toyota more than a decade to build an organization that even comes close to the learning organization it has in Japan. Toyota succeeds as a learning organization ultimately because it has relentlessly pursued success rather than pursued several “flavors of the month” over years with little results.
About the author:
Darren Dolcemascolo is an internationally recognized lecturer, author and consultant. As senior partner and co-founder of EMS Consulting Group, he specializes in productivity and quality improvement through lean manufacturing. Dolcemascolo has written the book Improving the Extended Value Stream: Lean for the Entire Supply Chain, published by Productivity Press in 2006. He has also been published in several manufacturing publications and has spoken at such venues as the Lean Management Solutions Conference, Outsourcing World Summit, Biophex, APICS and ASQ. He has a bachelor of science degree in industrial engineering from Columbia University and an MBA with graduate honors from San Diego State University. To learn more, visit www.emsstrategies.com or call 866-559-5598.
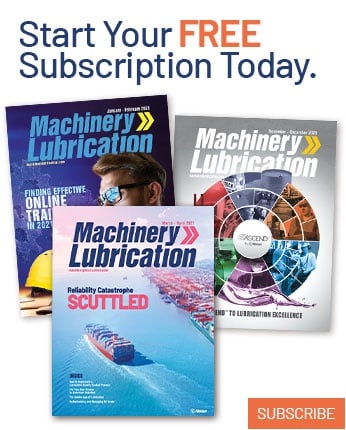