The potential-to-functional failure interval (P-F interval) is one of the most important concepts when it comes to performing Reliability-Centered Maintenance (RCM).
Remarkably, the P-F interval is also one of the most misunderstood RCM concepts. The failure mode analysis becomes even more complicated when you are dealing with several P-F intervals for one failure mode.
This article will help clarify the P-F interval and the decision-making process when dealing with multiple P-F intervals.
A functional failure is the point where an asset fails to perform a required function. The failure can be a complete or partial failure of any primary or secondary asset function. An example of a complete failure is a bearing seizing in a fan motor and causing the fan to stop.
An example of a partial failure is a worn impeller in a pump that still pumps fluid but not to the required level. Either a complete or partial failure will have an operational impact and will need to be corrected.
In some cases, when safety is a concern, the functional failure may not be the actual failure point but a predetermined point that should not be exceeded due to the risk involved.
An example of this would be a preset temperature in a car engine. This temperature is lower than the point where the engine would sustain critical damage.
The actual failure would be the loss of the engine, but the catastrophic nature of that failure requires an identification prior to the point of shutdown. This becomes the functional failure of the engine.
A detectable symptom or warning sign that a functional failure is in the process of occurring is a potential failure. Functional failures can have many different potential failure symptoms prior to the actual functional failure.
These potential failure symptoms can occur at different times and are detectable by different methods. Some of the symptoms include heat, vibration, smell and cracking. An example of a potential failure is the increased temperature in a bearing prior to seizing.
Another example would be the smell of burnt electronics prior to a resistor or capacitor burning up. The importance of the potential failure characteristic in RCM is to use an inspection to detect the potential failure before the functional failure occurs.
Figure 1. A graphical representation of a P-F interval.
Senses and Sensing
The method of potential failure detection is dependent on the symptom and the methods available. There are two different groups of methods for identifying potential failures - human abilities and predictive maintenance technologies.
Our ability to detect failures using our own senses has become somewhat forgotten in industry with all of the technologies available and the decrease in the skilled workforce. Human senses are very powerful, low-cost tools in an experienced maintenance professional's tool kit.
In many cases, we can still find the symptoms far enough in advance to correct the impending failure even though a predictive technology can detect the failure sooner. So, don't forget the valuable tools you possess.
The second method for potential failure detection is predictive technology. Some of the more popular predictive technologies are thermography, vibration analysis, oil analysis and ultrasound.
Predictive technologies also include testing and diagnostic equipment used either internal or external to the system that helps identify potential failure conditions. Predictive technologies can often detect potential failures much further out than human abilities, but they carry a much higher price.
You have to pay for the technologies AND the technicians who use them. Many companies have adopted the use of internal sensing equipment to lower the overall cost of using predictive technologies. However, these technologies still require experienced professionals to analyze the results.
Timing is Everything
The P-F interval is the time or cycles between the initial detection of the potential failure condition and the time of the actual functional failure. Most failures don't take the same amount of time to fail after the symptom is detected, so the P-F interval is expressed as an average amount of time or cycles.
The P-F is critical in designing the right maintenance task to prevent functional failures. A general example would be to set the task interval for inspection at half of the P-F interval.
The mean time between failure (MTBF) related to the failure is not important when designing the maintenance task because it gives no reference to time of a symptom to the failure. A graphical representation of the P-F interval is displayed in Figure 1.
The vertical axis is the functional capability of the asset and the horizontal axis is the operating age or number of cycles. As the life of the asset goes along, it will come to a point where the symptom appears. This is the potential failure. After the symptom appears, there will be a period until the functional failure occurs. This period is the P-F interval.
Multiple Symptoms
Failure modes that have multiple symptoms of the impending failure offer a great deal of flexibility in the choice of tasks to perform for detecting the impending failure. Each of these potential failure conditions has a different P-F interval, and it is important to not treat them as equals in the analysis.
Every symptom will arise at different times in relation to the functional failure. An example of this would be a bearing failure. The first symptom may be unusual vibration detectable by vibration analysis around six months.
The second symptom may be sound detectable at three months using airborne ultrasound. The third symptom may be increased heat detectable at one month prior to the bearing failing.
Treating these symptoms as similar P-F intervals and inspection methods can lead to extensive downtime due to the use of the wrong tool at the wrong time. A graphical representation of multiple P-F intervals is displayed in Figure 2.
Figure 2. A graphical representation of multiple P-F intervals.
The probability of detection is the probability of detecting a potential failure condition in one inspection if it exists at the time of inspection. The probability of detection when using any inspection technique will vary depending on certain factors.
First, there is the location of the failure and how accessible it is to the professional performing the task. Complex pieces of equipment or small, confined areas create difficulties in performing tasks. Second, there is the complexity of the task and the skill level of the professional conducting the task.
When determining the task to perform, consider the skill level of the professional that will be normally performing the task. This will help determine the probability of detection.
Finally, if there is a technology used to perform a task, it could have limitations that need to be taken into account. The bottom line is that the lower the probability of detection, the more often you have to inspect to increase your chances of detecting the potential failure.
Failure Monitoring
Failure monitoring is the act of continued inspections at an increased level and focus after a potential failure is detected. This allows you to get maximum life out of the asset while still keeping the risk to a minimum.
The possibility of monitoring can only be effective if the P-F interval is very predictable and long enough to allow time for monitoring the symptom. In many cases, the monitoring task is a shorter interval than the original task because of the fact that a potential failure condition exists.
Also, remember that it is best not to perform monitoring if the functional failure has safety or environmental consequences.
The mean time to repair (MTTR) is the average time it takes to repair a failure condition. Consider this when looking at the task interval. The MTTR can vary depending on the type of failure - potential or functional.
MTTR for the functional failure is used for determining the P-F interval adjustment. In some cases, the MTTR can be very extensive due to repair complexity, lead-time on parts or availability of skilled service people.
In cases where the MTTR is a significant length of time, that amount of time is taken off the P-F interval to increase the task interval, providing a greater possibility of correcting the problem prior to the functional failure.
Making the Right Call
Choosing tasks for a specific interval is dependent on several factors. It can be a simple decision process or done with a cost benefit analysis. However, for the purpose of simplicity, I will point out the factors involved in choosing the right task and a simplified decision-making process.
The first factors to identify are what tasks can be used to find potential failures and how often the tasks have to be performed. Second, you must identify the resources available to perform the tasks and the possibilities of attaining other resources.
Rule out the tasks that will not be options and choose the task or tasks from the remaining options available based on the acceptable impact of the task on safety and operations. A cost benefit analysis is a powerful tool to perform the selection process, but it is not always necessary.
Summary
This article has clarified the use of the P-F interval in RCM and the factors that affect the use of the interval. It has also explained how to make decisions when using multiple P-F intervals.
The P-F interval is a valuable piece of information for any maintenance team, and you don't need special education to use it. The use of P-F intervals in determining the right maintenance to perform at the right time need not be confined to RCM. Its use benefits any maintenance program.
Robert Apelgren is a senior reliability analyst for General Dynamics. He received a bachelor of science degree in industrial technology from Roger Williams University and an MBA from the University of Phoenix. Apelgren is a Certified Maintenance and Reliability Professional (CMRP) and a member of the Society for Maintenance and Reliability Professionals’ Best Practices and Standards committees. He can be contacted via e-mail at robert.apelgren@gdit.com.
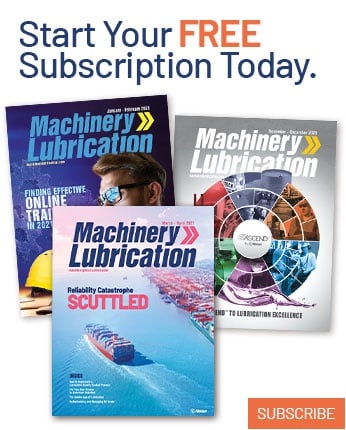