Experience tells us that when electric motors fail and must be rebuilt, possible non-bearing causes abound. These can include winding, wiring, grease or seal failures, which, in turn, may result in bearing failures (although bearings are not the root cause). Improper motor use and inadequate maintenance can add to potential problems and premature bearing failure. But, proper installation and maintenance of bearings can help extend service life in electric motors for years.
The “perfect” operating environment is contaminant-free and has low humidity, low non-fluctuating temperature, good alignment and no vibration. Loads are perfectly balanced. Theoretically, bearings could last indefinitely in a perfect world.
In reality, however, you can only strive to create the best possible operating environment. In advancing the goal of motors free of premature bearing failure, follow some basic guidelines.
1) Manage MoistureAlthough it’s not always possible to control moisture, it is manageable. When motors are running, humidity usually is not harmful; but when they are turned off and cool, condensation builds up. Condensation can’t be stopped, but you can guard against the harmful effects by using grease fortified with rust inhibitors in bearing assemblies and frequently rotating the shafts of idle motors whenever condensation is suspected. Good seals also can help keep humidity from invading the cavity. Avoiding direct water spray on seals during washdowns is also important.
2) Align the ShaftsMisalignment between an electric motor shaft and the shaft of the driven equipment represents a common root cause of premature bearing failure. Such misalignment introduces excessive vibration and internal bearing loads and will shorten the working life of an electric motor.
While couplings typically are flexible to accommodate misalignment, their flexibility shouldn’t be taken for granted. For ideal shaft alignment, you should first secure the driven equipment and then install the coupling. Only after the coupling is attached to the equipment should you move the motor into proper alignment and secure it.
3) Chart VibrationAfter a new motor is installed, take a vibration reading as a benchmark and regularly schedule readings. When a laboratory technician charts a recurring spike in vibration data (measuring amplitude at a given frequency on the inner ring ball pass) but lacks historical reference points, no clear picture will emerge confirming the data represents an actual problem. Vibration characteristics vary widely among motors and applications. Data documenting a “snapshot in time” will have little real-condition value.
4) Optimize LubricationProper bearing lubrication encompasses the proper quantity, replenishment interval, type and application method.
-
Quantity: A new electric motor should arrive with its bearings properly lubricated for the dimensions of the bearing envelope. Avoid overlubrication. Adding more lubricant than specified by a manufacturer can result in increased friction and temperature and reduced grease life, potentially harming a bearing and adversely affecting motor performance. Rolling elements require more energy to rotate if there is too much grease. This places a greater burden on the motor. Overlubrication also can cause undesirable heat buildup as the rolling elements attempt to push the extra grease out of the way. Heat buildup leads to friction, wear and reduced grease life.
-
Replenishment interval: While there is no general rule of thumb governing correct lubrication intervals, base practical intervals on bearing size, type, speed of operation, general operating environment and the type of electric motor (vertical motors require lubrication twice as often as horizontals). Some motors may come with non-relubricatable bearings (i.e., having seals or shields).
-
Type: Before lubricating a bearing, ascertain the grease currently in use and select either the same type of grease or a compatible product (compatibility charts are available from lubricant manufacturers). Always consult the manufacturer’s recommendation and beware that not all greases are compatible. For example, many deep-groove ball bearings arrive lubricated with urea-based grease (a high-temperature, all-purpose lubricant). Some of these lubricants, though, become sensitive to other lubricants, particularly lithium-based greases, which can cause the lubricants to drain out of the bearing cavity.
-
Application method: Most large electric motors come equipped with a grease fitting and drain plug (smaller motors may not have these ports because they use smaller bearings that are factory-lubricated for the life of the motor). A traditional lubrication method is to pump new grease into the bearing through the appropriate fitting and allow the old grease to exit through the drain plug. Newer technologies, including circulating oil and mist, have been developed to advance the lubrication process and offer key advantages in certain operational settings.
Rebuilding an electric motor will involve removal of old bearings and installation of new ones. For best results:
-
Use a puller to remove old bearings and avoid damage to the motor shaft.
-
Use hydraulic-assisted removal techniques if very large bearings must repeatedly be removed. (Hydraulic fluid is forced into a small, pre-drilled hole in the center of the shaft. The fluid expands the inner ring of the bearing and allows it to be removed).
-
Match new to old. If the original bearings can’t be matched (or if the bearings aren’t originals and are inadequate substitutes), turn to a reputable bearing manufacturer or distributor for a replacement solution as there are differences in designs and operating characteristics.
-
Decide between seals and shields for bearing protection. Seals can offer ideal protection from contaminant-laden operating environments because they make positive contact with the rotating inner ring of the bearing. Shields may be more practical for most motors because they extend close to the inner ring but do not make direct contact, thus avoiding friction. Consultation with the manufacturer can support decision-making. Always replace a sealed or shielded bearing with one of similar protection.
Daniel R. Snyder, P.E., is the director of applications engineering for SKF Industrial Division, SKF USA Inc. For more information, call 215-513-4680 or e-mail daniel.r.snyder@skf.com.
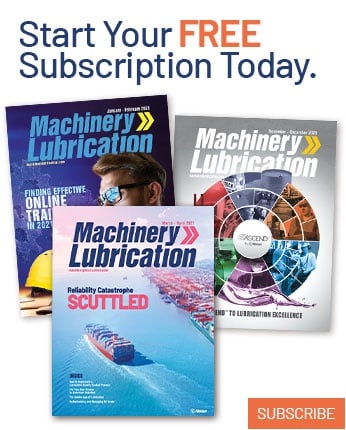