Pneumatic vibration equipment is an engineered solution that must be installed and operated properly (according to the manufacturer’s instructions) in order to obtain maximum benefits. To that end, VIBCO shares some “lessons learned” regarding the installation and operation of pneumatic vibration equipment.
Its top five pneumatic vibration equipment lessons learned include:
- Correct installation and mounting is critical to performance.
- The condition, size and configuration of your air line is important.
- Correct air pressure (PSI) and air flow (CFM) are essential.
- Periodic checks for loose mounting fixtures can extend the life of your pneumatic vibration equipment.
- If your unit requires lubrication (piston and ball style), make sure that your lubricator is functioning correctly and is no more than 5 feet away from the unit.
The best way to ensure that you receive the maximum benefits and life from pneumatic vibration equipment is to follow the manufacturer’s installation and operation instructions.
(VIBCO instruction manuals are online for your convenience.)
1. Correct installation and mounting is critical to performance.
Make sure to follow all of the mounting and installation steps exactly as they are provided in the manual. One of the ways you can ensure a good mount is to select the correct mounting plate and channel for your bin. The following charts are good “rule of thumb” guides:
2. The condition, size and configuration of your air line is important.
Kinks, holes and leaks in your air line can easily degrade the performance of your pneumatic vibration equipment, causing it to run and then stop unexpectedly. Pneumatic equipment performance can also be degraded if your air line is split between units (“T” junction) or used to run multiple pneumatic units. Best practice is to run separate, correctly sized lines for each unit in operation, and to perform periodic checks for kinks, leaks and holes.
3. Correct air pressure (PSI) and air flow (CFM) are essential.
Make sure that you are providing your pneumatic unit(s) with correct PSI and CFM. Pneumatic units should have the recommended PSI and CFM indicated on the housing or on the shipping box. A general rule of thumb is that PSI should be 40 to 80, and you should consult your manual for proper CFM. Insufficient or too high of air pressure flow can cause unit failures.
(Click here for a handy Air Flow Pressure calculator.)
4. Periodic checks for loose mounting fixtures can extend the life of your pneumatic vibration equipment.
Most pneumatic vibration equipment is virtually maintenance-free. You can increase the life of your equipment by performing periodic checks of the mounting assembly and hardware. Check to ensure that all mounting bolts are tight and hardware is securely welded to the bin.
5. If your unit requires lubrication (piston and ball style), make sure that your lubricator is functioning correctly and is no more than 5 feet away from the vibration unit.
Too much distance between the lubricator and vibration equipment can cause too little or no lubrication to reach the unit. Your lubricator should be no more than 5 feet away from the unit. For best results, you should use using air tool oil. You may also use SAE 10 or lighter machine tool oil, Marvel Mystery oil or automatic transmission oil.
About the author:
VIBCO is a manufacturer and supplier of pneumatic vibration equipment. You may contact the company’s technical support staff 24 hours per day, seven days per week at 800-633-0032. For more information, visit www.vibco.com.
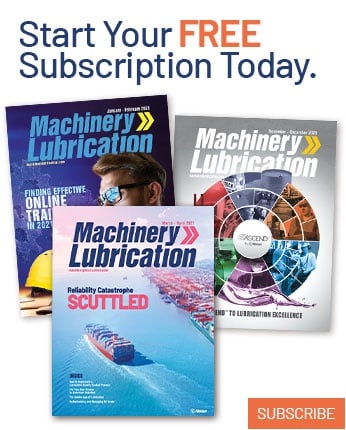