Middle management resistance to change is now the No. 1 obstacle to implementing the innovative business system known as lean production, according to a new survey completed by nearly 2,500 businesspeople and conducted by the Lean Enterprise Institute, a non-profit management research center.
Middle management resistance was cited by 36.1 percent of respondents in LEI’s annual survey about lean business system implementation in the U.S. The top three obstacles to implementation were middle management resistance (36.1 percent), lack of implementation know-how (31 percent) and employee resistance (27.7 percent).
Last year, backsliding to the old ways of working was the primary obstacle to introducing lean management principles, followed by lack of implementation know-how and middle management resistance. Backsliding dropped to sixth place in this year’s survey.
“The application of lean management principles exposes problems by traditional business systems, which often is threatening to middle managers in the problem areas,” said management expert James Womack, PhD, chairman and founder of LEI. “To get middle managers on board with lean transformation, organizations must transform the metrics and behaviors for judging their performances.”
For instance, Womack said, traditional financial metrics often need to be removed from day-to-day management decisions about key processes.
“Instead,” he said, “operating managers have to learn to help employees look for waste and remove it. The financial numbers will be positive.”
Since 2003, LEI has surveyed managers and executives annually about the major obstacles they encountered in transforming their companies from mass production to lean. The latest findings were based on more than 2,400 responses to a survey distributed electronically to 77,200 subscribers to LEI’s monthly e-letter. Respondents were asked to select all applicable obstacles from a list of 12 possibilities. Members also were polled on industry trends and the implementation level of their lean transformations. (See charts below.)
What is lean?
Lean production is a business system for organizing and managing product development, operations, suppliers, and customer relations that requires less human effort, less space, less capital, less material, and less time to make products with fewer defects to precise customer desires, compared with traditional management.
Toyota pioneered lean management as a complete business system after World War II. During the late 1980s, a research team headed by Womack at MIT’s International Motor Vehicle Program coined the term “lean” to describe Toyota’s system.
2007 “State of Lean” Survey by the Lean Enterprise Institute
Q: What are the biggest obstacles to lean implementation at your facility? (check all that apply)
Source: Lean Enterprise Institute, 2007 State of Lean Survey
Q: What is level of lean implementation in your business?
- Planning – no implementation
- Early – starting to implement in pilot areas; some progress being made
- Extensive – implementation under way; many areas of the business applying many lean tools; solid progress being made in many areas
- Advanced – lean has become standard way of operating; employees, supervisors and managers understand and use lean concepts; lean being extended to strategic suppliers
Source: Lean Enterprise Institute, 2007 State of Lean Survey
Q: What are the biggest trends in your industry now ? (check all that apply)
Source: Lean Enterprise Institute, 2007 State of Lean Survey
About the Lean Enterprise Institute
Based in Cambridge, Mass., the Lean Enterprise Institute (LEI) is a 501(c)(3) non-profit education, publishing, conferencing and management research center founded in 1997 by management expert James P. Womack, PhD. LEI helps organizations transform themselves into lean enterprises. Its workshops and workbooks teach lean techniques like value-stream mapping, lean manufacturing, and strategy deployment. Its management seminars and books help managers and executives develop the leadership behaviors that sustain lean enterprises. Its conferences showcase firms making lean breakthroughs. And its Lean Enterprise Partners research program with a small number of enterprises tests new approaches to lean management. The Lean Global Network, organized by LEI, has 12 nonprofit global affiliates in South America, Europe and Asia . For more information, visit http://www.lean.org .
Copyright, Lean Enterprise Institute (LEI),
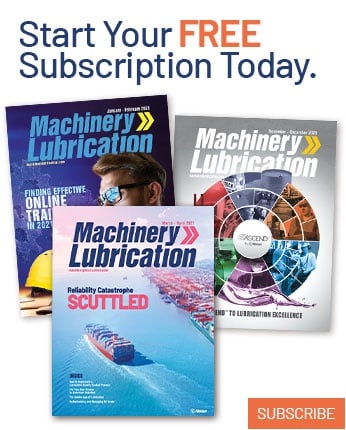