A measure of Mazda Motor Company’s current success is its flexible manufacturing system, which gives product developers and manufacturing the capability to make quick product adjustments when market demands change.
"Mazda’s production volumes are not as large as some other company’s, but we have used that fact to our advantage," said Mazda spokeswoman Mayumi Handa. "We designed each of our plants to be flexible and capable of producing different models on one line."
Mazdas are manufactured at four plants in Japan – two in Hiroshima and two in Yamaguchi. Mazda and Ford operate three joint plants in Thailand, the United States and the newest facility in China, the Changan Ford Mazda Automobile Company (CFME) in Nanjing.
"The basic Mazda production method is mixed manufacturing. All of our plants are flexible manufacturing and produce more than one model," said Handa. "This approach not only makes it possible for us to handle a wide range of product lines and models, but also allows us to meet changing market needs with efficiency, high quality and fast delivery."
For example, B-segment cars Demio and Verisa, the MX-5 roadster, the RX-8 sports car, the MPV minivan, the seven-passenger crossover CX-9, and Bongo series commercial vehicles all roll off one line at the Ujina Plant No. 1. The flexibility not only increases utilization capacity of existing models, but also enables Mazda to introduce new models at less cost in less time.
Mazda has increased efficiency by developing a "Kit Supply System" since 2004.
"Instead of having workers select the needed parts for each vehicle as it comes down the production line, all the parts required for a given vehicle are collected in advance, and accompany it on the conveyor," Handa said. "This reduces the number of things the worker has to be concerned about, making it possible for them to quickly and accurately select the correct components, which at the end results in reducing human errors and improving efficiency as well as quality."
Mazda is also implementing an integrated scheduled production system in cooperation with its supplier, meaning that every step in the production system derives from advanced planning. Mazda will fix the production schedule and notify the supplier several days before the production. Suppliers will deliver the parts of the right model, right color, and right trim in right order to the plants according to the production schedule. Components required for each step are supplied as they are needed, eliminating losses due to warehousing and redundant transportation.
Even the mode of transporting components has undergone innovation with the recent introduction of newly designed cargo containers in the company’s rail transport circuit. As part of Mazda’s Green Distribution System which seeks to improve transportation efficiency and cut CO2 emissions, the cargo containers are double the length of previous containers. A single truck carrying a container collects parts from multiple suppliers. The containers are then shifted to rail transport.
Mazda expects these improvements will reduce energy requirements for logistics between regions by 27 percent annually.
"Green" technology extends to such production facilities as the paint shop where the new three-layer wet painting process promises to reduce carbon dioxide (CO2) and volatile organic compounds (VOC), a prime factor in smog. Adopted first in 2002, the process has resulted in a 50 percent reduction in VOC and a 15 percent reduction in energy consumption (CO2 equivalent). Mazda now deploys this paint process to all its plants in Japan.
Mazda always looks into innovations for both better vehicle quality and environmental awareness in every aspect. In 2005, the company developed the world’s first heat aluminum-steel joining technology used to join aluminum and steel (which never joint in normal welding processes). In the MX-5, for example, the technology is used to join the aluminum trunk lid to steel retaining bolts. The technology helps Mazda develop lighter cars for greater fuel efficiency.
Mazda is zooming toward its goal of making appealing products for its customers.
In fiscal year 2001, Mazda reported operating losses of approximately $120 millions. Flash forward to fiscal year 2006, and Mazda has now marked three consecutive years of record operating profits and net income with global retail volume rising 2 percent over the previous year.
Writing in Edmund’s Auto Observer, Michele Krebs noted, "Design and dynamics are at the forefront of this Mazda revolution, a reminder that in the car business, it really is all about product, product and product."
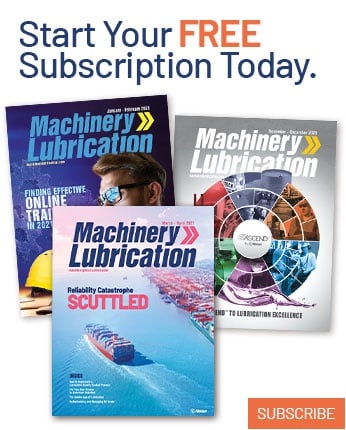