REPLIES TO TOR IDHAMMAR’S COLUMN “LET’S KILL WRENCH TIME STUDIES!” THIS COLUMN APPEARED IN RELIABLE PLANT’S MAY/JUNE 2007 ISSUE
HERE ARE THE COMMENTS. NAMES HAVE BEEN WITHHELD.
Comment No. 1
I'm involved with predictive maintenance at a major automotive stamping and welding facility. We are trying to use oil analysis, vibration analysis and infrared studies to predict failures and lately to reduce energy consumption. Pursuing this goal, we are often put in the middle three ways.
The maintenance people plan their life investments based on a stable and predictable amount of overtime. Maintenance leadership and planners hate to consume spare parts for something that could be "adjusted" rather than replaced. Finally, production never wants to give any equipment up unless it is already down. They are scared to death they either won't have adequate inventory for changing just-in-time customer demands. But more than that, they are scared that if a line breaks down, they won't have another "backup" to keep their people busy.
So in order to not rock the boat, everyone likes to see maintenance and tooling "busy". The plant manager came from skilled trades and is always scared "excess" skill trades people will be laid off, so he agrees with the system. In fact, infrared is the only one of these studies which is highly accepted. If they see a problem in a picture, it is hard to ignore.
We are most proud of our preventive maintenance (PM) program and the high percentage of wrench time devoted to PM tickets. We are told that to be "world class", more than 94 percent of our maintenance and tooling time should be PM-related. So our procedures are written to be very repetitive and give us huge numbers! For example, many of our electrical procedures call for us to retighten virtually all electrical connections once a month. Not only are we showing we are "proactive" by doing this every month. But after enough repetition we often find broken or cracked terminals and connections. So, our system obviously justifies itself. IMAGINE THAT!!
Our problems are generally not lack of attention to our equipment, but lack of direction. As long as we feel wrench time is the only way to exceed 90 percent P.M. work then we are "world class." Never mind that we are finding it harder than ever to be competitive price wise with the rest of the world.
From my point of view, the wrench time emphasis is as much a competitive problem for the big three pricing as the "legacy costs" of their long term employees.
Comment No. 2
Kill wrench time dead.
Wrench time studies are an antiquated attempt to quantify work done by a maintenance department. You'd be much wiser qualifying the work by measuring maintenance rework, MTBF, and chronic failures. In fact, one could argue that wrench time is diametrically opposed to the philosophy of reliability. No wrench time credit is given for documenting work, writing procedures, updating prints or other activities that improve long-term reliability. However, if a fan pump fails tonight, we'll throw an entire crew at the job – bring on the wrench time.
In my opinion, wrench time studies are done on the following premise: "If I can increase wrench time from 25 percent to 50 percent, I'll only need half as many mechanics." It would be better to ask, "How many mechanics would I need if I didn't have to fix (X) piece of equipment so often." In a time when everyone has fewer resources we should utilize them in the areas providing
greatest return.
Comment No. 3
I conducted a study on our wrench time early in 2006 evaluating our wrench time in 2005. I plan to do the same for this year. The purpose was quite different than you described in your article. The purpose was not to determine productivity of maintenance workers, but rather determine what amount of time was available for planning purposes. Yes, we found that we had 50 to 55 percent of our time available. We did not track planning (we have planners for that), getting parts, or travel as we considered that as part of our "wrench time". What we deemed as "non wrench time" were sick days, vacation time, training, break time, etc. – the true non-working time. We have had issues with attendance and so forth and wanted a better handle on how to minimize the non wrench time as we describe it. This is to better equip maintenance's staff. If you don't know how much time you have, how can you plan and schedule accurately? It's like going to the store to buy the groceries, but have no idea how much money you have. At the check out, you find you could have bought more … or you wind up putting stuff back.
We have many different trades in our maintenance departments and measured each trade. We found certain trades had more time available than others due to the nature of the work they performed. We also understood that an employee who is out for six months due to an illness would sway the statistics and made adjustments to the data.
We have conducted another initiative to help better define work tasks to be more effective and efficient in our PM program. As you stated, maintenance's job is to extend the life of the asset. That is our focus for our customer.
Comment No. 4
It was refreshing to read an article that addressed the status quo of maintenance practices. There are more. I see wrench time as defined as a routine task doer evaluation however I did use the concept to perform a study of my own. What I did was I met with our maintenance guys and discussed wrench time principles – then explained what we wanted was to list out “items that make you in performing your job less productive”, brainstorming if you will. Once I got them started, we quickly developed a list, included every suggestion whether I agreed or not. I took the list, consolidated it, four group meetings, and then sent it out via e-mail for them to prioritize the results, independently. We reviewed the results and at the end we had an “Areas for Improvement List” with 100 percent field buy-in seeing how it was there list. No one got upset. In fact, it was the opposite. We looked at the right things; they are what was important to them.
I think the concept (making and effective and efficient workforce) is a good one, however the defined process is not appropriate for our application. As you say, it could provide unintended results.
This is a pretty simple process and you can do it yourself – maybe that is the problem.
Talks to the guys, brainstorm what could be better, prioritize, implement.
Comment No. 5
You are right on, brother.
It definitely upsets folk, no matter how much lipstick you put on the pig, it's still a pig.
I have found that there is a direct correlation between wrench time scores and planned work / proactive work ratios.
Plants with a low percentage of planned work will have a low wrench time score.
How do you score three mechanics sitting in the breakroom? Suppose they're using that room to study mechanical seal failures? Does the observer dig that deep or just see the mechanics as non-productive? They would be scored in the "personal time" category, most likely.
For a confidence level of 5 percent, at least 4,000 observations are required. Witnessing (not participating in) a recent survey at a power plant, it required eight observers two weeks to gather that many observations. I could have used that 480 hours to help upgrade our technical database (which we don't seem to be able to get funds for). Mind you that six of these observers came from other plants – travel and living expenses incurred. It told them what we knew – travel time is high. Travel time is normally for tools and parts. If our technical database, including spares lists, standard job plans, drawings, etc., was up to date, planners would have more time to devote to
better planned jobs and less "planning time" in the field.
I'm preaching to the choir, I know. Lastly, wrench time measures utilization – not productivity. You sort of pointed that out in Point 6.
You're dad taught me this stuff, and changed my mind about tool time studies some 20 years ago.
Keep the faith.
Comment No. 6
I completely agree with your comments in the article “Let’s kill wrench time studies!” These are the days of the smaller, leaner workforce. Maintenance techs are forced to perform multi tasks with less support then ever before. In the old days we were able to have 14 to 16 techs per 100 production employees. Now we are lucky to have one tech per 100 production employees. We are force to multitask our selves to perform preventive maintenance, fire fighting maintenance, building maintenance, grounds maintenance and the like.
With all this facing us we still have the burden of making production schedules, dealing with schedulers that do not see the benefits of scheduling proper equipment maintenance. Wrench time studies truly only hurt an organization from the ground up, but management still relies on them heavily to see how the maintenance dept is performing. Also to see if you are overstaffed and how much they can cut the department FAT.
Maintenance departments are still seen as the dark hole or black hole in an organization. All we do is spend money, never paying back the company with products to sell.
Comment No. 7
After reading your article, I was happy to get the opportunity to respond directly to you with comments.
This is and has been a hot topic of discussion on site for almost a year now, and we are no closer to settling the debate. It is being offered to us as a way to measure effectiveness, and to utilize manpower to better cover our gaps. The bottom line is that we are short of people and there is as much or more work than before. Period.
It strikes me that these conversations with management are like arguments I've heard over the years about religion. If you believe it, then you can make an argument for it. But these arguments are not based on factual data, but on beliefs that this or that will work in the right environments or at the right time. And that is an acceptable argument for religious beliefs, but not for the manufacturing floor where real orders, real breakdowns, and real work has to be performed.
Are there tools out there to help us manage equipment repair? Absolutely. Are there numerous opportunities for us to improve on planned maintenance, preventive maintenance, equipment and parts inventory, etc.? Absolutely. But in order to achieve any lasting improvement you must look at all the pieces of the puzzle, not just a selective slice here and there.
The batter that hits the ninth-inning home run does not tell the story of the game.
Comment No. 8
I could not agree with you more. All six of your points are right on the money and the results are too easy to manipulate. In our case, it is cheaper to discuss wrench time that it is to discuss/address issues such as stores, BOMs, acurate PMs, etc.
Comment No. 9
I weigh in on the side of a need for reviewing management practices. I work in a chemical plant as a maintenance mechanic. We have two mechanics and one electrician and we are non union. We manufacture products for the forest products industry (thermosetting resins).
About eight years ago, the company made the move to lean manufacturing without explaining the new business model to the employees. Our total head count at the plant went like this pre-lean:
1-site leader, 1-chemical engineer, 1-production supervisor,1-trucking dispatcher, 1-office manager, 2-office workers, 1-maintenance supervisor, 2-mechanics, 1-electrician, 2-QC, 12-operators, 1-utility worker, & 6-truck drivers.
Since lean, we've eliminated the 1-office manager, 1-maintenance supervisor, 1-QC, 4-operators, 1-truck driver. We just hired a chemical engineer after being without one for the past six years. The four operators have quit and not been replaced because we were told the industry is soft (housing slowdown). We run three shifts, 24 hours a day, 365 days a year.
Using the lean model, I have been given or taken on tasks like purchasing for maintenance and safety supplies and keeping up with the inventory on all these products. We use SAP for our maintenance program, so I get to manage that. We have started meeting the requirements for PSM, so I've adopted the parts that require maintenance attention (equipment files, P&IDs, etc.). I also get to oversee construction projects that we do at the plant. I get to screen new vendors, maintain eligible vendor information and orientate contractors. Maintenance mechanics have to contribute about 15 hours a week to unloading raw materials. A spotter is required because of the hazards of one chemical we use (phenol 100 percent). The other mechanic usually does this. The job requires watching the unloading hose being connected and disconnected about 20 minutes out of the hour, three times a day.
The second mechanic will spend the 40 minutes that it takes to pump off the liquid, the time between hooking and unhooking the hose, visiting with the truck drivers, smoking and drinking coffee. Nothing else is required of him when he is spotting for the unloader. This time could be used to attend to small PMs, but management just overlooks it. The electrician spends his spare time forwarding e-mail jokes and porn around to friends on other jobs. The electrician is not required to assist with general mechanical duties. I have to attend morning meetings and give an account of my actions and constantly hear that I need to spend more time on my tools because we run such a large PM backlog list. That would be the idle situation, just being able to spend my day on my tools, considering that's the only job I'm paid for.
In the new maintenance department, we are all equal – in policy only, not work obligations. We no longer have any day-to-day planning for work. If you want to pickup a PM and do it, that is fine. If not, I'm the one who hears about the backlog. You were on target about management upsetting people when they bring up counting tool time. I've grown tired of hearing it. I've started looking for another job after 18 years. I have a large network of friends in our area and I'm finding that their jobs are being run the same way. What ever happened to give me the best and brightest and build a team?
My understanding about lean is that when you identified the two classes of workers (ants and slugs), you were to ride the slugs out. We've chosen to keep them and not hold them accountable. And as for rewarding those that step up, we haven't chosen to apply that part of lean, either. We have people who are caught sleeping on the job, spending the day on the phones talking with friends, washing cars after hours, bringing DVD players and watching movies, and nothing has been done.
Our new engineer has been upsetting the operators by asking them to do task that are impossible considering their procedures. He has not taken the time to understand their job duties. I see the same thing in the site leader who has been on the job for two years. He will tell me how long it will take to do a shutdown on equipment, even when I pull the history and try to explain why it took this much time in the past. I'm told I'm just being negative. There is a lot to be said for those who come up through the job with OJT.
An example from last week. We have two reactors that we manufacture the resin in and they run using a vacuum. So, each reactor has its own vacuum pump and we have a spare vac pump piped into the system in case one fails. On Monday, we have the operator conduct a check on the spare vac pump (weekly PM) by running it for one batch. Well last week, the pump failed to pull a full vacuum, so the operator could not start the batch. The operator told the electrician who is hanging out in the control room and he told the operator to just skip the test and use the regular vac pump to make his batch (noon Monday). On Tuesday morning, I'm questioned in the morning meeting about what is going on with the vac pump. I hadn't found any notifications written that morning in the work order system and no one communicated that the pump was not working. I had already been working on a critical agitator that had been down since Monday and was going to have to be replaced. Loss of this agitator was affecting our batch times and causing us to short product to our customers. We supply JIT. In the Tuesday morning meeting, we determined the critical path was to:
1. Get the vac pump working.
2. Get the agitator working.
3. Rebuild a plate cooler that the second mechanic had been told to rebuild by the site leader two weeks ago.
I communicated the critical path to the second mechanic and went to work on the vac pump by myself. The second mechanic went off and doodled with something minor and did spend some time talking with drivers in the smoke area. The electrician hung out in the control room. I finished the pump and communicated to the operator, site leader and production engineer. The site leader asked about the plate cooler and where the second mechanic was on that project. I had told him the parts had been in for two weeks and no action had been taken. He reassigned the task to the second mechanic as No. 3 on the critical path. The second mechanic gets mad and, after a temper tantrum, starts working on item No. 3. In the mean time, I'm off to the machine shop to get a coupling made to mount a different agitator to the slurry tank that is critical path No. 2. This is causing us to short product to our customers and we could miss a load altogether. I spend the rest of the week working on building a new mount for the different agitator by myself, along with doing some planning for a shutdown in two weeks (setup vendors, schedule workers in). The second mechanic was finished with the plate cooler after a day and a half. Friday, I pickup the coupling from the machine shop and continue working on the mount frame. Needless to say, it didn't get installed before we clocked out on Friday. I never did get any help on critical path No. 1 and No. 2.
Is it just me or is there a leadership vacuum? I've tried taking charge and have been told "who the f--- died and made you boss". There’s no support from management, so I have just thrown my hands up. I've communicated these problems to regional administrators and just get a shrug and am told don't take it personnel. And like I said earlier, I've talked with a lot of people who are fighting the same problem. It's not just at our site. I don't know if you will get the feedback by the problem is out there. Counting wrench time is a waste until management steps up.
Comment No. 9
I agree with most of your statement regarding the value or lack of when measuring wrench time for jobs. My experience has been this works great for assembly line-type operations or in other applications where external variables can be rigidly controlled. I have participated in many of these time and motion studies over the past 30 years and have yet to have two identical times for the same task. Environmental conditions, equipment conditions, lockout/tagout requirements and a host of other variables can have a huge impact.
Comment No. 10
I agree with you completely on the wrench time study. You made several valid points in the article. Any top mechanic will try to spend time looking over a job in order to do the job in the safest and quickest way possible. The only place I could see a wrench time study having any use
would be in a rebuilding facility where the mechanics are disassembling machines, replacing the parts and putting the machines back together. Studies like this are more of a waste of valuable time that could be used in identifying ways to make a job or machine safer or more reliable to reduce the need for wrench time.
Comment No. 11
It is long overdue to recognize the craftspeople of the world as problem-solvers and continuous improvement drivers in our industry. You are advocating what I have been doing for many years with great success. As a result, I have obtained reliability well over 96 percent in a continuous, automatically operated industrial plant. Another benefit of high uptime is that craftspeople can be eliminated from night and weekend shifts. Pressure-situation call-ins are minimized.
Craftspeople are better utilized doing equipment inspections, scheduled down job planning – i.e., knowing and having time to think out the job that they are going to perform. This is much more productive than having someone give them a package cold turkey to perform. Who knows the equipment better and what improvements should be made than the craftspeople?
Wrench time for craftspeople should not be higher than 25 percent. If it is, there is a problem in the facility.
Comment No. 12
I worked in a power plant for 30 years in the electric utility industry – a 1970s 600-megawatt coal plant. It doesn’t matter what you call it, or what its supposed purpose is, it is demotivating. I believe in setting up the processes, determining what you want to accomplish and by whom, and then training and making sure the process works. Measuring is subjective and most people know when measurements are happening and change their work habits that day. Even though there are many measurables in a time study that are considered productive activities, management only looks at wrench time. There are much better ways to get the workers fully engaged and productive. There are better goals than wrench time.
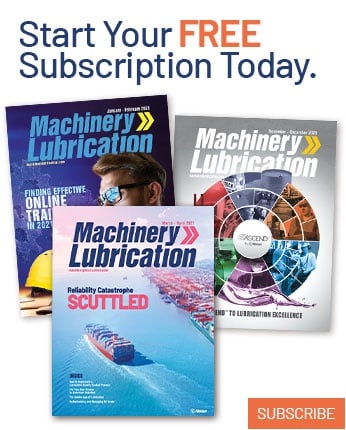