I've performed a significant number of lubrication surveys and audits in every conceivable industry, from food production to steel mills, cement plants to pharmaceutical manufacturers. While the industry may change, one common problem I see is a lack of understanding when it comes to insuring that the proper lubricant has been selected for a given application, while at the same time insuring that the optimum number of required lubricants is inventoried. This process is a careful balance of two needs: the application of lubrication engineering logic to select the correct lubricant and a focus on product consolidation (or deconsolidation if an insufficient lubricant exists) to insure that a proliferation of different lubricants of a similar nature occurs. This column will address the act of lubricant consolidation or optimization.
Lubricant consolidation is a straightforward process. The first step is to assess each oil or grease lubrication point to determine the technical requirements. Initially, base these requirements on application (make, model, load, speed, etc.) and operating context (ambient temperature, humidity, duty and loading cycles, etc.) rather than any specific manufacturer or brand. In doing so, the lube engineer should assess physical and chemical performance priorities of the lubricant (mineral vs. synthetic, viscosity and viscosity index, load-carrying capability, NLGI grade, demulsibility, water washout resistance, etc.) rather than brand-specific selections. Second, convert these technical specifications to a specific generic class of lubricants (e.g. mineral-based ISO VG 320 EP gear oil or ISO VG 68 R&O oil) for each machine. Third, reduce the currently stocked lubricant to the same generic technical specification (e.g. mineral-based ISO VG 46AW hydraulic fluid or PAG synthetic ISO VG 46 compressor fluid) and compare the choices with one another.
At this stage, eliminate any redundancy in currently stocked lubricants (two products with the same technical spec) and rectify any omissions with a new product selection. Finally, take a second pass across the technical specs for each machine to see if you can eliminate one or more less commonly used lubricant types, perhaps in situations where an "either or" decision can be made, such as deciding between two close viscosity grades, or a summer/winter lubricant change which can be consolidated to a single multi-grade or synthetic lubricant.
Perhaps the most common means by which product proliferation occurs is when new equipment is purchased. Anxious to maintain the warranty supplied by the OEM, the plant decides to stock a "special lubricant" recommended by the manufacturer. Is this necessary? In a few isolated cases, a highly specialized lubricant is required. But in the large majority of cases, applying the same logic used to consolidate - build a solid technical spec of the lubricant's required physical and chemical performance properties, then select one which meets these requirements - yields an option to use a lube currently stocked by the plant. But wait, what about warranty, you say? Surely we will void the warranty by not using the "recommended lubricant", right? The answer is an emphatic NO!
Based on the 1975 Magnusson-Moss federal warranty law, you can't void a warranty by using components that aren't supplied by the OEM, unless the component can be proved to have caused the failure. As part of this, the law specifically prohibits an OEM from requiring that a specific brand of consumable such as a lubricant be used to
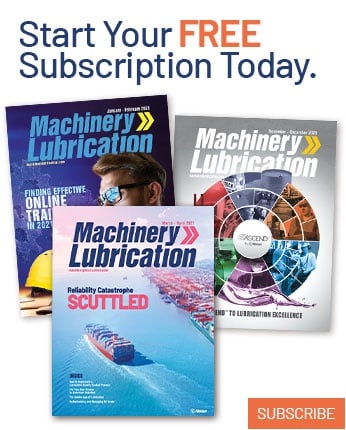