Baseball players speak of the Louisville Slugger bat the same way violinists dote over the Stradivarius or pianists praise the Steinway. Ballplayers, however, use more colorful language than their concert colleagues.
"One day I came into the hotel room - we were in St. Louis - and Ted had just gotten some new bats," recounts former Boston Red Sox pitcher Charlie Wagner in David Cataneo's book "I Remember Ted Williams." "The minute I got in, he said, 'Feel these goddamn bats.' You know, he swore a lot. He said, 'Damn, these are the best bats. Look at them. Feel that son of a bitch.' I looked at the bats and I sat on the bed and watched him. He was shaving some of the handles on them. The wood shavings were going all over my bed. That didn't bother him.
"Then he looked in the mirror. ... He's looking in the mirror and saying, 'Jesus Christ . . . Jesus Christ. Boy, oh boy, give me that bat. Boy.' Then he swung the bat at the knob of my bedpost and knocked my bed down. He knocked the post off my bed. He said, 'Hey, call 'em up and have them send up another bed.' It was that simple."
The Hillerich & Bradsby Company, maker of the Louisville Slugger, has had a storied, romantic relationship with the game of baseball - and its players and fans - since John A. "Bud" Hillerich turned out the very first product in 1884. With 123 years (and counting) under its belt, the bat and the company have earned a reputation for quality, craftsmanship and overall manufacturing excellence.
"I'd have been a .290 hitter without a Louisville Slugger," Williams frequently bellowed. "The Splendid Splinter" ended his Hall of Fame career with a .344 batting average, including a .406 mark in 1941.
"We're trying to get guys to feel as comfortable as they can while they are failing 70 percent of the time at what they're trying to do," says Chuck Schupp, the director of professional baseball at Hillerich & Bradsby.
Indeed. While Williams' career average is seventh-best all-time, it still equates to a 65.6 percent failure rate. For every 100 official at-bats, he failed to hit safely 66 times.
At the bat, failure is an accepted and unavoidable part of the game.
At the bat plant, though, failure is completely unacceptable and avoidable.
In the reliability game, H&B's manufacturing facility in downtown Louisville, Ky., swings a pretty mean stick.
Bill Dreschel was hired by Hillerich & Bradsby in 1966. A former machine operator, he is one of the plant's two millwrights.
Just the Facts |
|
TALENT AND TENURE
Ballplayers evolve over the course of their career in order to maintain or enhance their status. In his first 261 games, Babe Ruth had nearly six times as many singles as home runs. He averaged one homer every 33.9 at-bats. But from 1920 to 1933, a span of 1,959 games, he averaged one home run every 10.8 at-bats. He had nearly half as many round-trippers as singles. Conversely, Ichiro Suzuki averaged nearly 17 home runs per season in the Japan League, but found his role in Major League Baseball as a singles hitter. In the U.S., he averages 181 singles per season.
H&B's status in regard to machinery maintenance is exceptional, but the way that it achieves high levels of plant reliability is evolving.
For the past quarter-century, the wood bat factory's difference-maker has been knowledge and experience, mixed with the teachings of W. Edwards Deming.
"Reliability for us has traditionally been a function of longevity," says Bob Hillerich, who oversees facilities and maintenance at the plant. "We have relied on hundreds of years of collective experience."
Computers and automation equipment play a much bigger role today at the Louisville plant.
In early 2006, the plant employed 25 hourly production and five hourly maintenance workers, all of whom had at least 37 years of experience with the company. There had not been a new hire since 1974. When many of these unionized workers came to the company, the plant was still making game bats for Mickey Mantle, Hank Aaron and Roberto Clemente.
"You aren't going to find that anywhere else in the world," says John A. "Jack" Hillerich III, the great-grandson of the company's founder and the current chairman of the board. "Thirty-seven years . . . that was the new guy."
Coming into 2007, the maintenance department's two millwrights - Joe Davenport and Bill Dreschel - had been with the company a combined 77 years. Carpenter Dave Tully was hired in 1970. Maintenance supervisor Rouns Pence, age 70, was hired in 1963.
"These guys have grown up with the machines," says Bob Hillerich, who is Jack's nephew. "They started with them and have been working with them forever."
As a result, the more than 200 production machines and mechanical systems have hummed along quite nicely.
"We don't have reliability issues," says Dreschel, a millwright who joined H&B in 1966. "We rarely have breakdowns."
Bob Hillerich believes the site is in good standing when it comes to uptime, mean time between failure and other universally used maintenance metrics, but he can't provide details. That isn't for confidentiality reasons.
"We don't have any metrics that we track right now," he says.
He's telling the truth. These people's hands have traditionally been in and around machines, not tied to a computer system. For the past two decades, the department's maintenance management software program, called Alpha Four, was on a 5.25-inch floppy disk.
"I wouldn't say that we've gotten to this point based on luck," says Bob Hillerich.
Luck doesn't get you $100 million a year in sales and 70 percent of the big-league bat business.
"If it wasn't for these workers' experience and knowledge, we would have fallen off our feet a long time ago," he says.
Major-league player bats hang to dry after receiving a clear finish.
A DOSE OF DEMING
There have, indeed, been tenuous times.
The company was cruising along in the mid-1970s, annually making 7 million wooden bats and 1 million PowerBilt golf clubs (persimmon drivers and fairway woods) for professional players and the general public.
"Then along came the aluminum bat, and metal woods and investment-casted irons, and the rise of Asian manufacturers," says Jack Hillerich, who was president and chief executive officer of the company from 1969 to 2002. "When all three of those hit in the late 1970s and early 1980s, we knew something was seriously wrong. We were in trouble."
Such times call for new solutions.
In 1980, the company purchased a plant in Ontario, Calif., to manufacture aluminum baseball and softball bats. Today, the site makes nearly 2 million bats per year. But entering the aluminum market wasn't going to strengthen the flagship wood bat line or plant.
The Louisville Slugger trademark is burn-branded into ash bats.
An NBC television program on W. Edwards Deming titled, "If Japan Can, Why Can't We?" stoked Jack Hillerich's interest. In 1984, he and another company executive attended a seminar taught by Deming.
"We said, 'OK, the Asians are coming. We better improve the quality of the product,'" says Hillerich. "We went to Deming's seminar, and he didn't talk about the quality of our product - not for one second. He talked about staying in business. He talked about the fact that if you don't change, you won't succeed and you won't be here tomorrow. And, he talked about quality of management.
"We were thinking that we needed to make our products a little bit better with more quality. We came away thinking that we needed to improve the overall quality of our company."
Hillerich eventually sent 40 employees (20 from management and 20 from the union) to five-day Deming seminars.
Around the same time, he also instituted elements of Total Productive Maintenance, just-in-time manufacturing and Japan-style continuous improvement.
Kentucky is today home to many plants owned by companies that have become synonymous with Deming/CI/lean ideals - Toyota, General Electric, Ford and Johnson Controls, to name several. However, few have been at it longer than H&B. Its leadership is shown in the fact that Jack Hillerich serves on the W. Edwards Deming Institute board of trustees and is on the executive board of the Louisville chapter of the Center for Quality of Management.
"We live this stuff every day," says Hillerich. "It's to the point where people on the plant floor aren't even thinking about it, but they are doing it."
Adds production coordinator Brian Hillerich, who is Jack's nephew and Bob's younger brother, "Continuous improvement has always been the mantra here."
Louisville workers consistently develop innovative ideas that eliminate problems, and improve productivity and reliability.
"Having sawdust continually on the ways and guides is tough," says Bob Hillerich. "When the machines originally arrived here, fluid ran through to keep the machine cool while the bat spun inside the 'stay ring'. Daily, we'd have one spark and flame. We'd have to shut the system down. (Machinist) Leon Mathis and I knew there was a better answer out there somewhere. The machine manufacturer said one didn't exist. What we wanted was a bearing. That way, the bat could slide through the bearing and we could eliminate the fluid and the grease. It took Leon about a year of prototyping to achieve the solution, and it worked. We haven't had a shutdown as a result of a flameout in nearly three years.
"It's all about trying not to Band-Aid the problem. You have to figure out where the problems are coming from. You go through the seven-step problem-solving methodology (a continuous improvement tool). Let's look at the multiple potential causes and try to get it down to the root cause or causes."
14 POINTS: FOLLOWING THE DIRECTION OF DEMING |
|
In other instances in recent years, maintenance workers have: worked with a manufacturer to develop an automatic lubrication system; installed air nozzles to create an innovative system that keeps wood chips from collecting and jamming the loader path on an important lathe; and in four hours built a replacement shaft for an Italian-made processing machine when the original equipment manufacturer quoted two weeks to make a new part.
"You would have thought that in 123 years of making baseball bats we would have figured it all out," says plant general manager Frank Stewart. "But as you well know, in the business of improvement, you are never there. It's always, what can I do better? What can I improve today?"
Since 1984, Total Productive Maintenance has also elicited benefits.
"We have a maintenance department, but the goal, of course, is to get operators to do as much preventive maintenance on their machine as possible," says Stewart. "The operators do routine maintenance. They monitor the performance of the equipment and do routine checks of fluid levels. We want the equipment to run when it's supposed to run and do what it's supposed to do. We aim for predictability. TPM helps us accomplish that."
Plant general manager Frank Stewart used to be the commander of a U.S. Navy submarine.
TED WILLIAMS: THE CUSTOMER KNOWS BEST |
Ted Williams was fussy about his Louisville Slugger bats. He once complained about the way the handle tapered on his favorite bat. He sent them back, saying their grips didn't feel right. They weren't. Hillerich & Bradsby staff members measured the grip with calibrators against the models he had been using. They discovered that Williams' new bats were 5/1000ths of an inch off. Williams also could tell differences in the weight of his bats. J.A. Hillerich Jr., a late president of the company, once tested Williams. He gave him six bats, five weighing exactly the same, the sixth weighing one-half ounce more. Williams easily picked out the one with the minute difference. "Ted used different models for different pitchers and different times of the year," says chairman of the board John A. "Jack" Hillerich III. "The difference between the models was almost nothing. It was like a 64th of an inch difference in the knob. He changed them so minutely." |
CHANGE AND CHURN
The H&B plant has a strong history, but as mentioned earlier, evolution is under way. The sweet spot remains high reliability, productivity and quality, as well as fiscal prudence. But several factors are leading to a plant with a distinctly different stance and stroke. The workforce is, by far, the biggest factor for change.
In September 2006, the company closed its Little League and miniature bat manufacturing plant in Ellicottville, N.Y., and shifted that production to Louisville. When the New York workers opted not to make the move to Kentucky, H&B hired 26 new employees to run those lines.
"Over the past six months, we have doubled our workforce," says Stewart. "Half of our workforce averages 35 years on the job; the other half has six months."
In many respects, the new employees are starting at square one.
"Most of these people have never worked in a manufacturing facility before," says Bob Hillerich. "We've had to provide a great deal of education about our business and processes. We're also teaching them 5-S cleanliness techniques at the same time that we are teaching them the TPM system. It's a lot to digest."
Bats wait to be loaded into a sanding machine.
The influx of new blood isn't just from the plant closure and consolidation.
The Louisville facility's old guard has begun to retire, and the retirements will only increase in the next few years.
Production is bracing for the departure of craftsmen who have operated bat lathes, painting equipment, foil-branding machines and fire branders for decades.
"Once these people leave, I will be in a world of hurt," says Brian Hillerich. "That's not too much of an exaggeration."
In maintenance, machinist Phil Davenport (hired in 1970) retired a few years back. Leon Mathis took his spot. Millwright Joe Davenport (hired in 1970) retired in early March. Rusty Browning has been with the company for eight months and currently serves in the role of millwright helper. The company added Rodney Lessler last year to the new position of journeyman repairman. Also, supervisor Rouns Pence will retire in August.
The company has taken several steps to aid the transition.
"A new employee hadn't been hired in production since 1970," says Brian Hillerich. "As a result, there was never a need to develop a training program. So, this has been a learning experience for us all. When I got my first new employee, I was like, 'OK, what do I do with him?' There were no records to fall back on. Luckily, the union stepped up and helped us immensely. It's mostly been the older employees showing the new employees how to do it. We're scrambling behind them, taking notes and documenting everything."
Brian Hillerich is the plant's production coordinator.
In maintenance, Bob Hillerich has been focused on trying to retain the wealth of knowledge in his crew.
"I'm terrified about Rouns leaving," he says. "We know what his 44 years of experience brings to this plant. We are going to spend the next six months really picking his brain and documenting what he does."
Bob Hillerich also has developed a two-year millwright apprenticeship, education and job-shadowing program.
Apprentices work with the millwrights on the plant floor. They also must take eight classes at a local technical college. Attaining Millwright 1 status involves successful completion of classes in electrical systems, welding, plumbing and HVAC. The Millwright 2 level requires completion of additional classes in topics such as programmable logic controllers.
Browning was the first apprentice in the program. Additional positions will be offered soon.
Hillerich has also promoted the classes to department veterans. Dreschel has taken most every class in the curriculum. The workforce changeover ushers in a new mentality. That is a plus and a minus.
"The days of 'I'm going to work for XYZ Company for 40 years' is ending," says Stewart. "That mind-set has changed around the country and in our company. The workforce of the future is going to be much more mobile. Fluidity - where employees stay a few years and then move on - will be prevalent."
But on the other hand . . .
"Having zero turnover is just as challenging," says Bob Hillerich. "You have great people, but they have done it the same way for so long that it's hard to convince them to really shake things up and push the envelope. In our case, we have had to embrace technology to a much greater extent. That's been difficult for some."
The production lines are shifting more and more to automation equipment and CNC lathes.
"In manufacturing these days, the only way you can compete is by being lean and efficient," says Stewart. "Most of the efficiencies that you gain have to do with processes and automation and how to get the most out of your manpower as possible. We are looking at how we can continually automate what we do in the factory. Machines are taking the place of what workers were doing many years ago. With the addition of new automation comes the concern, or the potential, of reduced reliability."
Bob Hillerich is addressing those issues.
The Alpha Four floppy-drive system crashed recently. That opened the door to purchase a modern computerized maintenance management software (CMMS) system from Mapcon Technologies Inc. The system went live on March 13.
"It's going to be a great advantage," he says. "Every morning, it will give us a list of machines that are due to be worked on. It also will give us a list of what tools and parts will be needed, and where they are located in the crib. That will facilitate and expedite success with the amount of new people and machines we have."
Machine history will also be housed on the CMMS, not in the heads of maintenance workers. That should help as new technicians seek ways to bolster reliability.
"You will eventually be able to type in a symptom, and the program will give you its top three best guesses on what is possibly wrong with that piece of equipment," he says. "A vibration here or a noise there points you in the direction of that type of failure. The program will also tell you what parts are needed for that job and how long it should take to fix it."
The system will also allow the department to formally compile, track and utilize metrics that will serve as indicators of the plant's overall performance.
Maintenance has also begun to expand its use of predictive technologies. Rodney Lessler, for instance, is being trained to use infrared thermography equipment.
A large percentage of workers at the site have been with the company for more than 35 years.
AN ICONIC COMPANY
While the plant floor undergoes these mechanical and personnel-related changes, many of the things that make Hillerich & Bradsby an American manufacturing icon remain in place.
As has been the case for 123 years, the Hillerich family is managing this team. John A. Hillerich IV took over the president and CEO roles from his dad, Jack, in 2001, marking the fourth generation of family leadership.
As H&B has done for 23 years, the company will put Deming's principles into practice. It will also pursue continuous improvement. "In fact, this gives us a chance to retrace and reinvigorate our work in these areas," says Jack Hillerich.
Bob Hillerich oversees facilities and plant maintenance.
Reliability will remain a function of knowledge, experience, insights and ideas.
And, the plant will continue to craft the bats for Major League Baseball's top players, as well as those who dream of getting there someday.
Whether you're talking Ted Williams, Alex Rodriguez, Bill Dreschel or Rusty Browning, Hillerich & Bradsby's claim to fame always has been about putting the tools of the trade into the hands of the highly skilled.
FROM COMMANDER OF A NUCLEAR SUBMARINE TO GENERAL MANAGER OF A BASEBALL BAT PLANT |
|
A PLANT THAT IS BY THE PEOPLE AND FOR THE PEOPLE |
|
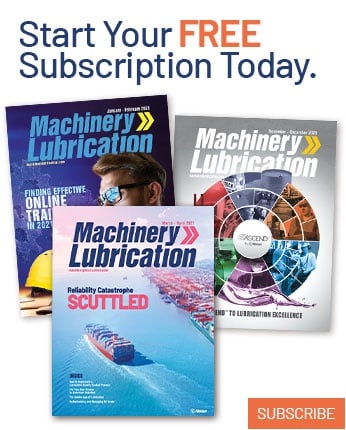