Aberdeen Group, a Harte-Hanks company, has put a stake in the ground with its latest report, “Manufacturing Flexibility: Synchronizing the Shop Floor and Supply Chain,” by defining manufacturing flexibility as the convergence of supply chain visibility, production process capabilities and dynamic decision-making. Competency in these business processes is established by performance in three key performance indicators (KPIs): finished goods inventory, on-time delivery and manufacturing cycle time. Based on the analysis of responses from over 200 manufacturers, results show that best-in-class manufacturers are:
- Three times more likely to have implemented open architecture automation systems
- Two times more likely to have manufacturing execution systems (MES) or enterprise resource planning (ERP) solution implementations that are readily configurable to changes in the production process
- Thirty-five percent more likely to have advanced planning and scheduling (APS) implementations, which are utilized in dynamic decision making and have supply chain visibility, bottleneck constraint modeling, and lean manufacturing optimization functionality
According to Matthew Littlefield, manufacturing research analyst with Aberdeen Group, “Manufacturers are indicating to us that they are being pressured to reduce the use of demand uncertainty buffers, such as finished goods inventory and lead time, while at the same time experiencing increases in the demand uncertainty they are attempting to buffer against. The only way for manufacturers to successfully address this conflict is to improve both their system performance and dynamic decision-making capabilities.”
Littlefield adds, “Our research shows the most effective way to improve overall manufacturing flexibility is to focus on improving two main aspects of the manufacturing process: production capabilities and dynamic decision making.”
Recommendations include:
- On the shop floor, move toward utilizing open architecture automation systems.
- MES and ERP implementations that are highly configurable to changes in the production process should also be utilized to improve production capabilities.
- An APS solution, either standalone or as an ERP extension, should be utilized to improve dynamic decision making. The APS solution should have supply chain visibility, production constraint visibility, and lean manufacturing optimization functionality.
More than 200 manufacturers participated in the study, including Advanced Micro Devices, The Coca Cola Company, ConocoPhillips, DuPont, Ford Motor Company and Unilever. This study is made available to the public through the underwriting of: Factory Physics Inc., Infor, Lawson, nMetric and Synchrono. To obtain a complimentary copy of the report, visit: http://www.aberdeen.com/link/sponsor.asp?cid=3859.
About AberdeenGroup, a Harte-Hanks company
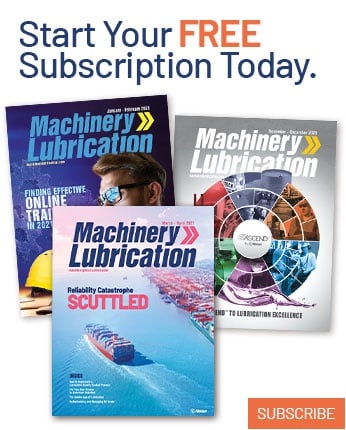