MSA on January 31 announced a strategic plan to improve the efficiency of its North American manufacturing operations by generating more effective use of existing and available factory space. Implementation of the plan – called Project Magellan – will result in the relocation of certain activities and the closure of certain facilities which are supporting those activities today. The initiative aims to lower costs, improve operating margins, enhance the company's competitiveness in key product segments and strengthen customer relationships by providing the best value in sophisticated safety products.
"Project Magellan is a multi-year endeavor that will significantly reshape MSA operations and enhance the efficiency of our manufacturing facilities for years to come," said William M. Lambert, president of MSA North America. "To achieve this, we will reconfigure our North American factory network in phases over the next three to four years through the development of new facilities and plant consolidations."
The company expects the initiative to reduce operating expenses by as much as $10 million a year once completed.
The optimization plan will initially impact three MSA manufacturing sites. First and foremost, the manufacturing of fire helmets at the company's facility in
The
In addition, MSA announced its intention to vacate its facility in
As a third step in this initial phase, the company announced it will shift its Mexican manufacturing operations from facilities in
"Our efforts in
As Project Magellan is implemented over the next several years, MSA will continue to evaluate the performance and utilization of all of its North American facilities while striving to align its business to best meet customer and market needs.
"MSA's business in
MSA currently operates 12 manufacturing facilities in
Lambert added that MSA is committed to making this manufacturing transition as smooth as possible for its employees, distributors and customers. MSA began notifying employees on January 30 and stressed that employment opportunities would be offered to affected employees as manufacturing shifts to new locations.
"We're committed to making this manufacturing transition as smooth as possible for our associates and transparent to our distributors and customers," Lambert said. "In short, it will be business as usual. Our customers and distributors in
Established in 1914, MSA is a global leader in the development, manufacture and supply of sophisticated safety products that protect people's health and safety. Sophisticated safety products typically integrate any combination of electronics, mechanical systems and advanced materials to protect users against hazardous or life-threatening situations. The company's comprehensive line of products is used by workers around the world in the fire service, homeland security, construction and other industries, as well as the military. Principal products include self-contained breathing apparatus, gas masks, gas detection instruments, head protection, respirators, thermal imaging cameras and ballistic body armor. The company also provides a broad range of consumer and contractor safety products through retail channels. These products are marketed and sold under the MSA Safety Works brand. MSA has annual sales of more than $900 million, manufacturing operations throughout the world, and more than 30 international locations.
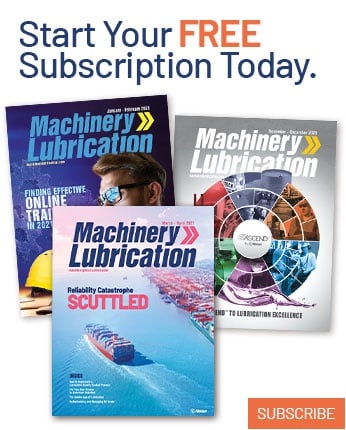