![]() |
People have a growing fascination with all things CSI. From video games to best-selling books and the top-rated CSI TV series, people just can't get enough, enthralled by the mystery, the systematic examination of evidence and the "eureka" moment when all the pieces come together and a case is solved.
Believe it or not, a group of Ford scientists and engineers experiences that same sense of mystery and satisfaction everyday – with one very big difference. Their investigations center on things automotive rather than human.
Home to about 85 test and materials engineers, Ford's Central Lab in Dearborn is the company's private CSI team, supporting product design engineers, manufacturing, legal, warranty operations and suppliers to identify the most probable cause of difficulties, ranging from the simple to the strange.
In a recent case, computers kept malfunctioning at the Lincoln Design Center in Dearborn, Mich., for no apparent reason.
"We were seeing a lot of new computers in one particular area of the design center that were malfunctioning – sometimes within the first 30 days," says Ford commodity analyst Cyndi Morrell.
In fact, these computers weren't just experiencing software problems, their motherboards were corroding. Morrell turned to Ford's Central Lab to find out why.
Central Lab chemist Tom Munie discovered that the solder on the motherboards and other circuitry within these computers had been attacked by sulfur, causing severe, premature corrosion. After some investigation, Munie pinpointed that the modeling clay, used in abundance near where these computers were stationed in the design center, contained high levels of sulfur.
"That was only half the puzzle," says Munie, noting that computers had previously been working in this area without problems. "The kicker is because of a new government compliance, lead-based solder is being replaced with a silver-bearing solder. Silver readily reacts with sulfur, lead does not. That's why only certain computers were displaying the problem."
Thanks to Munie's investigative work, the Lincoln Design Center is moving toward using a modeling clay that contains less than 1 percent sulfur.
"We are also looking at other areas within the company that might have a high-sulfur environment so we can alert them to this potential problem and save instrumentation," adds Morrell.
Central Lab was also put on the case when tiny craters began to pop up on the paint surface of vehicles rolling off the line at the Michigan Truck Plant in Wayne, Mich. After testing samples taken from the center of these craters, Central Lab engineers found traces of silicone. A thorough investigation later revealed that the lint-free coveralls worn by workers in the paint department had been washed with a detergent that contained silicone. Silicone particles from these coveralls were entering the paint spray booth's air circulation system and landing on the wet paint, causing the craters.
In its Dearborn location since 1978, Central Lab has seen it all, says Kathy Minnich, manager. On a daily basis, Central Lab runs corrosion and durability tests on metal parts, textiles, plastics, paints and sealers; examines steel, iron and aluminum parts and components; reviews the chemical structure of materials to determine possible contaminants and impurities; and conducts fracture and failure analysis on items from headlamps to interior door handles. The facility is capable of running some 25,000 different test procedures in a day, often producing results within hours to meet customer expectations.
The full-service lab also has the most-advanced equipment, including a Skyscan Micro-CT, which basically works similar to a CT scanner found in most hospitals.
"We can take virtual slices of a part while still keeping the part whole, determine if internal defects are present, and then have the part reinstalled on a vehicle for continued testing to see how many miles the part can withstand," says Vladimir Beltran, lab development analyst.
While much of the work done at Central Lab revolves around vehicles already in production, the team also plays a critical role in launching new products and assessing the validity of new technologies.
"When Ford brings in a new concept,” says Minnich, “we can assess if the materials are durable enough to fulfill the customer's expectations – so they can take it to production with high confidence."
The lab services Ford facilities around the world and also works closely with suppliers, often doing parallel testing on parts and components. According to Allen Radke, supervisor of the lab's Metallurgy and Mechanical section, the team does its best to provide a purely scientific, non-biased viewpoint.
“We all work together to do the investigative reporting, find the root cause and determine the best solution to get us into a healthy situation and satisfy the customer as fast as possible," says Radke.
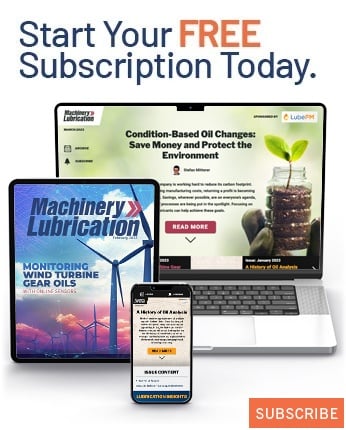