Most maintenance departments profess to be convinced of the need for maintenance planning and scheduling and condition-based maintenance. However, the benefit of using them together seems to be shrouded in mystery. Let’s open the hood and look at how they work together to produce results far exceeding that of the sum of the benefits of each used alone. Let’s start by briefly examining each of the concepts.
Maintenance planning and scheduling
In a
nutshell, maintenance planning and scheduling prioritizes and organizes work so
it can be executed in a highly efficient fashion.
Managers and hourly employees alike in stores, accounting, purchasing, engineering and production must buy in to the concept and do their part for it to work. Some of the major outcomes of planning and scheduling are:
- An organized approach to analyzing and executing any work identified.
- Detailed plans, rules and records for the evaluation and execution of work.
- Effective utilization of planners, supervisors and craftspeople.
These outcomes should yield these benefits:
- Cost savings due to efficient use of maintenance labor hours.
- Increased production yield from faster execution of all jobs.
- Reduced injuries and less stress from a better work flow.
As we can see, it’s all about efficiency and organization!
When maintenance planning and scheduling is implemented alone, craftspeople often continue to be frustrated with emergencies caused by “surprise” breakdowns, forcing them to bypass the planning and scheduling procedures they labored to hard and long to deploy.
Next, let’s look at condition-based maintenance.
Condition-based maintenance
Condition based
maintenance, or predictive maintenance as it’s often called, can be defined
different ways. However, it is important to note that it goes far beyond
vibration analysis.
Figure 1. A Common Definition of
Condition-Based
Maintenance
The outcome of condition based maintenance is finding future failures before they manifest themselves as a breakdown of equipment or a component. A breakdown is defined as the loss of the function a component was designed to accomplish – for example, when a pump stops pumping.
- As we can see, the outcome is pure information – knowing that an item will
break in the future. This in itself does not prevent any failures, but it allows
you to:
Gather information about the equipment and parts affected by the future breakdown. - Plan and schedule the repair.
- Eliminate the cost of consequential damage caused by a functional failure.
When you repair it before a breakdown develops, you typically save 50 to 90 percent (compare Figures 2 & 3).
Figure 2. Planning and Scheduling Without Condition-Based
Maintenance. When a breakdown is discovered, you must
diagnose, plan and
repair it immediately to get production back
up and running. Typically no
resources are spared at this time.
Figure 3. Planning and Scheduling and
Condition-Based
Maintenance. When impending failure is discovered ahead of
time, you have time to plan it, get parts, schedule and repair it
before
a breakdown occurs. This typically costs 50 to 90
percent less and can often
be scheduled with other repairs for
less production impact.
The degree of savings above depends on how early you catch it, if can be repaired online and the cost of repairs. Compare finding an impending breakdown on a standard motor you have in stock, attached to a production line scheduled for maintenance next Wednesday at 8 a.m. to 4 p.m., to the scenario where a non-stock motor failed at night and forced a shutdown of the line for repair. The second scenario will cost much more than the first as people scramble to find what’s wrong, call in several trades and perhaps stores. Add overtime, production losses and contacting supplier(s) to find replacements and a familiar picture emerges.
Implementation of predictive maintenance alone frequently results in many items being flagged for repair. However, only some of them are actually being repaired as maintenance does not have the efficient work practices (read planning and scheduling). Of course, this demoralizes operators and craftspeople as most items they find using predictive maintenance still break down instead of being repaired when discovered.
The marriage
On the other hand, when
predictive maintenance and planning and scheduling are used together, they
produce synergies like:
- reduced cost of spares and material
- increased labor productivity (primarily in maintenance but also for operators)
- better job satisfaction
- increased production yield
- effective work practices
- improved production quality
By now, you can clearly see that two plus two can equal eight when you use planning and scheduling and predictive maintenance together.
Torbjörn (Tor) Idhammar is partner and vice president of reliability and
maintenance management consultants for IDCON Inc. Michael Lippig is the business development manager. Tor's primary responsibilities
include training and implementation support for preventive maintenance/essential
care and condition monitoring, planning and scheduling, spare parts management,
and root cause problem elimination. He is the author of “Condition Monitoring
Standards” (volumes 1 through 3). He earned a BS in industrial engineering from
North Carolina State University and an MS in mechanical engineering from Lund
University (Sweden). Contact Tor at 800-849-2041 or e-mail info@idcon.com. |
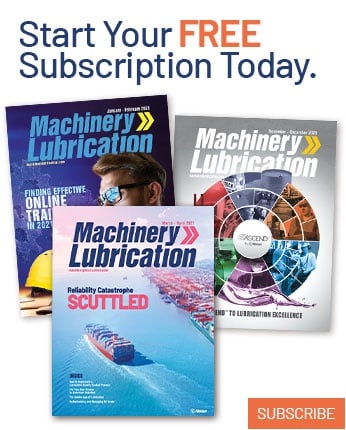