For today’s maintenance teams, the ability to make fast, accurate decisions can mean the difference between meeting performance goals and falling short. With economic pressures, workforce shortages, and rising demands for uptime, reactive maintenance is no longer a sustainable approach.
That’s where condition monitoring makes an impact. By delivering real-time insights into machine health, it empowers both maintenance and operations teams to make smarter, more confident decisions about when and how to service equipment. When paired with AI, expert analysis from condition monitoring engineers (CMEs), and seamless integration with systems like CMMS platforms, condition data becomes more than just information—it becomes the backbone of streamlined processes, improved asset performance, and stronger collaboration across teams.
Blending Continuous and Route-Based Monitoring for Optimal Data Collection
Effective condition monitoring starts with a criticality assessment to evaluate each asset’s impact on safety, production, and operations. This helps determine whether an asset requires continuous or route-based monitoring.
Continuous monitoring is ideal for high-risk or high-value assets where failures are costly. It provides real-time visibility into machine health, helping teams catch subtle issues early. Meanwhile, route-based monitoring is a cost-effective choice for lower-risk assets, allowing for scheduled checks without overloading resources. A hybrid approach ensures that teams collect the most relevant data at the right intervals to support timely decisions that prioritize the performance of critical assets.
Filtering the Noise: Reducing Alert Fatigue with Validated Insights
Once a blend of continuous and route-based monitoring has been established, it’s time to start looking at the data. One of the biggest challenges many teams face is alert fatigue. Alert fatigue happens when technicians are bombarded with frequent, non-critical alerts that drain attention and erode trust in the system. Left unchecked, this flood of low-value notifications can lead to missed warnings, delayed responses, and unnecessary stress on the team.
To prevent this, leading condition monitoring solutions use a dual-layered approach:
-
AI algorithms continuously scan data to detect anomalies and trends.
-
Condition monitoring engineers then review and validate these findings, applying human context to filter out noise, prioritize alerts based on actual risk, and provide prescriptive recommendations.
This combination ensures that only actionable, high-priority alerts and relevant expert insights reach the team, allowing technicians to focus on what truly matters. The result is less time chasing non-issues and more time executing high-value tasks, resolving critical problems faster, and proactively improving asset reliability. But to turn these insights into consistent results, teams also need structured processes that ensure every alert leads to the right action every time.
Creating a Documented Workflow with CMMS Integration
One of the most powerful ways to make condition monitoring actionable and unlock the full value of the data is through seamless CMMS integration. When actionable alerts are created and sent to the CMMS monitored conditions exceed thresholds, work orders are automatically generated—eliminating delays, double entry, and guesswork.
Every time a condition-based alert is triggered, your system should initiate a documented response that captures key details:
-
What was detected
-
When it occurred
-
What action was taken
-
Who responded
-
What the outcome was
Over time, this creates a centralized history of events and responses. Not only does this boost transparency and accountability, but it also allows maintenance leaders to track performance trends, enforce compliance, and train new team members more effectively. Here are the steps involved in a successful workflow:
Step |
What Happens |
Value Delivered |
1. Condition Data Captured |
Sensors continuously track asset performance (vibration, temperature, etc.). |
Real-time visibility into equipment health. |
2. AI Detects Threshold Breach |
Sensor readings exceed expected limits as defined by AI using historical trends. |
Early detection of abnormal conditions enables proactive action. |
3. Anomaly Categorized by AI
|
AI flags and classifies the event based on severity and pattern recognition. |
Reduces time spent reviewing normal or noncritical data. |
4. CME Validates & Prioritizes |
Condition monitoring engineer confirms severity and filters false positives. |
Prevents alert fatigue and focuses attention on high-impact issues. |
5. Work Order Auto-Created in CMMS |
CMMS receives validated alert and generates a work order instantly. |
Eliminates manual entry and reduces response time. |
6. Maintenance Team Executes |
Technician receives assigned task with asset history and clear instructions. |
Speeds response and improves accuracy and accountability. |
7. Action Logged in CMMS |
Technician logs work performed, parts used, time, and resolution. |
Creates a complete, auditable maintenance history. |
8. Status Updates in Real Time |
CMMS updates asset status and progress for planners and supervisors. |
Provides real-time visibility into work execution and asset readiness. |
9. Root Cause Analysis and Learnings Captured |
Post-job data feeds into historical records, enabling root cause analysis and identifying systemic failure patterns. |
Drives continuous improvement, better decision making, and future automation opportunities. |
Integrated systems also break down data silos. All relevant information—alerts, recommendations, actions taken—flows into a centralized hub.
The Power of Historical Data in Root Cause Analysis
One benefit of having this unified system is that when unplanned downtime occurs, historical condition data becomes an invaluable tool. Instead of starting from scratch or relying solely on memory, teams can review detailed records of past anomalies, interventions, and outcomes to spot patterns that may have been missed in the moment.
This visibility accelerates root cause analysis (RCA) by highlighting contributing factors, revealing failure modes, and providing a clearer timeline of how issues developed. It also helps distinguish between isolated incidents and systemic problems.
Calculating Business Value to Justify Investment
Data-driven decision making has a measurable effect on core operational metrics. Time-based preventive maintenance often leads to unnecessary work or missed issues. Condition-based workflows replace guesswork with precision, allowing teams to extend service intervals confidently and only intervene when necessary. This reduces both maintenance costs and risk of failure.
Improvements in uptime (OEE), mean time between failures (MTBF), and mean time to repair (MTTR) translate directly into cost savings and increased productivity. Organizations can clearly see the ROI of each action—from the moment an alert is triggered to the successful resolution.
Metric |
What It Means |
How Condition Monitoring Improves It |
Why It Matters |
OEE (Overall Equipment Effectiveness) |
Measures how effectively equipment is used, combining availability, performance, and quality. |
Detects issues before they cause downtime, allowing equipment to run longer, faster, and with fewer defects. |
Higher OEE = more output, better product quality, and lower operating costs. |
MTBF (Mean Time Between Failures) |
Average time a machine runs before failing. |
Enables early detection and correction of issues before they escalate into failures. |
Longer MTBF means fewer breakdowns, lower maintenance costs, and extended asset life. |
MTTR (Mean Time to Repair) |
Average time it takes to diagnose and fix a failure. |
Provides technicians with real-time alerts, asset history, and recommended actions. |
Shorter MTTR minimizes downtime, reduces overtime, and improves team productivity. |
ROI (Return on Investment) |
Measures financial return on condition monitoring tools and strategies. |
Tracks how quickly maintenance actions prevent costly failures or production losses. |
A clear ROI helps justify continued investment in reliability technologies. |
Supporting Sustainability and Safety Goals
Beyond productivity gains, condition monitoring plays a significant role in helping organizations advance their environmental and safety objectives in measurable ways. By enabling smarter, data-driven decisions, condition monitoring reduces the need for unnecessary maintenance, limits machine overuse, and prevents waste associated with last-minute breakdowns. It also helps keep assets performing at their peak, thus reducing energy usage and carbon emissions. When equipment is only serviced when it truly needs attention, and early in the failure curve, both material and energy use are optimized—supporting a leaner, greener operation.
Condition monitoring also contributes to a safer work environment. Unplanned failures often lead to hazardous situations—whether it’s equipment running in a degraded state, unexpected downtime in production-critical areas, or emergency repair scenarios that increase injury risk. When failures can be predicted and maintenance can be scheduled, it creates a more stable and predictable workplace.
Key sustainability and safety benefits include:
-
Reducing energy consumption by identifying inefficiencies before they worsen
-
Minimizing waste from unnecessary part replacements or emergency repairs
-
Avoiding excess lubricant usage and contamination through precise scheduling
-
Decreasing reliance on overnight or rushed work, cutting emissions from emergency shipments and overtime labor
-
Improving worker safety by reducing reactive maintenance and emergency callouts
-
Supporting broader ESG and compliance initiatives with traceable, data-backed decision-making
Turning Insight into Impact
Condition monitoring is more than a tool for catching faults—it’s a catalyst for transforming how decisions are made across maintenance and manufacturing operations. By capturing real-time data, connecting insights with CMMS systems, and empowering teams with expert guidance, organizations can shift from reactive fixes to optimized, proactive strategies.
With better decisions grounded in data, every part of the business—from the shop floor to the boardroom—can operate with greater clarity, confidence, and control. And that translates to lower costs, higher performance, and a more reliable future.
Did you miss part one on performing a criticality assessment? Catch up here: Maximizing Your Condition Monitoring Investment—Start with a Criticality Assessment
Turn real-time data into smarter decisions.
With AssetWatch’s predictive maintenance solution, you don’t just collect data—you act on it. Gain the insights you need to make faster, more confident maintenance decisions, reduce downtime, and improve performance across your entire operation.
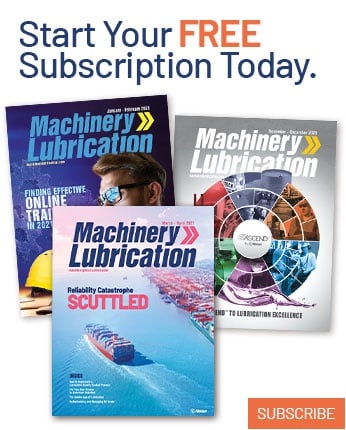