Heavy Mobile Equipment (HME) operates under some of the harshest conditions in the industrial world—dust, vibration, high loads, and constant movement are part of daily life in mining environments. To maintain uptime and extend the life of critical components like pins, bushings, and bearings, proper lubrication is essential. Yet despite the widespread use of automatic lubrication systems, lubrication-related failures remain a leading cause of unplanned downtime and safety incidents in mining operations.
Why? Because in most cases, there’s no way to verify that grease actually reached its intended target. The leading causes include leaking or bypassing injectors, ruptured hoses, empty grease tanks, all of which can go unnoticed by operators or maintenance teams until the component fails. The assumption that “the auto-lube is working” often leads to a false sense of security. Without confirmation of grease delivery, maintenance teams are effectively blind to one of the most preventable failure modes in mining equipment.
This whitepaper explores why grease delivery verification is the missing link in HME reliability—and how mining operations can address this vulnerability to prevent failures, reduce downtime, and improve safety.
Key Topics:
-
How Traditional Auto-Lubrication Systems Work—And Where They Fell Short
-
The Problem With Upstream Monitoring in Auto-Lube Systems
-
Why Downstream Monitoring is More Accurate (And What is It?)
-
Solutions for Downstream Grease Monitoring
- Maintenane Integration and Impact
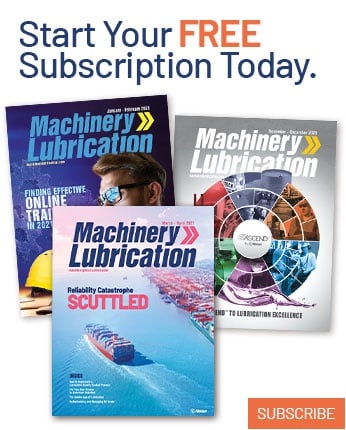