What is Reliability-Centered Maintenance?
Reliability-Centered Maintenance (RCM) is the systematic technique of optimizing a maintenance process to increase critical equipment's uptime and production capacity by analyzing breakdowns and determining proper maintenance requirements within that asset's unique operating environment.
Although its roots can be traced back to the aviation industry, RCM has quickly become a staple in many manufacturing facilities in every sector. Unlike other maintenance approaches that work on fixed schedules or run-to-failure strategies, RCM is considered function-oriented; it looks at each individual asset before assigning the appropriate maintenance tasks.
When implementing RCM, a maintenance team should ask itself several questions to identify key characteristics of an asset. These questions include:
- What functions should the asset perform, and what are the associated performance standards for this operating context?
- What are the potential failure modes for this asset when trying to fulfill its functions?
- What are the potential consequences of each failure mode on safety, operational efficiency, the environment, and the company’s bottom line?
- What are the most effective and efficient maintenance actions to prevent each failure mode?
- What would be the outcome if a preventive task cannot be found for a specific failure mode and the asset must run to failure?
The Benefits of Reliability-Centered Maintenance
Implementing an RCM program can provide several benefits to a maintenance team’s critical assets. These benefits include:
- Improved asset reliability and reduced unplanned downtime.
- Reduced maintenance costs. While initial program implementation may require an upfront investment, RCM helps optimize maintenance tasks and eliminate unnecessary work by focusing resources on preventing failures. This also reduces spare parts usage, labor costs, and required emergency repairs.
- Improved team member and environmental safety.
- Increased equipment lifespan. RCM focuses on addressing the root causes of failures and applying appropriate preventive measures, thereby extending the operational life of critical assets and creating a greater return on investment.
- Enhanced operational efficiency. Reduced asset failures and increased focus on predictable maintenance schedules drive smoother operations, reducing production disruptions and improving overall asset efficiency.
- Increased awareness of asset behavior. RCM helps maintenance teams better understand how critical assets function, how they might fail, and what consequences would arise from those failures. This allows teams to make more informed, timely decisions that will protect their equipment.
The benefits above can easily translate into visible improvements throughout a facility. By implementing an RCM program, facilities generally experience fewer unplanned breakdowns, leading to increased production throughput, reduced waste in multiple categories, lower maintenance costs, and more efficient operations.
These principles can be applied to nearly any asset within a facility, fostering a culture of continuous improvement that is centered on proactive maintenance.
The Challenges of Reliability-Centered Maintenance
While there are a host of benefits, as with any reliability program, a team trying to implement RCM can encounter potential challenges. These challenges include:
- Potentially significant up-front investment: RCM program implementation requires considerable time, resources, and experience to start the initial implementation. These resources often go towards data collection, data analysis, and continued training to properly apply RCM techniques.
- Properly skilled and dedicated team members: To bring the RCM implementation to fruition, a dedicated team with strong analytical skills, in-depth knowledge of critical equipment and processes, and a commitment to the methodology is needed.
- Resistance to change: Shifting from one maintenance approach to another can be met with resistance from team members who are comfortable with the status quo and the pre-established maintenance routines.
- Data-Intensive nature: RCM implementation requires accurate and detailed data on various topics, such as asset history, potential failure modes, and appropriate maintenance activities, for practical RCM analysis. Any gaps or inaccuracies in the data can negatively impact and hinder the process.
- Complexity and time commitment: RCM implementation requires a detailed analysis of critical assets, which can quickly become complex and time-consuming, especially for facilities with diverse assets.
- Potential for over-analysis: While RCM does require detailed analysis for success, there is a risk of over-analyzing the data if too much time is spent on low-criticality asset analysis. This can skew the program's focus away from critical equipment (which benefit more from detailed analysis) and can result in a lower ROI.
RCM Implementation Checklist
Effectively implementing an RCM program relies on several critical steps.
- Selecting the critical assets: Identify and prioritize the essential assets significantly impacting production, cost, and employee safety.
- Building a cross-functional team: Assemble a team consisting of employees from various sectors, including maintenance, operations, engineering, and other relevant stakeholders who hold in-depth knowledge of the prioritized assets.
- Gathering data and information: Collect all necessary data, including asset history, maintenance records, failure mode data, asset operating context, design specifications, and relevant industry standards.
- Performing a functional analysis: Define each prioritized asset's functions, purpose, and performance standards within its specific operating context and environment.
- Performing a failure mode and effects analysis (FMEA): Systematically identify all the potential functional failures, their failure modes, and the effects each failure would have on team safety, operations, the environment, and the facility’s bottom line.
- Designing and developing maintenance tasks: Based on the FMEA results, decide on the maintenance tasks necessary to prevent each significant failure mode. Consider multiple forms of tasks, including predictive, preventive, and even reactive where appropriate. Teams may also need to consider design or procedural changes to accommodate this.
- Documenting the plan: Document the findings and results of this analysis, the identified maintenance tasks, maintenance task frequencies, and team members who should be responsible for each task.
- Implementing the plan: Begin implementing the documented maintenance tasks, allowing time for proper training and resource allocation.
- Reviewing and refining: Periodically review the effectiveness of the RCM plan by tracking asset performance, analyzing failure data, and making the required adjustments to optimize the maintenance program. Done right, this will eventually become part of a larger culture of continuous improvement.
- Expanding the implementation: Once the program proves successful and all hurdles have been mitigated, gradually expand the RCM process beyond the initial critical assets to other priority assets within the facility.
Conclusion
Reliability-Centered Maintenance can offer a unique approach to protecting and managing critical industrial assets. By shifting the focus from reactive equipment maintenance to proactively preserving the integrity of critical asset functions, a maintenance and reliability team can produce significant and long-lasting benefits in terms of reliability, cost reduction, team member safety, and overall equipment efficiency.
While RCM implementation often requires upfront investments and commitments, the rewards of a long-standing program can significantly outweigh these costs. For industrial facilities in every sector looking to improve operational efficiency and safeguard productivity, utilizing RCM can provide a fundamental roadmap towards building a reliable, high-performing operation.
Supplier Spotlight
AssetWatch 60 Collegeview Rd., Westerville, OH 43081 844-464-5652 | www.assetwatch.com
Predictive maintenance has never been easier or more cost-effective, thanks to end-to-end condition monitoring from AssetWatch. With remote wireless sensors, advanced AI, and CAT III+ experts—all for a low monthly subscription—your team will have the power to conquer unplanned downtime for good. Try us risk free for 30 days, and start seeing value on day one.
RelaWorks 1328 E. 43rd Court, Tulsa, OK 74145 918-392-5058 | RelaWorks.com
Finding the right products can be difficult. Every industry and application is unique. Over-spending and guess work is common. At RelaWorks, we help reliability professionals solve this challenge. Our mission is to provide products for your unique needs and budget. Backed by Noria Corporation’s expertise and legendary customer service, we’re excited to help your reliability program succeed.
LubePM 1328 E. 43rd Court, Tulsa, OK 74105 800-597-5460 | LubePM.com
As a Lubrication Management System (LMS) engineered by lubrication professionals, LubePM helps an organization create accountability to ensure that every lubrication point is carefully maintained, inspected and measured. Ready to take your facility’s Lubrication Management System to the next level with LubePM? We’re ready to help. Simply request more information or schedule a demo.
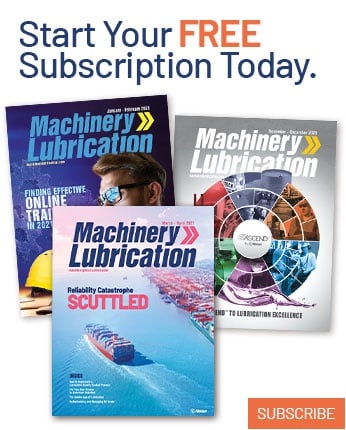