Auditing is a great way to establish a baseline understanding of maturity for your reliability functions. It involves ranking yourself against best practices, identifying what you are good at, and where you need to improve. It is an integral part of developing the action plan that will allow you to continue to mature and add value in the future.
I have seen a blend of organizations who regularly audit their reliability functions and those who don’t. For those that do audit themselves, they tend to be those that are well disciplined and operate with a steady cadence that drives value for their shareholders or owners. The results from there audits trend positively and reflect on the maturity within the organisation. This furthermore reflects in the culture within the teams, their engagement with everyday business, and the retainment of the workforce.
There are those organizations that while they regularly audit themselves and identify the gaps, the process ends there. They fail to construct an action plan that would address the gaps to create further value for them, or they fail to deploy and implement their action plan. There is no surprise then that their regular auditing results show no improvement, or worse a decline in maturity. Afterall, value is created from the improvement process by implementing the actions from the audits, not by simply completing the audit.
How to Audit Your Reliability Functions
Auditing your reliability function consist first of identifying what the best practices are within the industry and what makes it a ‘best practice’. Having a best practice doesn’t come overnight and the criteria that demonstrates best practice may only be achievable in a staged approach.
Auditing asks a series of questions on a specific reliability function topic. These topics might be related to lubrication, condition monitoring, defect elimination, asset strategy development, just to name a few. Topics can be made up of elements, and each element has a question that has a specific and measurable criterion that allows for a maturity ranking scale, like zero to four to be established. Avoid using yes/no style questions as this will limit your ability to progressively mature, or to mature to a level that your organization is happy with.
For example, the best practice of managing small lubricant containers might be…

There are no half-marks when determining your ranking score. You must satisfy a ranking in full to achieve that level of maturity. Also avoid the tendency to overstate on the truth. Nothing is gained by overstating the current condition or performance of your reliability functions. It is more likely to be detrimental in advancing them as you won’t identify the gaps and improvement actions needed to strengthen them.
How To Go About Auditing Your Reliability Functions
There are two ways to go about auditing your reliability functions.
One, appoint someone external to the business to do it. This is someone that has experience in the process, that has seen the various levels of maturity from the good to the bad, that has the auditing tools (categories, questions, rankings, etc.) and can provide a non-bias assessment. They will also come with the experience of what improvement plans and actions are best suited to the organization for them to succeed in implementation and sustainment.
Two, perform the audits yourself. If you do not already have the tools available, you will need to create them. This can be a very involved process requiring many hours of research and consultation with stakeholders and subject matter experts. If your organization already has a standard, policy, or guidance note related to for example, lubrication management, it should have the necessary guidelines and requirements that can be used in creating the auditing tools. If your organization does not have documents related to the desired audit topics, then the standard, policy, or guidance note, and auditing tool can be created together.
There is a third option. Start with option one and have the first audit completed by someone external, and then complete subsequent audits yourself once you gain an understanding for the process and the content.
The process though, whether the audit is completed by someone externally or internally, should be the same.
- Determine a timeline for audit engagement,
- Identify the people that need to be involved (i.e. who is going to be able to answer the questions),
- Identify what evidence might be needed to supplement the verbal responses (i.e. show the auditor the physical proof),
- Conduct the audit,
- Share the audit results with the organization,
- Develop and execute the improvement plan, and don’t forget to include regular reviews to understand how things are progressing,
- Lock in the date for a follow-up audit.
Benefits of Auditing Your Reliability Functions
It was previously mentioned that your organization may be happy to only reach a certain level of maturity.
The benefits of attaining ‘best practice’ in every reliability function, or any at all, needs to be understood from a return of investment perspective.
Some organizations pick and choose which areas they wish to improve and invests in because it delivers the results and value they require. They are content to not ‘gold plate’ everything they do.
Gold plating means investing in costly or nonessential items, and doing so purely for the status, rather than the need. We all like and enjoy the latest tool, technology, or trend, but do we really need it? Is it going to return any value or is it going to cost more to sustain in the long term?
The value can be a monetized return from the investment or an improvement in culture.
The monetized return is simple. Advancing the maturity of your reliability functions will have a direct impact in decreasing costs and increasing productivity. Show me a plant manager who wouldn’t want that!
The cultural aspect is recognized through the process of continuous improvement. Some employees may have come from organizations that had a higher level of maturity and they know what needs to be to improve. They will take the opportunity to engage in this process and share their knowledge and ideas. Other employees may not know what good looks like. There may be some fear related resistance to change, whereas others will be encouraged to learn and experience this growth opportunity.
The results of your audits should never be used as an employee disciplinary tool. This is an improvement tool only. While there might be instances where audit results are not improving, the leadership team need to understand the factors behind it, rather than wielding the axe. If it is linked to disciplinary action, then you may lose engagement and miss valuable opportunities for improvement.
Gains from Auditing Reliability at a Large Alloy Smelting Facility
I was involved in the auditing process of a large alloy smelting facility where we reviewed our lubrication management and condition monitoring program.
The relevant stakeholders and subject matter experts were brought together and briefed on the process and what was expected of them. They were then interviewed, which is where the questions were asked, and the assessment conducted that applied to each of them. There was also time spent in the field observing the lubrication and condition monitoring practices.
Items of note were:
- There were at times differences in scores and answers provided for the same question which depended on who we spoke to.
- Verbal feedback occasionally did not align to observations made in the field.
- There was an apprehension to admit that the lubrication and condition monitoring functions weren’t as mature as they thought.
It is likely that different scores and responses will be given depending on the person and their role. Some people will have more to do with the functions being audited and know what “really” happens, whereas others will think they know what is happening. There also will be some that won’t want to bring to light what really happens, potentially to save face. The future goal here is to have everyone aligned with what does and does not happen, and not to keep secrets.
The results of the audits conducted every six months and over a two-year period, and completing improvement plans speak for themselves and the role auditing played in elevating the maturity of two of their reliability functions.
Lubrication Management
Average scores increased each audit interval.
Audit 1: 0.57
Audit 2: 1.13
Audit 3: 1.68
Audit 4: 2.30
A total of 18 action items were identified during the first audit and completed over a two-year period.
Five additional actions were generated (two of which were completed) to build on some of the previously completed actions.

Condition Monitoring Program
Average scores increased each audit interval.
Audit 1: 0.74
Audit 2: 1.85
Audit 3: 2.10
Audit 4: 2.78
A total of 20 action items were identified during the first audit and completed over a two-year period.
Four additional actions were generated (Two of which were completed) to build on some of the previously completed actions.

Regardless of if you think you need it or not, auditing your reliability functions will identify where you sit on the maturity scale and provide guidance for improvement.
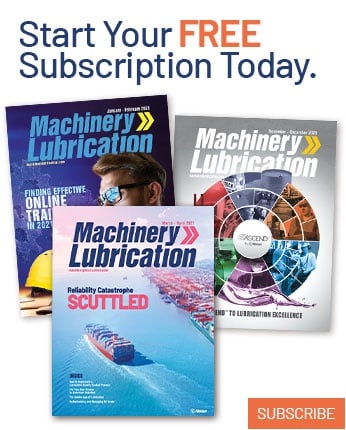