Do you remember how it felt starting on that big project you’d spent so much time preparing for? You know, the one that carried with it high hopes of success.
Well, what happened? I think you probably know the rest.
Starting a big project with high hopes only to see it wither away, lose momentum, and ultimately fail is a scenario many of us are familiar with. According to Professor Bent Flyvbjorg and Dan Gardner, authors of How Big Things Get Done, in their study of over 16,000 projects, only 8.5% hit their targets on time and within budget. This dismal statistic is referred to as the Iron Law — projects tend to go over budget, over time, and under deliver benefits.
The root causes of project failure, as discussed by Flyvbjorg and Gardner, lie in psychology and power dynamics:
- Human biases, particularly optimism and overconfidence, often lead to underestimations of costs and overestimations of benefits.
-
Additionally, the power to make a project appear more attractive on paper can lead to misrepresentations of its feasibility.
A real-world example of project failure can be seen in a company's repeated overspending and failure to meet deadlines in their project management framework. Several years ago, I was asked to facilitate an Apollo Root Cause Analysis investigation into a company’s project management framework, because in the previous three years every project had overspent and failed to be completed on time.
The investigation found more than 60 cause-and-effects into the problem. Numerous issues contributed to this failure, including inexperienced planners, insufficient funding, and poorly defined scopes of work. This pattern of project failure is not isolated to specific industries but can be observed across various sectors. Whether it's a reliability project or a safety initiative, the tendency to treat these endeavors as mere projects often leads to unsatisfactory outcomes.
To address this issue, a shift in mindset is necessary. Rather than viewing reliability improvement as a project with a finite end date, it should be seen as a cultural journey. This entails ingraining reliability into the organizational culture, similar to how safety is prioritized.
The key to embedding reliability as a culture lies in the 5A's framework: Alignment, Agreement, Adoption, Application, and Advancement:
- Alignment (Mindset): Fostering a shared mindset across the organization involves ensuring that every employee understands the importance of reliability and their role in achieving it. This can be achieved through regular communication, training sessions, and incorporating reliability goals into performance evaluations. For example, a manufacturing company might hold monthly town hall meetings where the leadership emphasizes the significance of reliability in maintaining customer satisfaction and market competitiveness. Additionally, providing case studies or success stories that highlight the benefits of reliability can help employees understand its value and align their mindset accordingly.
- Agreement (Board Buy-In): Board buy-in is crucial for ensuring that reliability initiatives receive the necessary support and resources. This involves presenting a compelling business case to the board, demonstrating how investing in reliability will lead to long-term cost savings, improved productivity, and enhanced customer satisfaction. For instance, a utility company seeking board buy-in for a reliability improvement program might present data showing the correlation between reliability metrics and customer retention rates. By involving the board in the decision-making process and addressing their concerns, organizations can secure their commitment to the reliability agenda.
- Adoption (Engage Everyone): Engaging everyone in the organization in reliability initiatives is essential for their success. This means making reliability accessible to all employees, regardless of their role or level of expertise. For example, a software company implementing a reliability engineering program might offer training workshops for developers, testers, and support staff on best practices for writing reliable code and troubleshooting issues. Additionally, fostering a culture of knowledge sharing through platforms like internal forums or lunch-and-learn sessions can empower employees to contribute ideas and solutions for improving reliability. By investing in skill development and creating opportunities for collaboration, organizations can ensure that reliability becomes ingrained in their corporate culture.
- Apply (Grow your Culture): Implementing a reliability improvement roadmap involves translating strategic objectives into actionable plans with clear roles, responsibilities, and timelines. This requires identifying key performance indicators (KPIs) related to reliability, establishing accountability mechanisms, and allocating resources effectively. For instance, a pharmaceutical company might develop a roadmap for enhancing equipment reliability in its manufacturing facilities, outlining specific maintenance tasks, training requirements, and performance targets. By aligning activities with organizational goals and monitoring progress regularly, organizations can ensure that their reliability culture continues to evolve and grow over time.
-
Advance (Reliability for Life): Integrating reliability into everyday operations requires a commitment to continuous improvement and the establishment of robust support structures. This involves implementing feedback mechanisms to capture lessons learned, conducting regular audits to identify areas for enhancement, and investing in technology solutions to automate reliability monitoring and analysis. For example, a transportation company might use predictive maintenance software to monitor the health of its fleet in real-time and proactively address potential issues before they escalate. By embracing a mindset of lifelong learning and innovation, organizations can stay ahead of evolving challenges and maintain a high level of reliability in the long run.
By fostering a shared mindset, gaining buy-in from leadership, engaging all employees, implementing improvement roadmaps, and continuously advancing, organizations can go a long way in establishing a truly sustainable reliability culture.
Treating reliability as a cultural endeavor rather than a project is essential for long-term success. By integrating reliability into everyday operations and continuously striving for improvement, organizations can minimize downtime, promote efficiency, and build a reliable and sustainable future.
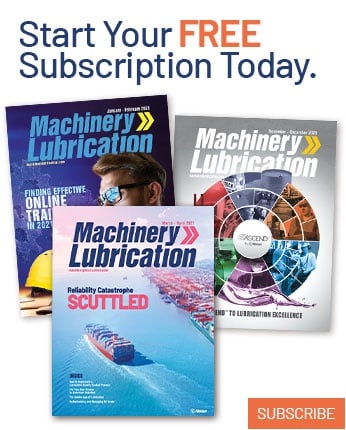